
Part 2 of a 3-part series on the history of titanium. Part 1, in the March 2016 issue of AM&D, covered the history of the metal. Part 3, scheduled for the June issue,will discuss machine tools, cutting fluids, fixtures,and toolholders.
Anyone who’s stood in front of a lathe or machining center for any length of time knows titanium is a real bear to cut. It has several properties that make it an excellent choice for aerospace and medical components, but these same attributes may cause rapid wear for tools and nervous breakdowns for machine operators. Fortunately, the right mix of application knowledge and tooling can tackle even the gnarliest titanium. Success is largely a matter of selecting the right tools, using appropriate feeds and speeds, and generating toolpaths that protect the tool’s cutting edge and prevent shock to the workpiece, machine tool, and cutter. Here are some tips to set you on the right path:
Stay sharp
Machining tough and elastic titanium is a bit like cutting a rubbery birthday cake. Without a sharp knife, the slices will be ragged, making the partygoers unhappy. Titanium is also a poor conductor of heat, so the old machining adage “get the heat into the chips” doesn’t work so well. Since heat stays in the work zone, tools may quickly become dull, in turn causing rubbing and ultimately generating even more heat. This also causes work hardening, a common problem with titanium. Because of this, what began as an ideal cutting speed at the start of the cut may soon be too fast for the now-harder material. Tool degradation escalates, and sudden tool failure can result.
Often the best solution is a very sharp cutting tool, one with a multilayer titanium aluminum nitride (TiAlN) PVD coating and micro-grain carbide substrate. This reduces the potential for chip welding at the insert surface and provides the heat and wear resistance and edge toughness necessary for the unfavorable conditions of titanium machining. Further, positive insert and cutter geometry helps create a shearing action, reducing heat buildup and tool pressure, extending tool life.
Of course, there is no one-size-fits-all insert recommendation for any machining operation, let alone when titanium and other heat-resistant super alloy (HRSA) materials are involved. Tool life in heavy or interrupted cuts might be prolonged with a slight edge prep on the insert such as a hone or T-land, which are better at absorbing shock. Chemical vapor deposition (CVD) coatings shouldn’t be discounted either; though the cutting edges of CVD-coated inserts are typically less sharp than PVD, they perform somewhat better in the high heat and extreme pressure seen when roughing titanium.
One cutting tool material that doesn’t play nice with titanium is ceramic Titanium is very reactive in the presence of oxygen, and the thin chips and dust produced when machining it are prone to ignition at temperatures higher than 332°C (630°F). Since ceramics must be used without cutting fluid, and considering the high cutting speeds at which these tools are run, the risk of fire is fairly high. Nor is cubic boron nitride (CBN) a great choice for titanium machining; problems with binder degradation lead to rapid edge wear, notching, and chipping, quickly destroying the tool. However, CBN’s harder cousin, polycrystalline diamond (PCD), a favorite of aluminum shops, works surprisingly well in some titanium finishing operations.

Shape up
Insert geometry also plays a big factor in successful titanium machining. Round inserts work quite well, since these thin the chip and provide a wider cutting surface able to absorb heat. Be careful not to bury the tool in a corner, otherwise chatter, work hardening, and subsequent tool breakage may result. Square or polygon-shaped inserts are another option, provided the approach angle is kept at 45° or less, so that effective chip thinning can take place.
When pocket milling, a long-edge, indexable insert cutter is frequently the best bet, provided sufficient chip clearance can be maintained. If not, a high-helix end mill or exchangeable head cutter should be used. In either case, chip evacuation through a consistent flow of cutting fluid, preferably under high pressure, must be assured. Cutters with more teeth are often most effective, since titanium likes a light depth of cut (DOC) and relatively high feed rates. Also, keeping several teeth engaged in the cut at all times reduces chatter and improves tool life. Look for eccentric or double margin relief on end mills and drills – they might cost a little more but will generally last longer under titanium’s punishing cutting conditions.
Another consideration is the actual construction of the tool, especially the pockets that contain the inserts. Cutting forces with titanium are quite high. On toolholders not designed for such work, this may lead to slight shifting of the insert during heavy cuts, or when entering and exiting the workpiece. Where possible, toolholders equipped with shims beneath the insert are preferred, as these provide greater support. A robust clamping mechanism and rigid tool body also is required. Successful titanium machining depends on a stiff, high-quality machine tool and fixturing (more on this in Part III).
Get with the program
More important than incredibly long tool life is predictability. Understanding the signs of imminent tool failure is a necessary part of process control, and being able to spot tool wear before catastrophe strikes is a crucial skill. It’s better to replace a cutter or insert before its time than to scrap an expensive workpiece. Once optimum feeds, speeds, and other cutting conditions have been determined, tool life should still be monitored closely, so that wear trends can be identified early.

Success with any machining process depends on good programming techniques. The toolpaths for cutting aluminum and steel are far more forgiving than with titanium. Bury a tool in the corner of a 6061-T6 workpiece, and the power meter might spike or some small complaint could be heard from the sheet metal. Do the same thing with titanium and you may be dodging shrapnel as the cutter breaks free of the tool shank.
The rule with titanium is easy does it. Experts recommend arcing cutters into and out of the workpiece to avoid shock and abrupt movements.
Climb milling, which creates a thick to thin chip, overcomes some of titanium’s truculence. Trochoidal toolpaths maintain constant cutter engagement and reduce stress to cutting edges. In face milling applications, a racetrack pattern is preferable to multiple linear passes, since it promotes continuous cutter engagement. In this case, pre-cutting a slight chamfer on the workpiece blank at each end of the toolpath improves tool life and helps avoid shock to the machining system.
Keep feed rates as consistent as possible. Stopping in corners or against shoulders creates rapid heat buildup and work hardening. Instead, program a small radius in the corner to avoid this problem, or use a slicing or rest milling technique to clean out corners and other part features impossible to reach with large roughing tools.
Modern CAM systems boast dozens of such techniques, all of which are meant to improve productivity and increase tool life. Spiral morphing, helical and contour ramping, tangential, high-feed, and roll-in milling are just a few of the programming functions effective with rough- and finish-milling titanium. And although the canned options available for turning work are limited, lathe programmers can use many of the same principles used by their machining center counterparts.
Sadly, there’s no set of instruction manuals for titanium machining – ones that say “do this, and do that and all will be right with the world.” Pushing the boundaries with any tough materials is hard work, and titanium is no exception. It requires some trial and error, a little creativity, and above all, consistency and scientific testing methods to determine what works and what doesn’t.
Sandvik Coromant
About the author: Michael Standridge is an aerospace industry specialist with Sandvik Coromant and can be reached at 800.Sandvik or us.coromant@sandvik.com.
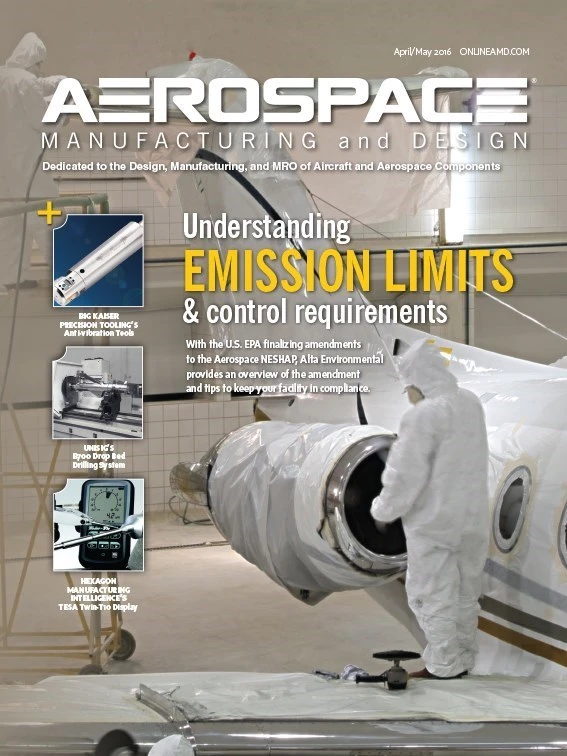
Explore the April May 2016 Issue
Check out more from this issue and find your next story to read.
Latest from Aerospace Manufacturing and Design
- AAMI project call submission deadline extended to May 12
- Jergens launches cast iron tooling column additions
- Airbus to acquire assets relating to its aircraft production from Spirit AeroSystems
- FANUC America's Cobot and Go web tool
- Chicago Innovation Days 2025: Shaping the future of manufacturing
- High-density DC/DC converters for mission-critical applications
- #59 - Manufacturing Matters: Additive manufacturing trends, innovations
- ACE at 150: A legacy of innovation and industry leadership