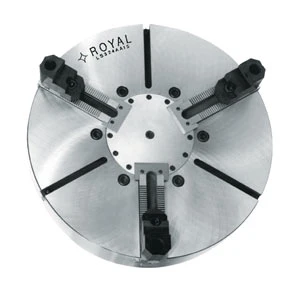
There are many chucks manufactured 50 years ago that are still working today and making quality parts. However, when, or if, a chuck begins to perform improperly, you must make an important decision to repair, recondition, or replace the defective unit. And there are many considerations to evaluate in making that decision.
Obviously, safety considerations are first and foremost in determining the overall results you are looking to achieve. Then, you must decide whether the chuck has to operate for a short period of time or for a long period of trouble-free use. And, most importantly, how will the cost difference of each of the three "R's" effect your decision?
Now, let's look at your reasons to consider repairing, reconditioning, or replacing the chuck:
- Does the chuck visibly appear worn?
- Has an accident broken something in the chuck?
- Has the chuck begun to lose its gripping force or its accuracy?
- Is the Chuck design incapable of holding a part to meet your part process and tolerances?
If the answer to any of these questions is yes, then you should consider the three "R's."
Repairing
Usually, this is the least expensive service and the quickest to get you back in production. If there is a broken master jaw or broken jaw activator, caused by an accident, then replacing the broken part, and cleaning up some damaged surfaces can make the chuck serviceable at little expense. However, an exception to this service is when the broken part is a special part. Then it may have to be reverse engineered and manufactured, which is more time consuming and costly. The repairing procedure provides a very serviceable chuck returned to its original condition prior to breaking. However, the repaired chuck is still a somewhat worn chuck with a warranty only on the replaced parts and workmanship. Replacement parts may not have the same fit with worn parts, which in turn may not provide the best situation for holding parts.
Reconditioning
This is the midrange expense of the three "R's" and is recommended when the cost of reconditioning is 60% or less of the price of purchasing a new chuck. A correctly maintained and lubricated power chuck will usually age gracefully and will only show wear by loss of accuracy and/or gripping force. When sent in for an examination and/or testing, all the major wear surfaces will be inspected. If they are found to be worn, they will require rebuilding of one form or another.
The forms for building up worn surfaces are either chrome plating or welding. After the worn surfaces are built-up and the parts are carefully checked for any possible cracks, the new surfaces are ground to likenew chuck tolerances. Master jaws are also qualified to like-new chuck tolerances.
Once an original chuck has been reconditioned to new chuck standards, it usually has a one year warranty (the same as a new chuck), and for most situations is equal to new chucks in reliability.
Reconditioning usually can be done in half the time it takes to have a new chuck built. It may be such that a part has to be replaced, welded or plated; however, you have most of the chuck already completed. It is important to note that replacement chucks still retain the old chucks' design with any problems and/or deficiencies inherent to the old design. Any desired changes usually require replacement.
Replacing
Quite often the cost of reconditioning exceeds 60% of the cost of a new chuck or it's simply time to update and replace with a new design. The new chuck will have all the advantages of the latest designs and materials plus many times your operations have changed and you require redesigns to improve performance. In addition to receiving a full one year factory warranty, possible considerations for selecting new chucks are:
1. The need to operate chucks at a higher rpm. Today's selection of coated carbide tooling requires much higher speeds and feeds than before. Current designs take high speed into consideration, using counterweights and counter centrifugal mechanisms.
2. The additional travel required in master jaw strokes. The usual stroke of a standard chuck is 3/8" per jaw, which in most cases is substantial. However, with the long stroke chucks this can be up to 1" per jaw. This permits gripping parts where a flange may have restricted gripping only a certain area, which may not be the ideal situation. Also, the longer stroke will allow the gripping of more part diameters with the same set of jaws, thus reducing setup time. With automation, the long stroke chuck allows part to be loaded more easily and also permits chips to escape more easily.
3. The ability to mount locators on chuck facings. Newer chuck models allow locators or locator bungs to be mounted on the face of the chuck, which provides a stationary repeatable flat surface for the part to locate. Usually the locating face is on the moving top jaw and may yaw when clamping, giving inconsistency from part to part.
4. Adding new options such as part sensing, chip blasting, and automation. Today, in order to stay competitive, many companies have to run "lights out" with robots or automation. Monitoring the chucks actions is critical to preventing a problem that would shut down the process. Feeding air pressure through the locating surface is a common way to detect if a part is not located properly. A drop in air pressure signals that the part is not seated properly, allowing the air to escape. Air may also be fed through the spindle to blow off chips from the mounting surface and part. Today, sensors can be used to indicate clamp/unclamp, part location, and clamping pressures.

Before deciding whether to repair, recondition or replace a defective chuck, companies can initially contact Royal Machine & Tool for suggestions and it may even be recommended that the chuck be forwarded to the factory where they provide a free evaluation and proposal.
Making the right decision is critical and it's beneficial to ask the assistance of a knowledgeable vendor in guiding you to make this most important decision. The decision must be based on what is functionally and financially best for your situation - repairing, reconditioning, and replacing all have their place.

Explore the May June 2008 Issue
Check out more from this issue and find your next story to read.
Latest from Aerospace Manufacturing and Design
- 2024 Favorites: #5 Article – Solving workforce issues with digital transformation
- 2024 Favorites: #5 News – GE Aerospace is investing in manufacturing
- 2024 Favorites: #6 Article – Mastering complex precision machined parts
- 2024 Favorites: #6 News – Boeing to acquire Spirit AeroSystems in $8.3B deal
- Season's greetings
- 2024 Favorites: #7 Article – Deep drawing aerospace components
- 2024 Favorites: #7 News – GKN Aerospace completes sale of St. Louis facility to Boeing
- 2024 Favorites: #8 Article – Beyond uptime