
Supply chain challenges continue to plague the manufacturing industry. John Rutledge, one of President Ronald Reagan’s economists, warned the COVID-19 pandemic will continue to disrupt global supply chains well into 2023. The aerospace manufacturing industry is no stranger to these issues, especially as Markets Insider reports aluminum prices hit 10-year highs as the supply chain fails to meet surging demand. Aerospace manufacturers must find new strategies to better respond to rapidly shifting supply chains and labor availability. Manufacturers such as CMS, Hangar One, LISI Aerospace, and JJ Churchill have turned to strategies such as 3D printing to move more operations in house and speed up manufacturing.
Keeping business in house
By keeping business in house, aerospace manufacturers can have direct control of their supply chain. CMS, an airline and aviation company based in Conroe, Texas, works on entertainment systems for luxury private and business jets. Its one-off projects often involve replacing or repairing aging cabin systems that include discontinued parts. These projects are time and labor intensive, needing on-the-spot modifications. All aircraft materials must be thoroughly tested and 100% traceable to qualify for FAA approval.
CMS solved the need for on-demand, unique parts by purchasing 3D printers. On one aircraft, the CMS team 3D-printed at least 100 different parts using the Markforged X7 printer. By keeping much of its business in-house, CMS reduced the number of steps in its supply chain, also reducing cost and turnaround time.
Another aerospace manufacturer and maintenance company, Hangar One Avionics, based in San Diego, California, specializes in completions of law enforcement and special mission aircraft for global customers including Airbus Helicopters, Bell, Cessna, and MD airframes. Many of its customers require low production or one-off custom parts to increase cockpit safety and convenience. Prior to adopting 3D printing, the team relied on time consuming, conventional machining methods, with up to a 65% scrap rate.

Faced with the challenge of making a center console for a fixed-wing Cessna, Hangar One implemented a 3D printer that printed the console in record time and enabled the team to add further customizations such as cupholders, a niche for the pilot’s keyboard, and disconnects for hand controllers and USB chargers. By taking its business in-house with 3D printers, the team could take control of its supply chain.
Faster manufacturing
3D printing also leads to quicker turnaround times, allowing manufacturers to take more jobs and spend more time focusing on their business.
LISI Aerospace is a global specialist that manufactures assembly solutions and aircraft engine and structural components. From its plant in Rugby, U.K., it manufactures fasteners for clients including Airbus and the civil aircraft market. Most of the fasteners are produced in titanium, but a small percentage are produced in steel. LISI Aerospace faced a challenge with numerous variants within each product category. The company implemented composite 3D printers and had quicker problem-solving and higher productivity with less damage, waste, and downtime for manufacturing high-quality aerospace fasteners. Adding 3D printing made it quicker for LISI to introduce new fastener variants to their product line. The LISI team creates custom tooling for new products without the additional risk of traditional tooling lead times, which can be up to nine months.

Another aerospace manufacturer which manufactures more quickly with 3D printing is JJ Churchill, a precision aerospace manufacturing and engineering firm. In manufacturing jet engine turbine blades, the team found traditional methods using coordinate measurement machine (CMM) fixtures involved multiple roughing and refining operations, slowing iteration and increasing machining wait times. It required enormous time and machining cost because fixtures needed to be highly accurate, repeatable, and strong.
By implementing 3D printers, JJ Churchill could produce complex custom geometries for efficient, secure workholding of valuable low-volume parts. Combining custom 3D printing with off-the-shelf parts enabled the team to streamline production and improve functionality. Now, the team can design and test fixtures within the same week, with lower material waste and exceptional quality and precision – saving 70% of its time and 80% of its cost.
The supply chain makes headlines every day. While we can’t totally predict what new challenges manufacturers will face tomorrow, we can be certain that a new day will bring new bottlenecks, supply constraints, or shifting consumer demand. Aerospace manufacturers that can most quickly adapt their processes for the environment will be the ones to survive, and thrive, in the face of uncertainty.
Markforged
Get curated news on YOUR industry.
Enter your email to receive our newsletters.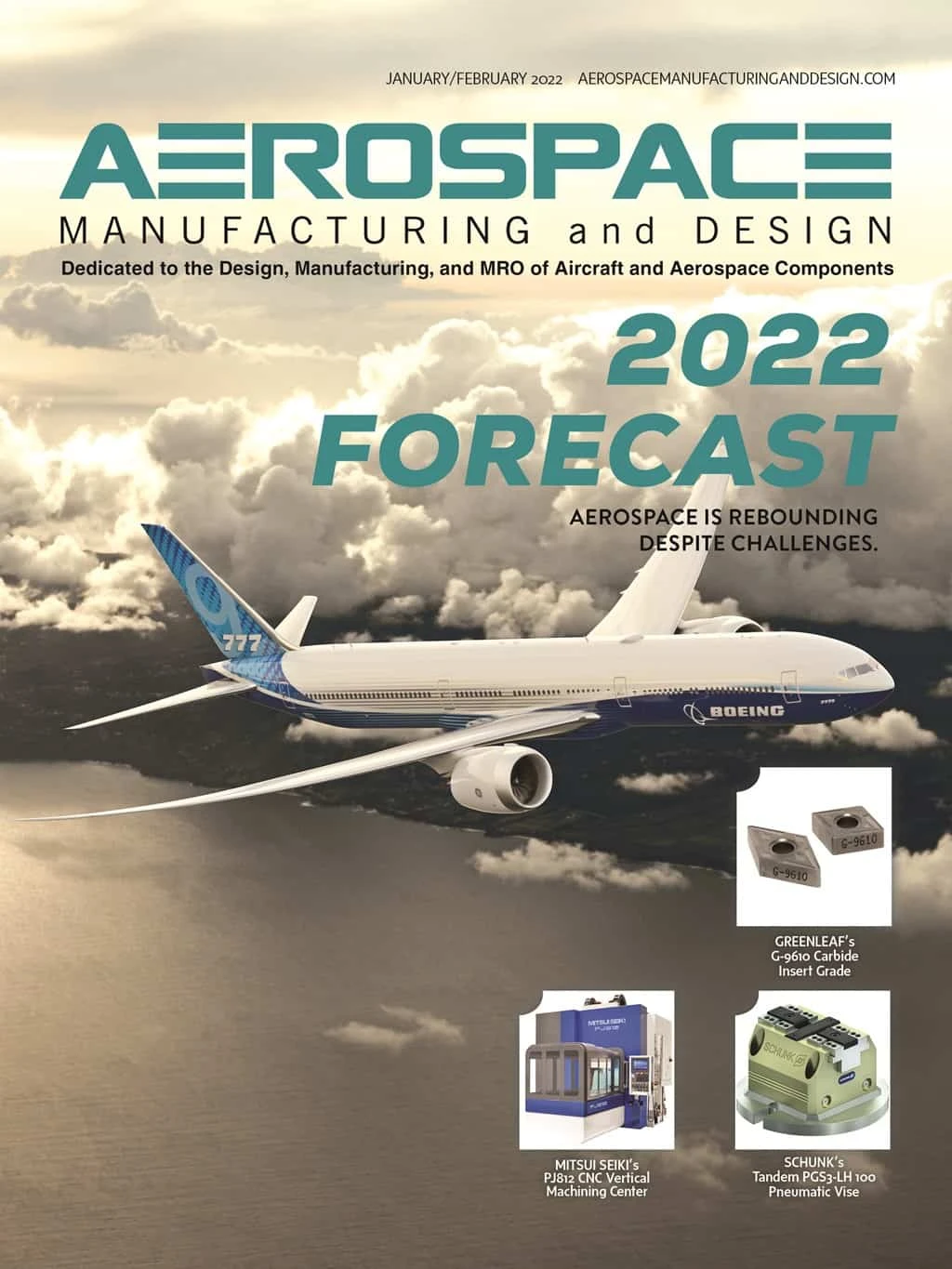
Explore the January February 2022 Issue
Check out more from this issue and find your next story to read.
Latest from Aerospace Manufacturing and Design
- GE Aerospace awarded subcontract for FLRAA next phase
- KYOCERA Precision Tools publishes 2025-2026 Indexable Cutting Tools Catalog
- BOC Aviation orders 120 Airbus, Boeing jetliners
- Mazak’s INTEGREX j-Series NEO
- Embraer tests wing for new technologies demonstrator
- Mitutoyo America’s SJ-220 portable surface roughness tester
- #55 - Manufacturing Matters - A Primer on Defense Contract Manufacturing
- Registration is open for April’s Manufacturing Lunch + Learn!