

When most people hear the words rocket science, they immediately picture something extremely complex and challenging. But when it comes to machining components for spacecraft, manufacturers who are already working in aviation, power generation, or even automotive industries might actually find themselves in familiar territory.
The materials, component features, and processes needed for spacecraft components are similar to those used in commercial aerospace and certain other industrial applications. Component manufacturers that work with aircraft discs, blisks, or casings will find entering the space market can be done without a huge additional tooling investment. But is the investment worth it?
According to a report by McKinsey & Company, the global space industry has nearly doubled since 2010, growing from $280 billion to $447 billion in 2022. The advent of private space enterprise has helped fuel rapid growth, as well as more demand for new rockets to be built – a new frontier of opportunity for manufacturers.
Entering the space market can be a great way for machine shops to diversify their business. It’s also an exciting industry that can boost a shop’s credibility and cachet. And aerospace shops may be pleasantly surprised to learn that, for now, the space industry doesn’t come with the same stringent regulations and documentation as commercial aviation markets.
Of course, there’ll be challenges. It is rocket science after all. Shops must still work with extremely tight tolerances using difficult materials such as titanium- and nickel-based heat-resistant superalloys (HRSAs), composites, or other proprietary materials that withstand extreme heat and pressure.
The good news is aerospace manufacturers can draw from the know-how they already have and apply many of the same principles to meet these challenges. Here are some ways shops can break into this exciting industry and tool up to produce a variety of space components.
Fundamentals of space component machining

A rocket engine is essentially a giant venturi system that compresses propellent and liquid oxygen in a conical combustion chamber where it’s ignited to create thrust, unlike a jet engine that pulls oxygen from the outside air. This important difference means rockets have fewer dynamic, moving parts, but they also generate more heat.
Aerospace manufacturers will find many areas of crossover in the key components of a rocket. The combustion chamber and the nozzle that expels hot exhaust are static components with similar features and materials to jet engine casings. The turbo pump that delivers fuel or oxidizer to the thrust chamber is composed of a shaft and dynamic impellers and inducers, similar to turbine discs and blisks. And structural components for the rocket will use similar composite and titanium materials used for aircraft wings and tails.
It takes a lot of force to get a rocket into space, and the materials need to withstand extreme heat and pressure. The same cutting principles for HRSAs in aerospace can apply. To avoid putting heat back into the tool, which can lead to tool failure and scrapped components, operators must use round inserts and very light depths of cut, sometimes below 10% tool engagement. They’ll also need high-pressure coolant, optimized tools, and the right CAM software to maximize process security.
Machining static rocket components

When manufacturing static parts such as nozzles or combustion chambers, shops should be prepared for time-consuming, repetitive processes on very expensive, and sometimes very large, parts. The materials for these components are often clad, usually involving Inconel (an HRSA) bonded with another metal, such as copper.
Working with cladded bimetals, which may involve two metals with very different properties, can add extra time and complexity to machining operations. This is especially true for combustion chambers, where the original equipment manufacturer (OEM) may need to reclad the component between machining stages at multiple intervals.
Shops will usually need large machines to handle the nozzles’ massive size. These components may include small grooves for coolant channels that usually require specialized cutting tools and time-consuming grooving operations that require light radial engagement.
One common error is running tools too deep for too long, which causes excessive flank and notch wear on the tool. Operators might assume they need a stronger grade, when the reality is they just need to change their approach. Shops need to rely on the same cutting principles used for other HRSAs to ensure process security, using light depths of cut and tooling with sharp geometries with physical vapor deposition (PVD) or thin chemical vapor deposition (CVD) coatings to help shear the material in turning and milling operations. This light cutting action will minimize heat and protect the life of the tool for more reliable and predictable machining.
Taking on the turbo pump
Producing the dynamic parts in a turbo pump – the inducers and impellers – gets more complicated. Like discs and blisks, these components have blades along the outer edge that require much roughing and more complex operations during the intermediate and finishing stages.
These components are smaller than their commercial aircraft counterparts, so operations will need the right tools and processes to handle all the intricate features. Solid carbide end mills will likely have a role to play in the small areas between the blades. Shops should also replace straight tools with conical tools or barrel cutters. With a barrel cutter, operations can avoid doing small axial steps into the material with incremental blends and make larger axial depths of cut to improve productivity.
To do this effectively, operations will need a stable 5-axis machine and advanced CAM software that can support these types of component features and operations. Fortunately, there are a few CAM software providers who offer specialized software packages for turbo pump machining, enabling more complex tool paths and techniques, such as trochoidal, dynamic, or adaptive milling.
Working with composites
Manufacturers working with structural components in spacecraft should expect a wide range of variability and challenges in the composite materials they use. Operations will have to consider more than the makeup of the material – such as phenolics, graphite, and glass fibers – but also the direction of the layup when developing a milling and drilling strategy. Unidirectional composite material can be a troublesome material to cut and drill. Additionally, many companies apply their own composite with the needed material composition, creating more variation in the types of composite materials shops will need to handle.
For most composite milling and drilling operations, polycrystalline diamond tipped (PCD) tools are ideal because of their high abrasion resistance. However, because of the wide-ranging variation in materials, structural component manufacturers will usually get the best performance using engineered tools and customer-specific designs for their unique challenges. Here’s where having the right tooling partner who understands the challenges of machining composite space components can be key to productive operations.

The right partnership
Entering a new market like the space economy may seem daunting, even when you’re equipped with the machines and the fundamental know-how to make the transition, so it’s important to remember you’re not on your own. With the right partnerships, operations can get the support they need to expand the business.
Networking and developing stronger relationships with OEMs will be critical to gain access to the rare, proprietary materials sometimes used in space components. The upside is it’s a rapidly growing market, so OEMs are on the lookout for new suppliers to support increasing demand.
Having an expert tooling partner that can support you throughout your journey will also help. A tool provider who knows the industry will be able to offer critical insight into tooling solutions that can greatly improve your space machining capabilities – from custom-engineered geometries to using exotic tool materials such as PCD for titanium, or cubic boron nitride (CBN) and ceramic for nickel.
The right provider will offer far more value than just tooling; they’ll give you access to a global network of experts who can support your business transition from beginning to end. From setting up tooling and CAM software to helping with engineering and testing in a secure and confidential lab environment – an expert tool partner can provide everything needed to guide your operation for success in the growing space market.
Sandvik Coromant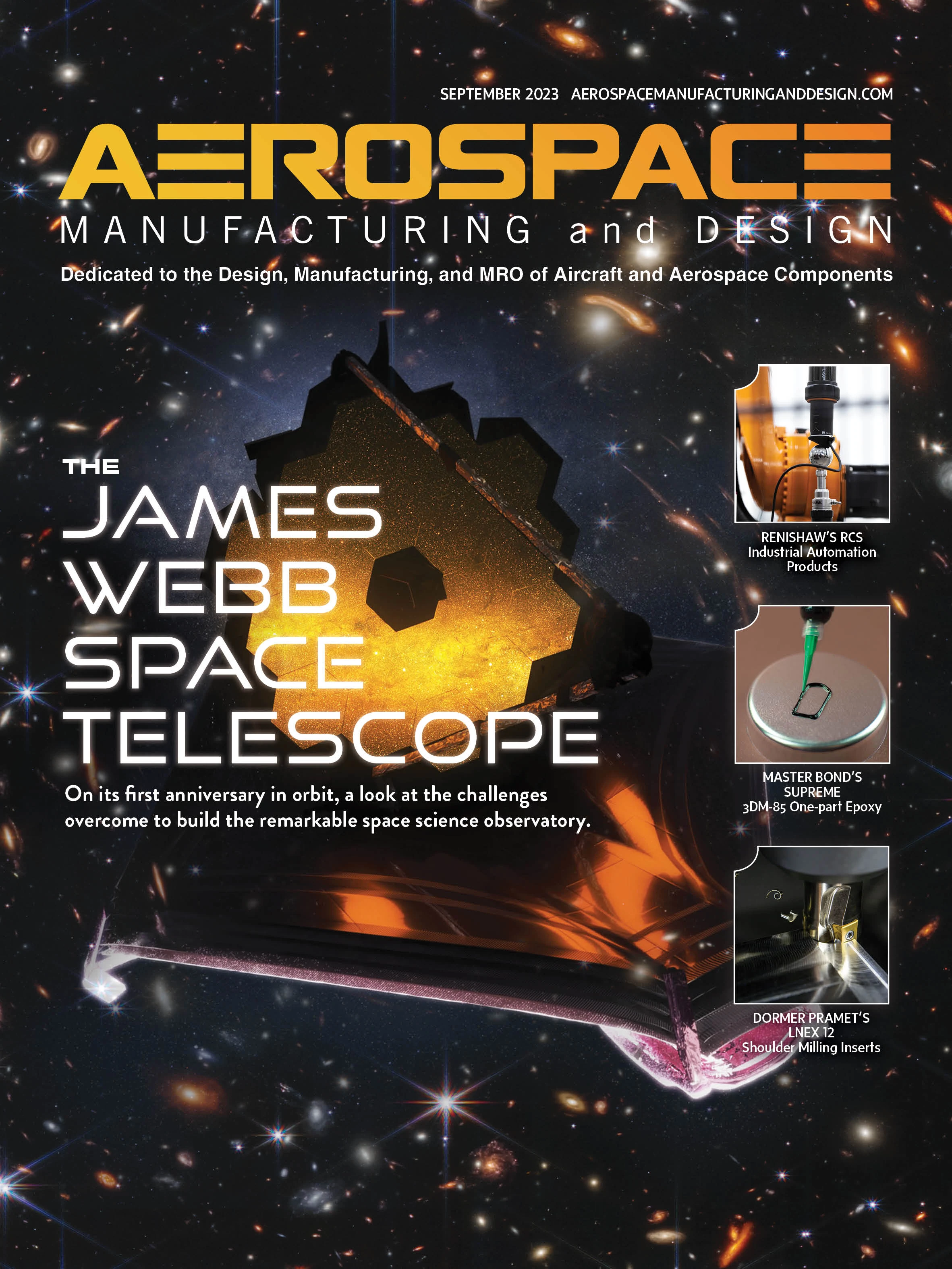
Explore the September 2023 Issue
Check out more from this issue and find your next story to read.
Latest from Aerospace Manufacturing and Design
- Solar Atmospheres of Michigan expands capabilities
- Firm, safe, efficient parts handling with non-damaging pressure
- Deutsche Aircraft rolls out D328eco test aircraft
- Laser drilling DrillOptimizer for galvo scanner systems
- #64 - Manufacturing Matters: Automation offerings with Visual Components
- Is your shopfloor connected? The importance of Industry 4.0 in manufacturing
- Reduce setup time & maintain high accuracy
- Take a lunch break, expand your manufacturing knowledge