Aerospace original equipment manufacturers (OEMs) and maintenance, repair, and overhaul (MRO) operators continually seek new ways to improve the performance and longevity of turbines, flight control systems, landing gear, and hydraulics. Components must withstand erosion, corrosion, extreme temperatures, high loads, and metal-on-metal contact.
Additionally, suppliers are seeking new ways to increase the operational performance and fuel efficiency of aircraft through refinements in component and system design, materials, and coatings. Minor factors, such as compressor blade surface finish, can increase the fuel economy in high-bypass-ratio turbofan engines.
This is putting renewed attention on coating, plating, or nitriding options that modify the surface of critical components to improve wear and corrosion resistance while providing the required coefficient of friction for metal-on-metal contact or erosion resistance necessary for optimum airflow in gas turbines.
This comes at an opportune time, given the industry’s transition from hard chromium plating to more environmentally friendly alternatives. Once
Thin film coatings applied by physical vapor deposition (PVD) and plasma-assisted chemical vapor deposition (PACVD) and other techniques such as nitriding are filling this void, providing greater durability than hard chrome plating while providing similar functional properties.
Thin film coatings
Approved and field-tested, PVD and PACVD can deposit thin film coatings to harden the surface of components, increasing component lifespan while reducing maintenance and downtime.
Typically 1µm to 5µm thick, and up to 25µm for specific erosion-resistant properties, coating tolerances can be as low as ±0.5µm across a surface. Thin layers, in conjunction with close tolerancing, means that the
Oerlikon Balzers’ Balinit Turbine Pro PVD coating is designed to protect engine compressor blades, vanes, or integrated bladed rotors (
“In the aircraft industry, the goal is to reduce fuel use as much as possible,” explains Oerlikon Balzers Global Aerospace Segment Manager Toby Middlemiss. “Manufacturers often polish compressor blades and
As blades foul in service, compression system efficiency eventually drops.
“Debris particles in the air erode the surface finish of the blades. They begin to get a matte finish and ultimately lose performance,” Middlemiss says. “By applying [Balinit Turbine Pro] coating, you can maintain the highly polished surface finish and retain the efficiency gain.”
Balinit Turbine Pro uses a metal aluminum nitride (
Balinit Turbine Pro hardness has been demonstrated in
In the solid particle erosion test, in which materials were evaluated based on mass loss, Balinit Turbine Pro demonstrated more than 4x higher erosion protection than titanium nitride (TiN) and other PVD coatings – more than 40x when compared to uncoated titanium.
Chrome plating alternative
Hard chrome plating has been consistently used to protect aerospace components from fretting, corrosion, and wear. However, carcinogenic hexavalent chromium salts used in hard chrome plating spurred the U.S. Occupational Safety and Health Administration (OSHA) and the EU (REACH) to impose tight restrictions on chromium and cadmium plating.
Existing chromium and cadmium plated parts will need to be replaced, and new parts will need to be manufactured using environmentally safe materials.

Some OEMs have attempted to replace hard chrome-plated steel with uncoated, hardened stainless steel, but stainless steel has poor low-frictional wear and sliding properties.
Another option, tungsten carbide-based thermal sprays, often require considerable post-coating processing and grinding, which drive up costs. On thin-walled parts, thick thermal spray coatings can also result in unwanted stresses and distortions of the components.
Balinit C, a tungsten carbide/carbon (WC/C) ductile carbide carbon of the diamond-like carbon (DLC) family (a-C:H
Balinit C coating has a high load-bearing capacity, even during dry contact or low lubrication conditions. A low friction coefficient reduces pitting and fretting corrosion on sliding or moving parts on an aircraft, such as on actuators, compressors, and pumps.

Bearings are another component that
The PVD coating can be applied to inner and outer races and cylinders and the balls in ball bearings in a uniform coating thickness of 0.5µm to 1µm. A slight increase in roughness is offset by the burnishing qualities of the coating, which smooth the raceway of the inner and outer rings, providing additional protection against scuffing and pitting.
“Given the ever-increasing performance requirements and lighter construction for the next generation of aircraft, along with the environmentally friendlier concepts for operation and maintenance, there are greater requirements on the components and tools,” Middlemiss says. “PVD and PACVD coatings are an effective means to improve operational performance, reduce operational costs, extend operating hours, and reduce maintenance intervals.”
Oerlikon Balzers
www.oerlikon.com/balzers
IMTS 2018 Booth #432275
Get curated news on YOUR industry.
Enter your email to receive our newsletters.
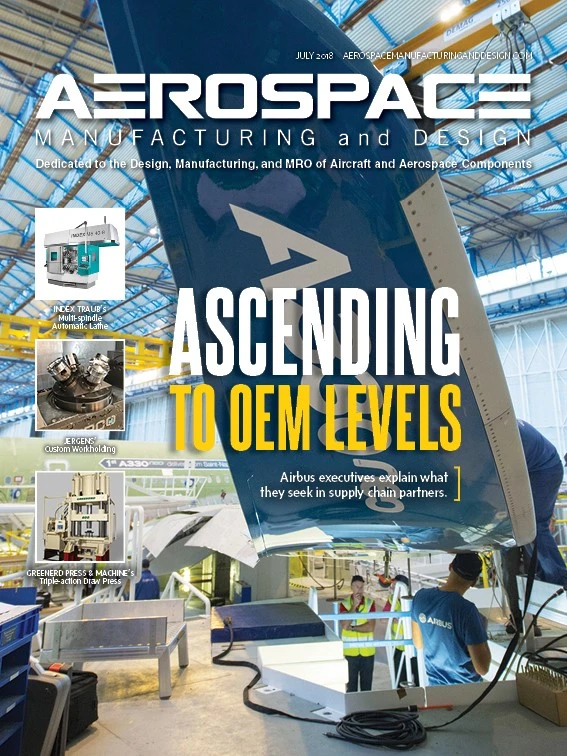
Explore the July 2018 Issue
Check out more from this issue and find your next story to read.
Latest from Aerospace Manufacturing and Design
- July is for learning – so drop in for this month’s second Manufacturing Lunch + Learn
- Essential strategies to protect your data
- NASA selects instruments for Artemis lunar terrain vehicle
- Twin-cutter boring head
- Bell awarded funding for X-plane build phase of SPRINT program
- Shaft coupling clamps
- #46 Lunch + Learn Podcast with SMW Autoblok
- Gleason Corp. acquires the Intra Group of Companies