
Machine tending is crucial for realizing complete automation in manufacturing production. Effectively incorporating machine tending to align with CNC and other automation systems serves as a strategic approach to automate processes and improve overall efficiency. While the fundamental functions of robot control, safety prioritization, and proper functioning are covered by robot brands’ programming software, extending communication beyond the immediate cell poses significant challenges. Many existing solutions lack the capabilities required for connecting with other devices, databases, or interacting with supervisory systems. Limitations in control parameters and adaptability to changing processes often hinder the full potential of machine tending integration.
Caron Engineering’s MiConnect Technology combats the challenges of integrating robot arms into operations, including CNC and automation device compatibility, limitations for complexity, and flexibility and adaptability to changing processes.
MiConnect is a customizable application builder for manufacturing, enabling the connection and control of devices in a manufacturing environment. Within the MiConnect toolbox are pre-built manufacturing devices to communicate to CNC controls, robot arms, electronic measurement devices, barcode readers, files, databases, and supervisory systems.
For machine tending integration, MiConnect serves as a software-centric solution. It facilitates the connection of a robot arm with various CNC or automation devices to interact with each other by using the drag-and-drop building blocks of operations to customize a manufacturing process. When a robot unloads a part from a machine and presents it to an electronic gage for measurement, MiConnect can signal the gage to begin measuring. Upon completion, MiConnect will signal the robot to unload the part and will send the data for automated tool wear compensation back to the CNC control.
Robots lack compatibility and device communication. Not all robot arms and automation can connect to all controls. Specific communications protocols are required per control which limits compatibility. MiConnect can create a robot as a device and a CNC as a device to pull in the registers associated with the control used within the platform for a seamless integration between robot arm and control. The user can program and control the robot arm from a single interface. MiConnect can also connect older machines with no industrial protocols.
Robots lack the ability to read databases. When a robot is tasked with loading a job into a machine, there are databases linked to that specific job, such as the part program for cutting or the CMM measuring device program for identifying the required feature measurements. The robot can’t interpret this data. If the database needs to be transmitted upstream to a production monitoring system, the robot faces challenges in connecting or communicating with such a system. MiConnect Technology simplifies this process, allowing for seamless communication and connectivity.
MiConnect streamlines user interaction by providing a singular, user-friendly interface for programming all device communication. The MiConnect human-machine interface (HMI) displays each step in the process and is customized to display user-defined steps and instructions for the operator to complete before the process advances. MiConnect ensures process integrity by systematically logging all interactions. It can retrieve necessary data from files or databases and transmit data upstream to supervisory systems, enabling comprehensive integration for total production monitoring.

Processes change. The MiConnect platform was created with flexibility and adaptability to ever-changing processes in mind. This empowers manufacturers to create a more versatile and responsive production environment. Before the introduction of MiConnect, manufacturers had to develop custom software or seek third-party applications to integrate machine tending functionalities with external systems. This adaptability is essential, particularly when robots require interaction within the broader manufacturing environment or with other interconnected systems.
By providing a solution for robots to communicate beyond their immediate environment or cell, MiConnect contributes to the efficiency and adaptability of robotic systems within manufacturing processes. It offers a more user-friendly and standardized approach to robot integration, reducing the burden on manufacturers to develop custom solutions for each combination of robot arms and control systems. By creating a standardized communication platform, MiConnect enables easy integration between robot arms and all other device communication in the process.
As industries continue to embrace automation, the role of machine tending can’t be overstated. MiConnect Technology serves as a catalyst for overcoming the challenges associated with machine tending integration, offering a comprehensive software-centric solution. By ensuring compatibility, flexibility, and a streamlined integration process, MiConnect empowers manufacturers to unlock the full potential of automated production systems, marking a significant step toward the future of manufacturing efficiency.
Caron Engineering
IMTS 2024 booth #134742
NEWS AND PRODUCTS
Plated ULTEM resin in aircraft parts

SABIC and Cybershield Inc. will begin using plated ULTEM resins in aerospace applications as part of a new collaboration. SABIC shared their expertise on injection molding of high-heat ULTEM resins while Cybershield shared their experience and capabilities to optimize plating quality and performance on a range of ULTEM resins and other specialty materials to potentially expand their use in applications requiring electromagnetic interference (EMI) shielding. Cybershield has successfully molded ULTEM 2310 resin into backshells for electrical connectors for use in audiovisual (AV) control modules for commercial aircraft for Russtech Engineering Co. Inc.
Cybershield previously worked with SABIC on the development of glass fiber-reinforced ULTEM EPR resins, which offer enhanced plating capability.
CNC manufacturing management software

MMS 8.2 software controls automation systems and helps CNC manufacturers use automation to measure, report, and optimize production sustainability efforts. Users can measure energy consumption of NC programs, minimize power usage during machine idle times, and dedicate specific machine tools to process certain metals for high-quality chip recycling. MMS version 8.2 will be available as a new feature and as an upgrade to existing automation systems beginning Summer 2024.
MMS version 8.2 helps manufacturers achieve sustainability goals, especially in high-mix manufacturing.
MMS 8.2 measures and reports the machine tool energy consumption of each NC program, allowing manufacturers to calculate the energy use in part level. The information can also be used to adjust inefficient NC programs or for running certain parts overnight when the electricity demand is lower.
To minimize unnecessary energy use, the auto-power on/off function turns machine tools off when there aren’t planned NC-programs to run. With the automatic wake function, the machine starts and warms up before the next NC-program start time.
MMS 8.2 comes with a material-dedicated feature allowing users to route jobs with specific material to specific machine tools so high-quality chips can be easily separated and recycled.
Fastems
IMTS 2024 booth #338966
NDAA compliant neodymium iron boron magnets

Neodymium iron boron (NdFeB) magnets offer energy storage and transfer, making them especially fit for a variety of mission-critical applications where high-energy materials are required. The high energy potential makes the magnets suited for use in high-performance motors, magnetic resonance imaging (MRI), sensors, and more. While NdFeB has corrosive potential, corrosion-resistant coating for the NdFeB magnets is available.
In compliance with the John S. McCain National Defense Authorization Act (NDAA) which went into effect Jan. 1, 2020, Arnold Magnetics has established a secure NdFeB supply chain with compliant rare earth permanent magnet manufacturing. This offers uninterrupted NDAA-compliant supply for aerospace and defense markets.
Robotic quality inspection

PRESTO System is a modular suite of automated robotic inspection cells for 3D measurement in aerospace manufacturing. PRESTO System builds on the foundation of the turnkey PRESTO quality inspection cell to provide manufacturers a future-proof system that’s scalable, versatile, and seamlessly integrated.
PRESTO System allows manufacturers to be more agile with automated robotic programming enabling a single quality control specialist to create, test, and deploy robust robotic inspection in hours. The integrated robotic system eliminates repetitive manual setup and calibration processes, enabling teams to work more effectively and focus on operations.
PRESTO System is agnostic so manufacturers can integrate it with existing metrology and quality assurance software, acquiring datasets to optimize quality and inform continuous process improvement. Users can develop feedback loops by identifying key trends, predicting more accurate out-of-tolerance (OOT) results, or addressing the root cause of non-conformances in a Quality Management System (QMS).
PRESTO System comprises three base models: near-square 4.5m PRESTO M uses one fixed laser tracker and 3D laser scanner; 10.0m x 5.5m PRESTO L with a mobile tracker and mobile scanner; and 10.0m x 7.5m PRESTO XL that employs two mobile trackers and two mobile scanners. Multiple options are offered to adjust inspection performance. Metrology professionals can use their preferred metrology software to work with programs and data. The metrology data produced by deployments of the PRESTO System can be easily analyzed and shared with other desktop software and cloud applications through Hexagon’s open digital reality platform, Nexus.
Hexagon
IMTS 2024 booth #134102; #133210
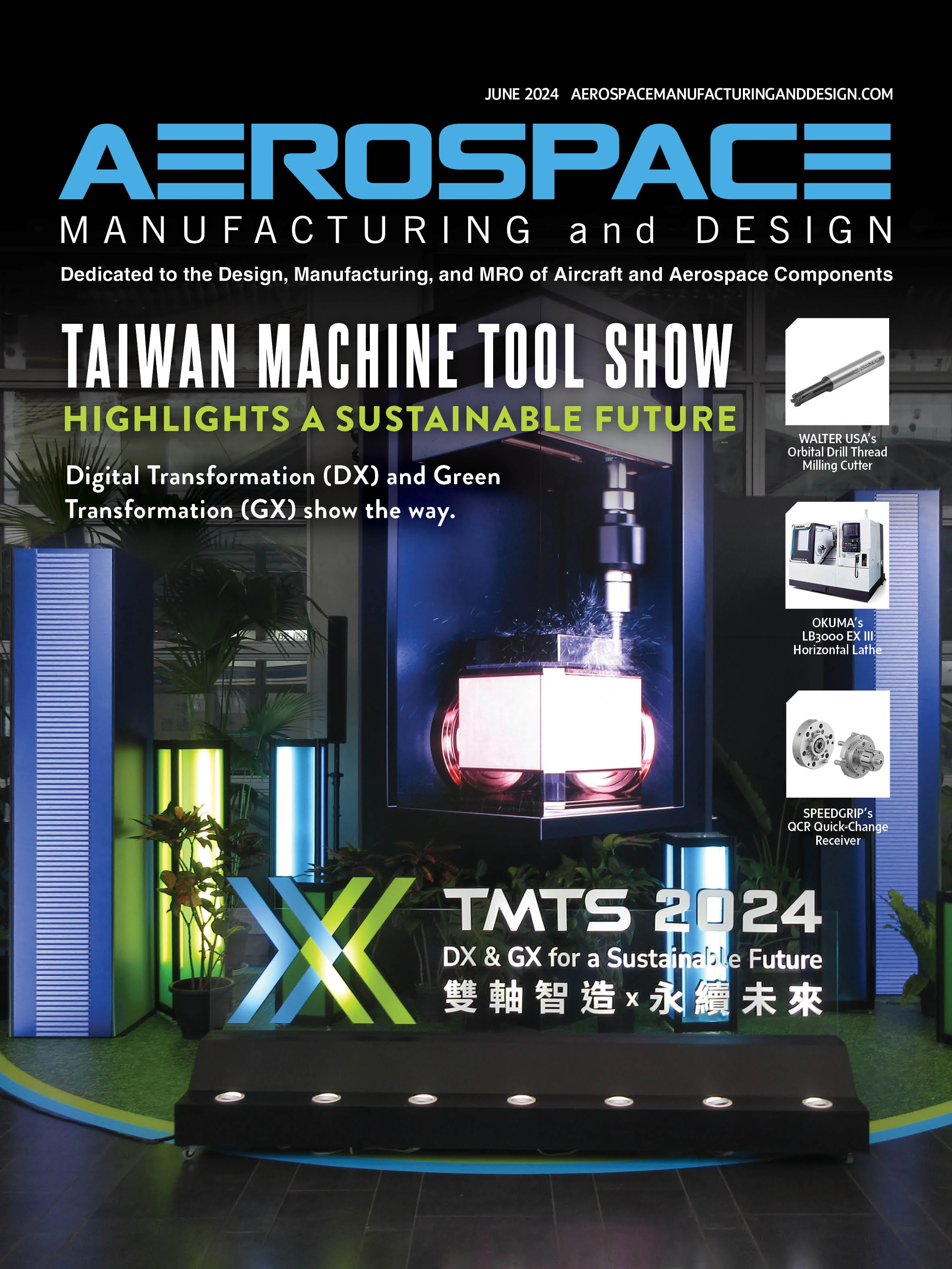
Explore the June 2024 Issue
Check out more from this issue and find your next story to read.
Latest from Aerospace Manufacturing and Design
- AAMI project call submission deadline extended to May 12
- Jergens launches cast iron tooling column additions
- Airbus to acquire assets relating to its aircraft production from Spirit AeroSystems
- FANUC America's Cobot and Go web tool
- Chicago Innovation Days 2025: Shaping the future of manufacturing
- High-density DC/DC converters for mission-critical applications
- #59 - Manufacturing Matters: Additive manufacturing trends, innovations
- ACE at 150: A legacy of innovation and industry leadership