
In recent decades, airframe design and manufacturing trended toward simplifying structures and reducing part count. The reduction in part count has contributed immensely to the ease of manufacturability and overall weight savings, boosting airframe performance as well as cost savings for airframe end users. However, the concept of integral, multifunctional components has placed the burden on the structural component manufacturers and sub-assembly supply chain. When it comes to making large complex moving components for various airframes, U.S. manufacturers have found support from MAPAL when delivering simple, reliable, defect-free hinge lines through a tailor- made innovative machining approach for these types of components.
For more than 40 years, MAPAL has been a global leader in precision boring tools for all market segments. Their understanding of aerostructures enabled them to provide airframe manufacturers with robust solutions to machine hinge lines precisely, accurately, and repeatably. The U.S. team of aerospace application engineers understands the demanding requirements of airframe manufacturers and component suppliers and leverages their cutting tool knowledge to develop cutting tool solutions to best serve each manufacturer’s needs.
“We have invested in our own Aerospace Test Center and assembled a knowledgeable team who really takes the time to listen to the customer’s needs and challenge the traditional notions of the aerospace manufacturing environment,” says Mogens Nielsen, director of industry segments for MAPAL. “When it comes to the specific challenges of our aerospace customers, we offer complete cutting tool solutions to meet their preferred manufacturing method. Whether it’s done on a CNC machine or performed by skilled operators with a more manual approach such as automated drilling units (ADUs), we can tailor our approach accordingly. Some customers come to us with brand new projects, while others look to revamp their current process. To do this correctly, MAPAL works with all stakeholders, from the cutting tool end user to fixture design and machine tool builders.”
MAPAL designs and manufactures cutting tool solutions for complex moving components made from all grades of airframe materials: composite, aluminum, titanium, corrosion resistant steels, and nickel-based alloys.
“In the end, whatever material you’re cutting, however you decide to produce, and whatever tier you are within the aerospace supply chain, we assist you with process knowledge and innovative solutions, so you can deliver to your customer in a timely manner, at a competitive cost, and with zero defects,” says Alex Hjorten, aerospace segment manager for MAPAL. “Even if we play a small role in the overall aerospace supply chain by designing and manufacturing cutting tools, we are proud to help our customers by delivering a quality solution to create a safer, more efficient aircraft.”
With experience in commercial and defense fixed-wing aircraft and rotorcraft, MAPAL has begun its journey into assisting newer emerging markets such as private space companies and electric vertical takeoff and landing (eVTOL) aircraft to provide solutions across the supply chain.
MAPAL Inc.
https://mapal.com
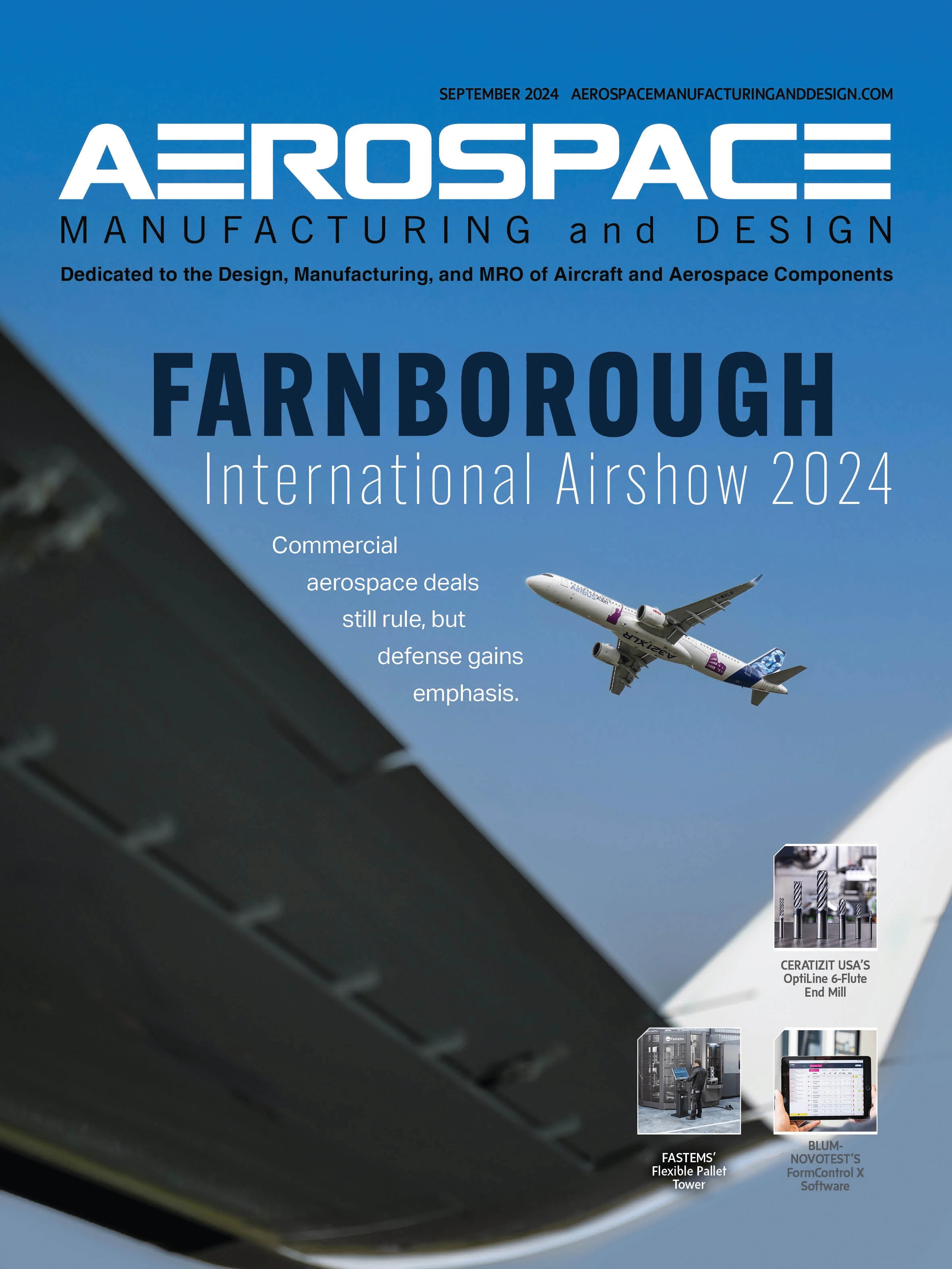
Explore the September 2024 Issue
Check out more from this issue and find your next story to read.
Latest from Aerospace Manufacturing and Design
- Piasecki acquires Kaman's KARGO UAV program
- PI Americas’ long-travel XY piezo nanopositioners-scanners
- AAMI project call submission deadline extended to May 12
- Jergens launches cast iron tooling column additions
- Airbus to acquire assets relating to its aircraft production from Spirit AeroSystems
- FANUC America's Cobot and Go web tool
- Chicago Innovation Days 2025: Shaping the future of manufacturing
- High-density DC/DC converters for mission-critical applications