
L&L Machinery Industry Co. Ltd.
Taiwan machine tool builder APEC focuses on 5-axis machining of aerospace composites

Works with customers to develop optimum solutions for efficiently producing large components regardless of the material.
Carbon fiber-reinforced plastics (CFRP) are the trend in aerospace. Although the composite material is light and thin, it’s difficult to cut, which makes the yield poor and produces harmful dust during cutting.
APEC offers several excellent solutions for CFRP material processing. The CM4050 5-axis machine, designed specifically for aerospace composite materials processing, features box-in-box thermal symmetry and an ultra-low center of gravity structure for excellent rigidity and stability in machining. It’s also equipped with special spindle and 2-axis head, dust suction hood, automated pallet exchange systems (up to 4m x 5m table size), and intelligent systems for tool and production management.

Canada’s top aerospace manufacturer chose APEC after two years of evaluation – the first Taiwan-made precision machine to be used in the prime and Tier 1 aerospace supply chain.
More than machines
“APEC can offer a complete product portfolio for the diversity of aero-structure parts and engine parts, based on our 20 years of experience. We have solutions for manufacturing long, slim parts; skin panels; or belly fairing parts in a composite structure, in sizes from 10m to 22m,” says Matt Chang, APEC’s director. “Whether the material is titanium or aluminum for fuselage or wing structure, or aero-engine parts from blisks to engine casings, we have machine tools that meet the different requirements for each.”

APEC has machines available now, but the company also can meet a customer’s special requirement with turnkey solutions, flexible manufacturing systems, or intelligent manufacturing options. Its application engineers can calculate productivity and suggest which type of machine and spindle a customer should select, or how best to collect big data during operations or inline monitoring.
“We focus on high-end machines and high-end applications, so we only make 5-axis machines,” Chang says. “I’m very serious about being 100% responsible for customer service. Reducing downtime is important, so I can replace a spindle within one day.”
L&L’s multi-function CNC lathes are built for processing aerospace parts
From design to components, the Taiwanese company’s machines meet rigorous standards.

1 High rigidity & high efficiency
Difficult-to-machine aerospace parts require high-rigidity CNC tools with a cutting spindle offering constant torque output in a wide speed range. L&L CNC lathes meet these demanding requirements with their spindle design, coil winding, cooling and lubrication system, sealing, bearings, and one-piece Meehanite cast base.
2 High precision & high dynamic response
A machine tool’s dynamic performance greatly affects machining accuracy, so L&L offers a fully closed-loop feedback system with a grating ruler and a stable static-pressure guide rail to guarantee repeatable positioning. The servo feed’s high acceleration and short positioning and start-up time adjust spindle vibration, drift, and temperature in real time to retain accuracy.
3 High reliability & high precision retention
L&L lathes’ swing head bevel-and-worm gear increases contact surface to disperse loads and slow wear. Shock absorption and water-cooling dampen vibration and reduce cutting deformation. Overload cutting protection sensors on the table and feed shaft protect the machine tool from sudden stops. The spindle’s hydrostatic bearing (ceramic ball) minimizes wear.
4 Powerful cooling & green processing environment
_fmt.png)
L&L CNC lathes ensure good cutting cooling, from internal cooling to water- and oil-based high-pressure external cooling with easy switching, to available oil mist lubrication, liquid nitrogen cooling, and dry cutting dust collection.
5 Convenient operation & easy maintenance
Accessibility for loading, unloading, clamping, and alignment is made easier by L&L machines’ large-sized doors and optimally place observation window. A wide chip conveyor evacuation port ensures chip removal with no dead zone. Components requiring regular maintenance are easy to reach and replace.
Esme Chen, L&L service department sales manager, explains that monitoring machines and processes is easier now because of virtual reality. “We use the visual narrative to show a customer what’s happening inside a machine.” It also makes it easier for the company’s Los Angeles, California-based engineers to diagnose and remedy a problem.
6 Powerful control system
The lathes’ powerful control system can adjust each moving part’s parameters in real time and plan the CNC path to achieve geometric accuracy, surface quality, and productivity.
7 Specialized & intelligent
In addition to specially developed CAM systems, machining systems, and process monitoring, L&L offers personalized fixtures, clamping, and automatic pallet changers. Intelligent systems include self-adjusting machining control, automatic process parameter generation, simplified program design, and integrated loading/unloading.
Vision Wide’s large-size gantry machine tools can process aluminum, hard materials
Combining different capabilities on one machine improves productivity in processing diverse aerospace parts.
In 2019, a European aerospace customer contacted Vision Wide wanting to process aerospace structural parts and engine cases on one machine simultaneously. These operations involve two completely different materials and processing methods.
Most structural parts are made of aluminum alloy and require high feed rates and high acceleration/deceleration for high-speed machining, along with a high-power spindle for high removal rates.
Engine cases must be high-strength and high-heat-resistant, so they’re generally made of titanium or nickel-based alloy. To machine engine cases, it’s generally necessary to use a lathe for internal and external turning, then use a milling machine for shaping. These machines require high torque, tool and tool life management, and clamping.
Vision Wide’s R&D team responded to the request by building the GSF-TC series gantry-type, 6-axis machining center. Vision Wide’s high-power, high-speed interlocking universal head improves aluminum alloy removal, while an efficient, high-power, high-torque continuous universal head plus coolant through spindle (CTS) and 250rpm rotary table enable milling-turning of difficult-to-cut materials.

Kenneth Chen, Vision Wide’s chief technology officer, in charge of product development, works with customers to determine what they need to develop their product and how to improve production efficiency. “Never waste time with workpiece transfer operations,” Chen says. “We can integrate two machining functions into one machine to improve productivity. And, to enhance performance, we make our machines with high-speed or high-powered spindles.”
A range of capabilities

Vision Wide also has developed machines for optimized for different materials. The GSF machine is designed for cutting aluminum. The ADM series is for cutting carbon fiber and glass fiber. For difficult honeycomb material, they created the UC machine that employs ultrasonic cutting – it’s the fourth machine the company has introduced in the past three years.
In addition to improving processing efficiency, Vision Wide offers customers control of regular maintenance with reminders through the machine’s controller. Vision Wide’s professional service team in North America can provide commonly needed spare parts within 24 hours, so customers don’t have to wait for delivery from the factory in Taiwan.
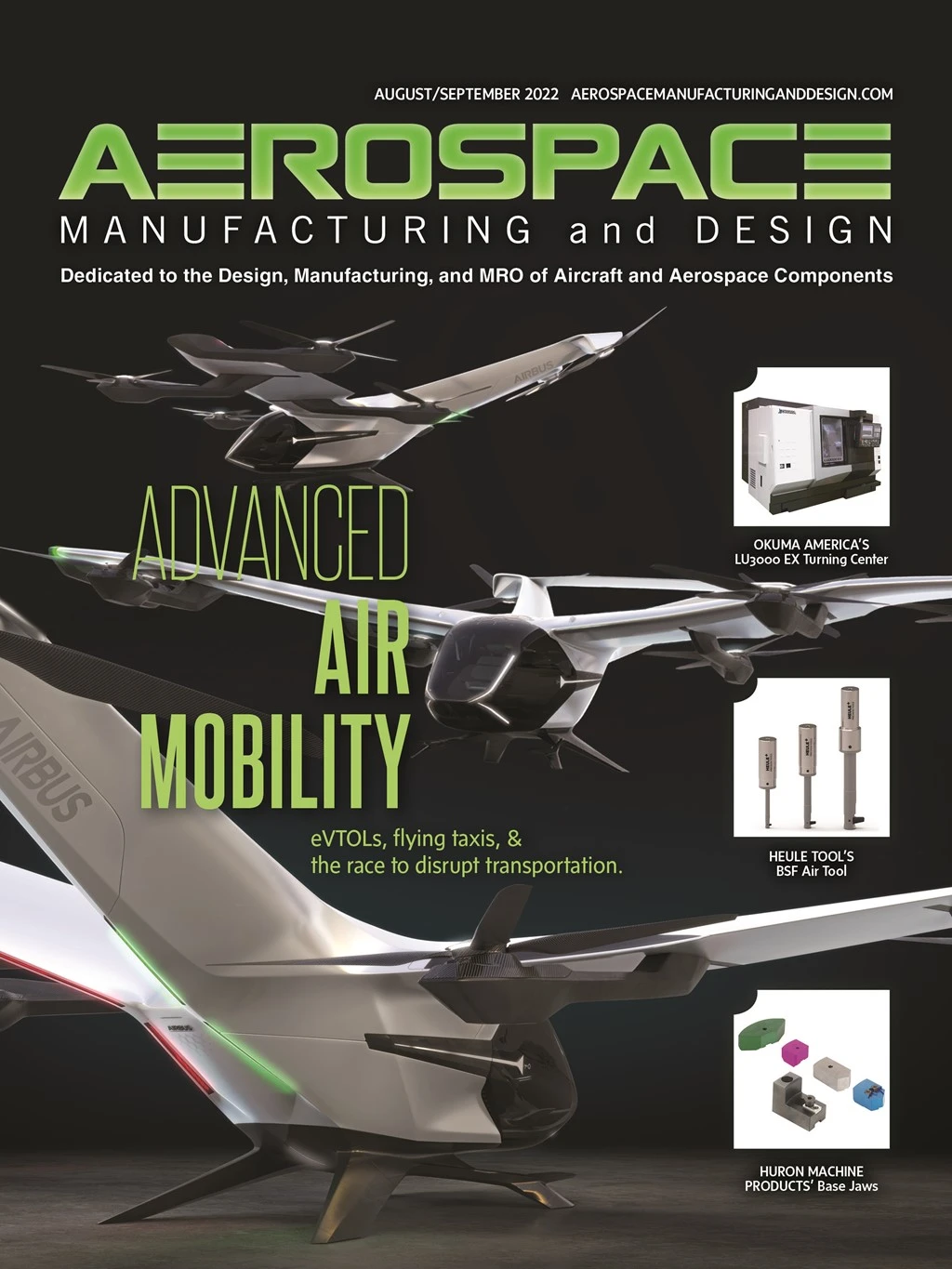
Explore the August September 2022 Issue
Check out more from this issue and find your next story to read.
Latest from Aerospace Manufacturing and Design
- AIX shows aircraft interiors are a strategic priority for global airlines
- Machine Tool Builders Roundtable: Turn equipment into expertise
- No time to waste: How to machine MedTech parts more efficiently
- The 5 Best and Fastest Spindle Repair Services
- Mill smarter, not harder: How collaboration optimizes production
- Be proactive – stay ahead of tariffs and other economic and supply chain curveballs!
- Taiwan’s China Airlines orders Boeing 777X passenger, freighter jets
- Reamer re-tipping extends life of legacy tooling