
Today the aerospace manufacturing sector is being driven by rapid advancements in sophisticated technology. Among the most significant contributors to this modernization are digital twins, 3D artificial intelligence (AI), robotics automation, and immersive reality technologies. These innovations aren’t merely enhancing traditional aerospace manufacturing processes but are fundamentally altering how the industry approaches production, quality control, and overall operational efficiency.
Bridging the physical and digital worlds
Digital twin technology has emerged as a game changer, providing aerospace manufacturers with a virtual replica of physical assets, systems, or processes. This technology allows for real-time monitoring, simulation, and optimization of manufacturing operations, leading to significant improvements in efficiency and productivity.
In the aerospace industry, digital twins enable manufacturers to simulate the entire production process, from design to assembly. By creating a digital counterpart of an aircraft, engineers can test different design iterations and manufacturing processes without the need for physical prototypes. This accelerates the development cycle and reduces costs and material waste.
Similarly, digital twins can also be used to monitor the health of aircraft components. Sensors embedded in the physical parts send real-time data to their digital counterparts, allowing for predictive maintenance and reducing the risk of unexpected failures. This technology ensures higher safety standards and prolonged lifespan of critical components.
Revolutionizing design and production
3D AI, which combines three-dimensional modeling with artificial intelligence, is another pivotal technology reshaping manufacturing. This convergence allows for the creation of highly detailed and accurate 3D models, which can be analyzed and optimized using AI algorithms.
3D AI-driven generative design algorithms can create lightweight, optimized structures that maintain strength while reducing weight, which is crucial for aerospace components. AI models can then simulate physical conditions and stress tests on 3D models, identifying potential issues before physical prototypes are built. This accelerates the design process and reduces costs.
Enhancing efficiency and precision
Robotics automation has been a cornerstone of manufacturing for decades, but recent advancements are taking it to new levels. Modern robots are more intelligent, flexible, and capable of performing complex tasks with greater precision.
In aerospace manufacturing, precision is paramount. The slightest error can have catastrophic consequences. Robots, with their unparalleled accuracy and repeatability, are modernizing the way aircraft and spacecraft are built. Advanced robotic systems are being used to automate intricate assembly tasks, such as drilling, welding, and fastening. These systems ensure components are assembled with exact precision, significantly reducing the likelihood of human error.
Moreover, robotics automation helps streamline production processes, leading to increased efficiency and reduced lead times. Collaborative robots (cobots) work alongside human operators, taking over repetitive and physically demanding tasks. This collaboration speeds production while allowing human workers to focus on more complex and strategic activities.
Transforming training and maintenance
Immersive reality technologies, including virtual reality (VR) and augmented reality (AR), are offering new ways for manufacturers to train employees, conduct maintenance, and enhance overall operational efficiency.
VR is being used to train operators and maintenance personnel. By simulating real-world scenarios in a virtual environment, workers can gain hands-on experience without the risks associated with on-the-job training. This improves skill levels and reduces the likelihood of accidents and equipment damage.
AR is playing a crucial role in maintenance and repair operations throughout aerospace manufacturing. For instance, AR headsets provide technicians with real-time information and guidance, overlaying digital instructions onto physical equipment. This enables faster and more accurate repairs, minimizing downtime and operational disruptions.
Synergy of technologies
The true potential of these technologies is realized when they converge to create a smart factory ecosystem. In such an environment, digital twins, 3D AI, robotics automation, and immersive reality technology work in unison, enabling a seamless flow of data and operations.
Consider the impact on today’s smart factories. Digital twins provide a virtual replica of the entire production line, 3D AI optimizes the design of aircraft components, robotics automation ensures precise and efficient assembly, and AR assists maintenance teams with real-time information. The result is a highly efficient, flexible, and resilient manufacturing operation capable of quickly adapting to changing market demands.
The integration of digital twins, 3D AI, robotics automation, and immersive reality technologies is modernizing manufacturing across aerospace. These advancements are driving significant improvements in efficiency, precision, and sustainability, while also enhancing safety and operational flexibility. As these technologies continue to evolve, they’ll undoubtedly unlock new possibilities and further transform the manufacturing landscape, paving the way for a future where smart factories are the norm and innovation is the key to competitiveness. The manufacturers who embrace these technologies today will be the leaders of tomorrow, setting new standards for excellence in industrial operations.
GridRaster Inc.
https://gridraster.com
NEWS AND PRODUCTS
Automated surface conditioning solutions

Autobrade, a new subsidiary of Dynabrade, is dedicated to robotic integration of automated surface conditioning solutions and innovative process improvements for industries. Autobrade aims to revolutionize industrial automation and efficiency of material removal and surface treatment applications.
Its mission is to design innovation into success by automating surface conditioning processes, saving companies significant time and money.
Dynabrade
https://www17.dynabrade.com
Electric linear actuators

Electrak LL line of electric linear actuators features 600km of maintenance-free life and 100% duty cycle performance to get absolute position feedback, CAN bus integration, reduced current flow, and higher speeds.
In addition to resistance against environmental hazards, the high-duty-cycle electric actuators offer more electronic control options.
The long-life architecture is helped by a brushless motor, a high-load ball screw assembly, a brake solution that doesn’t wear, and IP69K (static) and IP66 (dynamic) compliant sealing. This enables duty cycles up to 100%, up to 600km of travel life, and up to one million cycles – more than 10x that of electromechanical actuators without these features. The new configuration options augment durability with advanced control, integration, higher voltage, and higher speed options.
Absolute position information enables instantaneous, exact reading of position for advanced control logic.
Absolute position measurement doesn’t require mechanical contact, minimizing wear to the system.
Thomson also has added a 2kN (450 lb) load option to handle higher speeds with longer service life.
Thomson Industries Inc.
https://thomsonlinear.com
Machine tool drives

Redex USA drives for machine tool applications feature preloaded rack & pinion solutions for linear axis drives, ring gear and pinion for rotary axis drives, and 2-speed spindle drive gearboxes providing constant power to the spindle. Redex rack & pinion dedicated reducers provide high stiffness and work with DualDRIVE mechanical and TwinDRIVE electrical preloading technologies to eliminate backlash and ensure precise positioning over the entire axis length. Enhanced gearing solutions feature minimal transmission error for smooth operation and low noise while providing an excellent surface finish when driving machine tool axes. SRP+ and KRP+ rack & pinion dedicated reducers offer 7% to 40% greater torque capacity compared to previous versions. The Dual KRP Rack & Pinion Drive features a closed-loop system combining two KRP reducers and a DualDRIVE mechanical preload to eliminate backlash. Only one motor is required to drive the axis. The MSR High-Torque VTC Table Drive combines two identical right angle two-speed gearboxes equally sharing the driving torque during turning. This turntable drive delivers precise, C-axis motion without backlash for milling and drilling operations.
Redex USA
https://redexusa.com
Get curated news on YOUR industry.
Enter your email to receive our newsletters.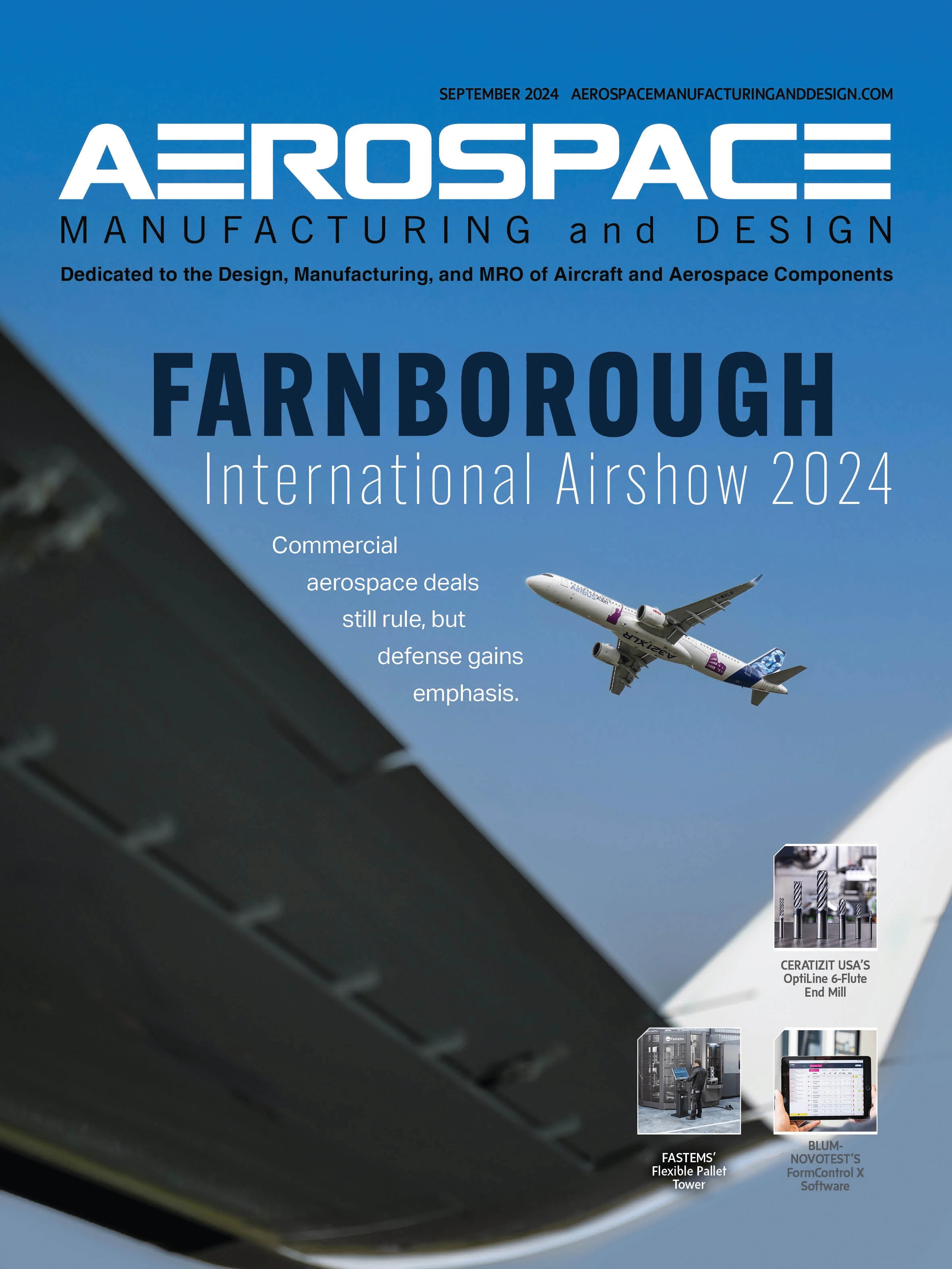
Explore the September 2024 Issue
Check out more from this issue and find your next story to read.
Latest from Aerospace Manufacturing and Design
- AAMI project call submission deadline extended to May 12
- Jergens launches cast iron tooling column additions
- Airbus to acquire assets relating to its aircraft production from Spirit AeroSystems
- FANUC America's Cobot and Go web tool
- Chicago Innovation Days 2025: Shaping the future of manufacturing
- High-density DC/DC converters for mission-critical applications
- #59 - Manufacturing Matters: Additive manufacturing trends, innovations
- ACE at 150: A legacy of innovation and industry leadership