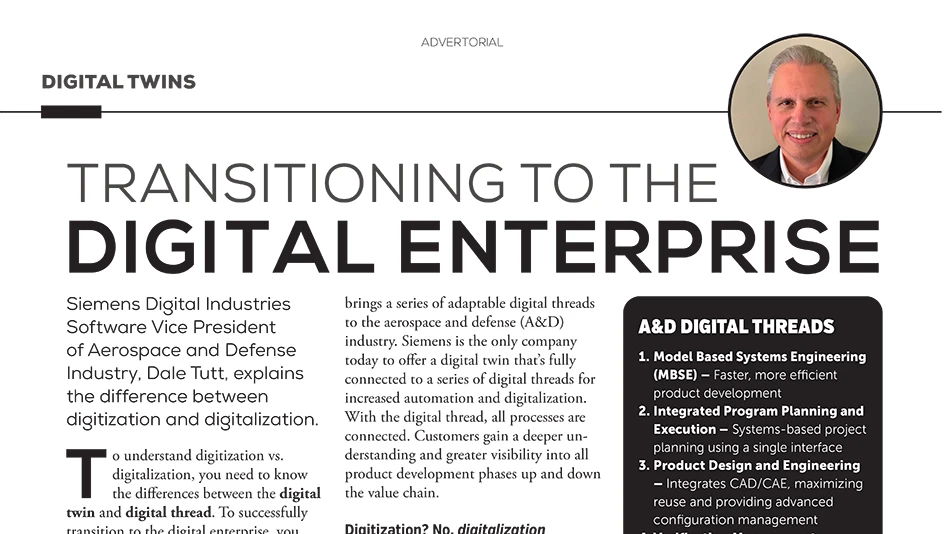
GIE Media

To understand digitization vs. digitalization, you need to know the differences between the digital twin and digital thread. To successfully transition to the digital enterprise, you need to have both.
Digital twins
The digital twin, which has been around for decades, is a virtual representation of a product or process in the proper context so teams can analyze, study, and improve the product or process under development.
A digital twin enables companies to better predict product performance and production processes prior to verification and physical production, minimizing risk. Ultimately digital twin users win new business, get to market faster, and manage costs better than their competitors.
A digital twin can do all the right things, but if it’s not connected or integrated to all phases of product lifecycle development, you’re not realizing the twin’s full potential.
You can set up a digital twin for just about anything in engineering or manufacturing. Many examples manage the digital twin and 3D CAD implementations, but you need a digital twin seamlessly connected to other digital twins or to other phases of program development for the continuous exchange of data – the enhanced automation of data – up and down the product development lifecycle.
Digital threads
The Siemens’ Xcelerator portfolio represents a comprehensive digital twin that brings a series of adaptable digital threads to the aerospace and defense (A&D) industry. Siemens is the only company today to offer a digital twin that’s fully connected to a series of digital threads for increased automation and digitalization. With the digital thread, all processes are connected. Customers gain a deeper understanding and greater visibility into all product development phases up and down the value chain.
Digitization? No, digitalization
As a company goes through its transition into a digital enterprise, it often stops short, not realizing the full benefits of its digital enterprise.
When companies begin, information is placed into a Word or Excel file. Simulation or modeling programs are started, but nothing is linked. When a user moves something from paper to a software-based program, they are digitizing that artifact. This is primarily a document-based system.
Most companies today import and translate data from external sources, but nothing is fully connected. One team may manage engineering data in one system while other teams manage production data, program management, scheduling, and tracking on different systems.
Many companies think they’ve achieved digitalization once the digital twin is in place and functioning at full maturity using 3D CAD models, simulations, etc. However, even with a virtual representation in place, there is no sharing across the product lifecycle or supply chain (hence, no fully operational digital thread).
A fully digitalized enterprise connects virtual representations or twins with a digital thread. Seamless integration of the entire value chain has been achieved. Common tasks are automated and everything’s networked together. Requirements drive entire design, manufacturing, testing, and service systems. Updates are automatically shared up and down the value chain. The digital thread connects all processes to provide integration throughout the entire lifecycle of product development. This is also where a fully mature digital twin and a fully operative digital thread come together.
Siemens provides A&D digital threads that take advantage of our Xcelerator portfolio, and when combined with our deep industry knowledge, provide a key competitive advantage for our customers.
Learn more about Siemens’ Xcelerator portfolio at https://www.sw.siemens.com/portfolio
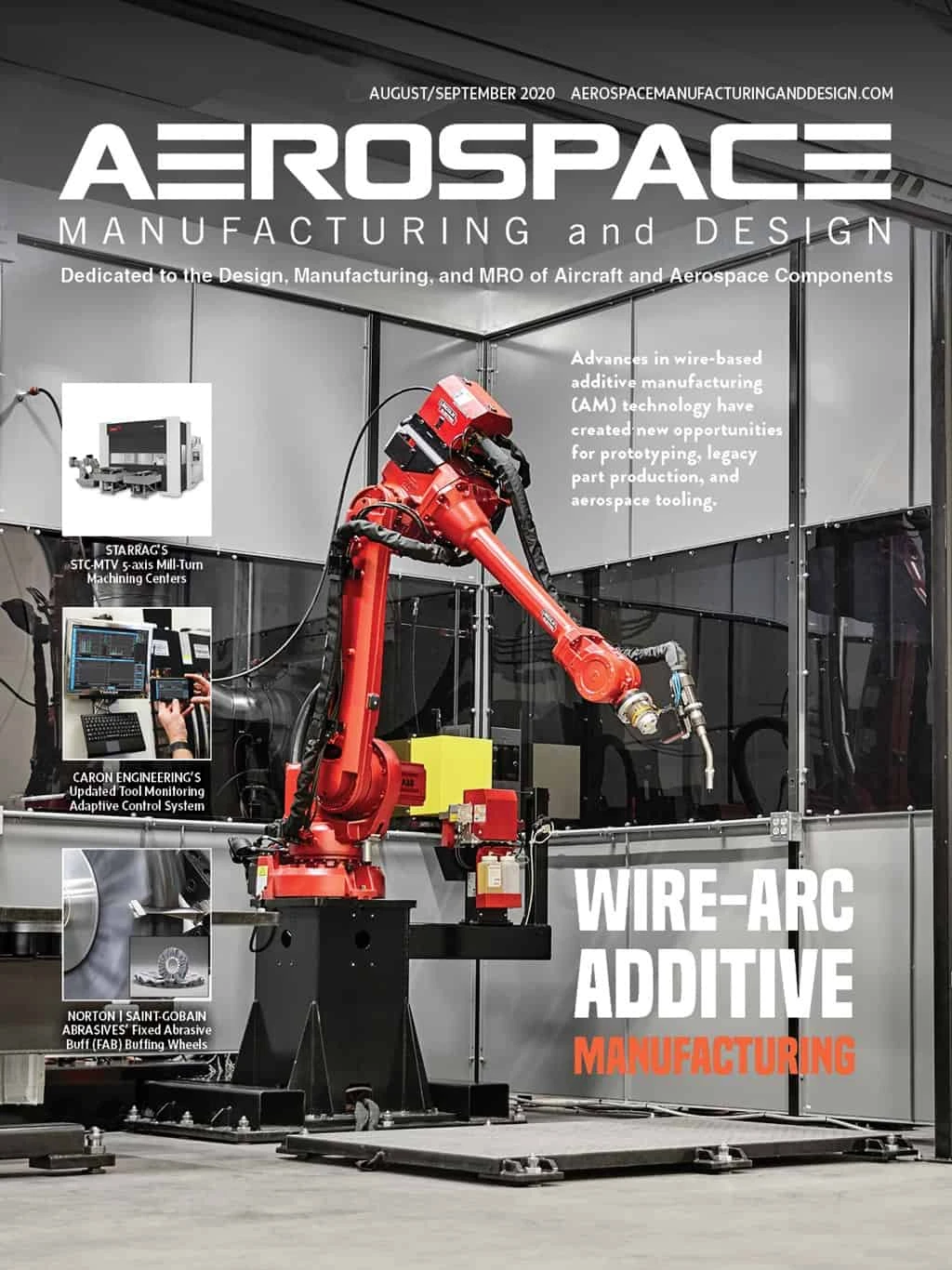
Explore the August September 2020 Issue
Check out more from this issue and find your next story to read.
Latest from Aerospace Manufacturing and Design
- Revitalizing the Defense Maritime Industrial Base with Blue Forge Alliance
- Safran Defense & Space opens US defense HQ
- Two miniature absolute encoders join US Digital’s lineup
- Lockheed Martin completes Orion for Artemis II
- Cylinder CMMs for complex symmetrical workpieces
- University of Oklahoma research fuels UAS development
- Motorized vision measuring system
- Everyone's talking tariffs