

Since 1984, NSK America Corp., a fully owned subsidiary of NSK Nakanishi, has been the leader in high-speed spindle technology. Here we describe why you need to upgrade to a high-speed spindle system for your micromachining operations.
1 Speed.
The key to high-speed machining is the ability to achieve the tool maker’s recommended surface speed for the micro tool. Running a micro tool at a speed below the manufacturer-recommended speeds causes rubbing instead of cutting, poor surface finish, excessive chip load, and premature failure of the cutting tool. The smaller the diameter of the cutting tool, the more rpm you need. Cutting tool manufacturers recommend the cutting speeds for their tools in surface feet per minute (sfm), but the calculated rpm depends on the diameter of the tool. Example: 250sfm for a 0.500" diameter tool is 1,910rpm. That same 250sfm for a 0.020" tool is 47,750rpm. If you don’t have a machine tool that can run that fast, you’re going to need a high-speed spindle.
2 Accuracy.
Nakanishi spindles have a maximum run-out of 1 micron. Nakanishi’s standard collets have a guaranteed total indicator runout (TIR) value of 3 to 5 microns, and High Accuracy collets in select sizes with a guarantee of 0 to 2 microns. This equates to 0.00020" (or 0.00008" for High Accuracy collets) TIR. When running at speeds of 25,000rpm to more than 150,000rpm, with run out values of thousandths, you’re writing a prescription for failure. Micro tools will not tolerate run out.
3 Vibration.
Sound generated by a spindle and tool is transformed into vibration. This vibration causes poor surface finish, a loss of tool longevity, premature spindle bearing failure, and excess heat. Accessory units such as speeders, coolant driven spindles, and air driven spindles all tend to be sources of vibration, due to their structural composition. Vibration will often cause a breakdown of the substrate of the micro tool. High-speed electric spindles offer minimal vibration.
4 Heat.
Heat is generated by vibration and high rotation speeds. Friction-generated heat reduces bearing longevity and causes thermal distortion, or spindle growth. Nakanishi’s Modular and Integral Spindles and Motors use ultra-precision, greased ceramic bearings and a small amount of dry air to cool the spindle and bearings to eliminate heat generation and thermal distortion. These attributes also allow for extended machining time without harming the spindle, while maintaining smooth and accurate micro machining.
5 Longevity.
Using a Nakanishi High-Speed Integral Motor Spindle allows for the 24/7 machining often required for mold finishing, surfacing, or micro drilling. Its superb speed and accuracy combined with the absence of heat and vibration promote spindle longevity. Not needing the machine’s main spindle to rotate at maximum RPM for prolonged periods also increases its longevity. It’s a win-win situation.
For more information: NSK America Corp.

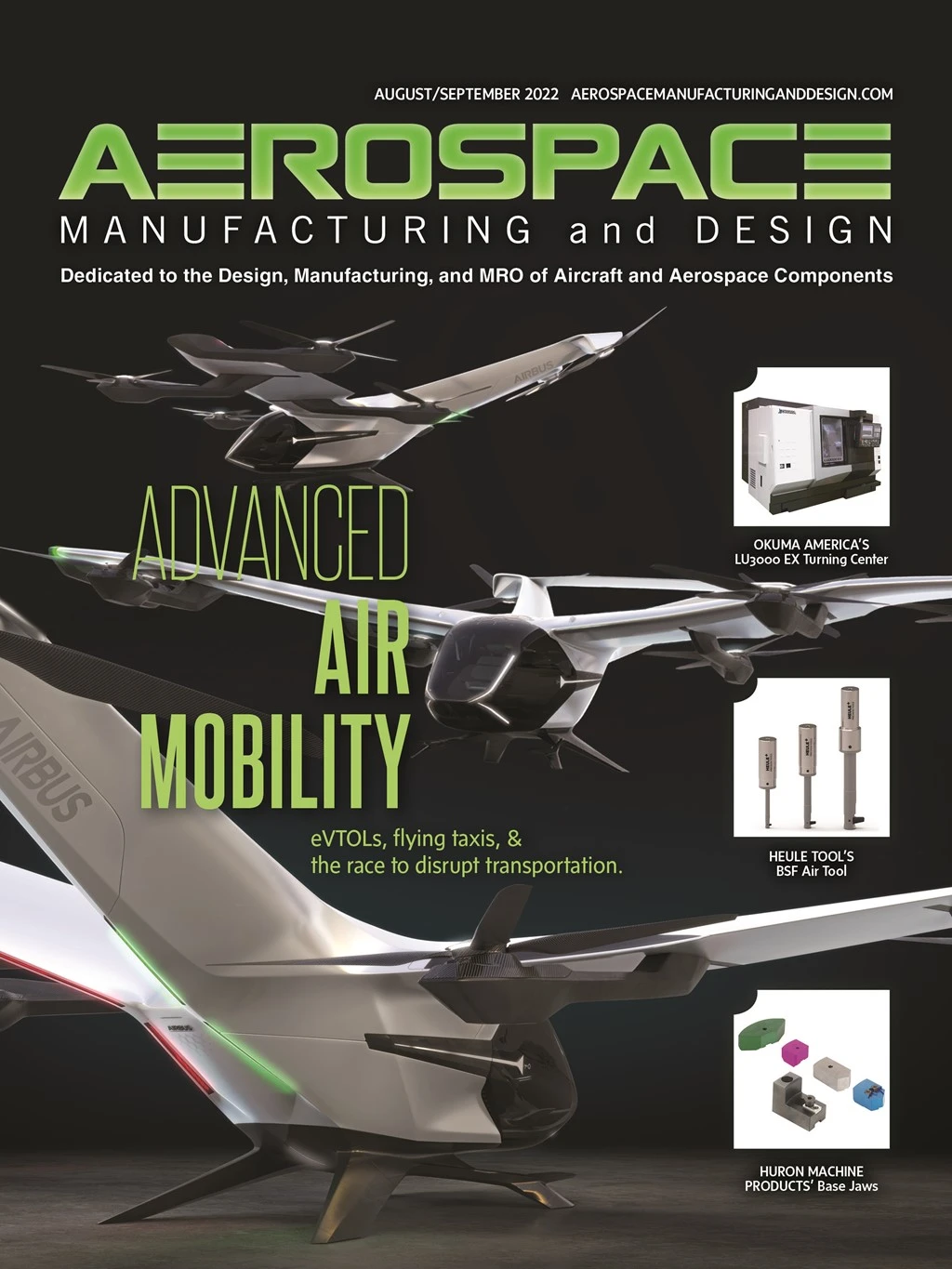
Explore the August September 2022 Issue
Check out more from this issue and find your next story to read.
Latest from Aerospace Manufacturing and Design
- Taiwan’s China Airlines orders Boeing 777X passenger, freighter jets
- Reamer re-tipping extends life of legacy tooling
- Revitalizing the Defense Maritime Industrial Base with Blue Forge Alliance
- Safran Defense & Space opens US defense HQ
- Two miniature absolute encoders join US Digital’s lineup
- Lockheed Martin completes Orion for Artemis II
- Cylinder CMMs for complex symmetrical workpieces
- University of Oklahoma research fuels UAS development