
A team of scientists at the U.S. Department of Energy’s (DOE) Argonne National Laboratory is combining one-of-a-kind X-ray experiments with novel computer simulations to help engineers at aerospace and defense companies save time and money.
The process starts at Argonne’s Advanced Photon Source (APS), which produces X-rays more than a million times brighter than those in a dentist’s office, allowing engineers Brandon Sforzo, Alan Kastengren, and Chris Powell to peer through an engine’s steel fuel injector.
“Visualizing through steel with this detail is not possible with any other diagnostic technique,” says Prithwish Kundu, an Argonne aerospace engineer who develops predictive computer models derived from experiments at the APS.
Sforzo adds, “If you don’t have the brightness of the light we have here, you can’t see what’s going on inside these devices.”
In 2019, Sforzo and his colleagues investigated the fluid dynamics within a gas turbine and noticed odd behavior. “We could see the liquid spray ending up in unexpected places.”
These revelations help scientists understand the fundamental physics that affect engine performance, thrust, and emissions. The data – boundary conditions – enable high-fidelity simulations.
Boundary conditions are detailed parameters that act as guardrails; with the right boundary conditions, scientists can build models that predict a host of engine behavior involving pressure, temperatures, mass, and speed that may be unmeasurable during experiments.
“With the right predictive models, we can reduce testing and development costs by a large margin,” Kundu says.
While engineering thrives on high-fidelity 3D models, those models often run for months on supercomputers – a scarce resource for most businesses.
To solve this challenge, Kundu, along with Opeoluwa Owoyele and Pinaki Pal, are exploring a type of artificial intelligence (AI) known as deep neural networks, which help computers find patterns within large, complex data sets. They have already developed neural-network algorithms that significantly reduce the time to optimize models; the equations also help the scientists understand combustion engines’ chaotic inner workings.
“There are so many parameters in an engine – the human mind can’t analyze a 10-dimensional space,” Kundu says.
Using Argonne’s Blues and Bebop high-performance computers, Kundu and Sibendu Som, manager of the laboratory’s Multi-Physics Computation group, created a high-fidelity model that measures how two different jet fuels behave in a gas turbine engine combustor.
They discovered the computational models could predict trends in lean blowout, a condition in which a gas turbine engine’s flame sputters in response to less fuel.
In another study, Pal, in collaboration with the Air Force Research Laboratory, developed high-fidelity simulations for Rotational Detonation Engines (RDEs). These tools will help engineers accelerate the design of RDEs, which might enable future supersonic and hypersonic flight.
Get curated news on YOUR industry.
Enter your email to receive our newsletters.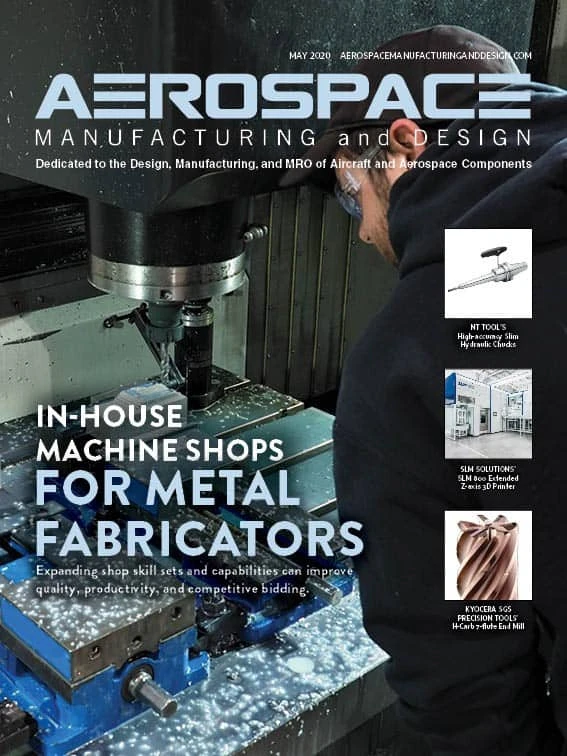
Explore the May 2020 Issue
Check out more from this issue and find your next story to read.
Latest from Aerospace Manufacturing and Design
- Ralliant to establish global headquarters in North Carolina
- Philatron MIL-DTL-3432 military cables
- Beyond Aero refines its hydrogen-electric light jet
- Americase's advanced protective solutions
- Social media - what are your thoughts
- GE Aerospace secures Air Force engine contract
- Thomson Industries' online sizing and selection tool
- #53 - Manufacturing Matters - 2024 Leaders in Manufacturing Roundtable