
Maintenance is a necessity to any manufacturing firm, with companies large and small on the lookout for new methods to increase efficiencies across the board. The importance of reducing the time it takes to bring down operating costs and downtime can’t go understated, but often these jobs are still conducted manually.
There are solutions coming to market helping engineers to reduce machine downtime during maintenance operations. Engineers previously checked the torque level of every single bolt in a piece of machinery, engine, vehicles, or other structures manually. Although solutions using ultrasonic waves can perform inspections, for many, these still aren’t to the standard required.
Maintenance processes the smart way
From our perspective, aerospace is one of the foremost vertical sectors in which maintenance, repair, and operations (MRO) processes require efficient, standardized, and safe practices. As a supplier and solutions provider solving key challenges for manufacturers within this space, we began addressing this issue a couple of years ago. It was apparent maintenance engineers needed something that would meet head-on the fundamental challenges within processes, while overcoming the shortcomings of existing solutions.
This resulted in a disruptive proof-of-concept solution called Smart Washer, a next-generation sealing technology enabling touchless and wireless measurement of bolt axial load. Instead of having to manually verify the torque level of every traditional bolt, maintenance engineers are notified about the fasteners that are too tight or too loose so they can attend to them immediately. This offers an added safety benefit as the device can reduce breakages in bolts caused by repeated over tightening during manual checks.
Designed to improve efficiencies within MRO, Smart Washer performs the fundamental role of a standard washer but uses intelligent connectivity to provide maintenance and service engineers with a clear picture of axial loads. This is achieved by incorporating a proprietary strain gage and a transmission system into the washer, which relays the information to maintenance engineers through the Smart Reader device.
Quantifiable efficiency gains for users
Currently in beta testing across customer sites, Smart Washer is already proving an invaluable asset. This is underscored by our customer, Airbus Helicopters, which noticed quantifiable efficiency gains across helicopter engine maintenance. A helicopter can require a periodic check necessitating removal of its engines and interior trim before maintenance engineers can gain access and check the bolts. Once checked, the engine must be re-installed and a ground-run undertaken to ensure correct installation. This is a labor-intensive, heavy maintenance operation that typically takes around two days and requires two engineers to check about 12 bolts. Using Smart Washer, Airbus Helicopters reported they perform the same task in about 2 hours with one engineer.
Impressive versatility
The disruptive Smart Washer technology could potentially address other sectors demanding extremely high safety standards and efficient maintenance processes.
We see opportunities in the energy and renewable resources markets, where nuclear energy companies could check radioactive waste tanks from a safe distance using a drone. Manufacturers of wind engine turbines could leverage the technology in conjunction with a drone, saving time and costs, and overcoming safety issues inherent with hard-to-access wind turbine blades. There are other examples where this solution can work, including chair lifts and cable cars at ski resorts, or high-level rides at amusement parks.
Crunching data for wider benefits The amount and level of data provided by Smart Washer that can be accessed, analyzed, and processed could enable accurate live monitoring and predictive maintenance. Tension, date, location, and temperature could all be registered.
Whether it’s an engine for an aircraft manufacturer, wind turbine, or amusement park ride, companies could be alerted if there’s a requirement to perform maintenance for a sudden and immediate issue or according to schedule.
While maintenance may prove to be a challenging area of most businesses, those adopting and onboarding advanced, efficiency-enhancing solutions are seeing a drastic reduction in time and costs. What used to be a thankless and tedious task can now be a simpler, streamlined process.
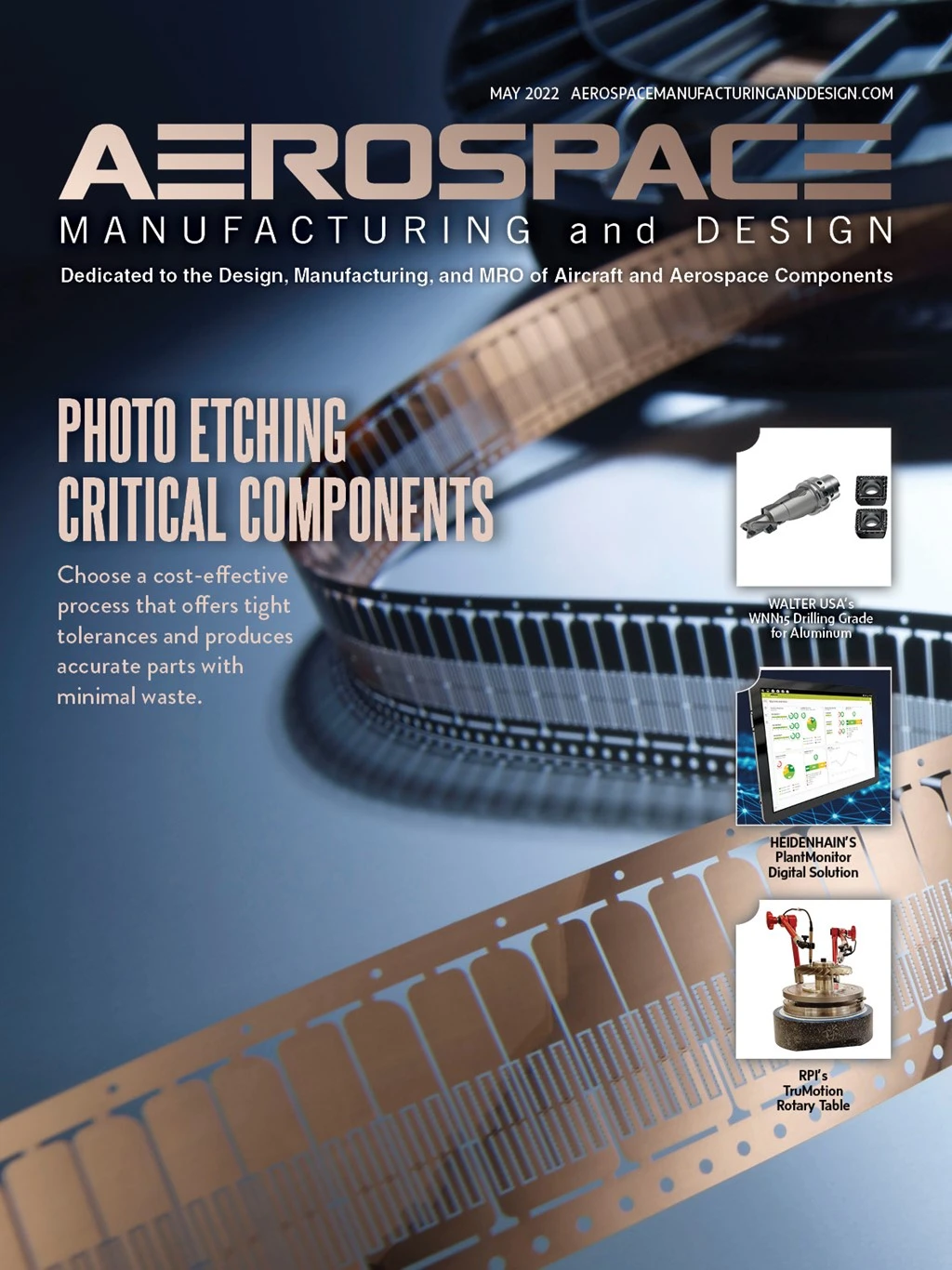
Explore the May 2022 Issue
Check out more from this issue and find your next story to read.
Latest from Aerospace Manufacturing and Design
- AAMI project call submission deadline extended to May 12
- Jergens launches cast iron tooling column additions
- Airbus to acquire assets relating to its aircraft production from Spirit AeroSystems
- FANUC America's Cobot and Go web tool
- Chicago Innovation Days 2025: Shaping the future of manufacturing
- High-density DC/DC converters for mission-critical applications
- #59 - Manufacturing Matters: Additive manufacturing trends, innovations
- ACE at 150: A legacy of innovation and industry leadership