
1. What obstacles have you witnessed preventing manufacturers from achieving higher productivity?
Since 2020 we’ve seen numerous manufacturers struggle with material shortages that caused uncertainty for planning and meeting customer demands. There are still some occurrences of material supply issues, but more prevalent now are struggles with finding and retaining talented people. It’s become apparent there’s a knowledge gap within manufacturing due to the retirements or loss of machinists, technicians, and engineers. This creates a struggle for companies to innovate and improve processes at the same rate they did 5 to 10 years ago. Manufacturers need to do more with less but can’t work on projects to improve productivity and still meet customer demand. This is where we can help, by offering our machining expertise to optimize their processes… creating a win-win!
2. How can Greenleaf help manufacturers?
In addition to the tooling solutions Greenleaf offers, the company has a long tradition of hiring and developing technical individuals to assist our customers. From the technical sales engineer, working directly onsite with the customer, to the customer service and engineering teams supporting from the corporate office, each group is staffed with personnel focused on delivering designs, shop floor advice, and best-practice information. Due to staffing shortages within the manufacturing engineering departments at many companies, our direct support can provide much needed assistance and help develop new team members with hands-on training and demonstrations. Decades of experience with aerospace applications from the Greenleaf team can reduce the learning curve and rapidly improve manufacturers’ levels of productivity.
3. What productivity solutions does Greenleaf offer for manufacturing aerospace components?
Greenleaf revolutionized manufacturing heat-resistant super alloys in the 1980s with the introduction of WG-300, a whisker-reinforced ceramic grade. This provided manufacturers with productivity gains up to 10x higher than traditional carbide tooling. Greenleaf has continued to innovate since with additional ceramic grades to meet the demands of the constantly changing and more difficult-to-machine materials used in aerospace. Another area where Greenleaf has proven success is with special engineered products. Whether it’s turning, milling, grooving, or slotting, Greenleaf works with the customer to develop a unique solution offering productivity gains along with quality, dependability, and repeatability.
4. Does Greenleaf have other products to help boost productivity beyond specially designed solutions and ceramic grades?
Greenleaf offers standard ISO tooling systems to support indexable carbide products that provide customers with additional options for applications in titanium alloys and finishing heat-resistant super alloy (HRSA) materials. The company pushes for developing improved carbide grades. G-9610, for example, offers significantly higher speeds for finishing titanium versus other commercially available grades on the market. We focus on developing solutions for materials and applications providing customers with sustainable productivity. Greenleaf is constantly working to be our customers’ one-stop-shop for their tooling and insert needs, technical service and support, and long-term partner. Greenleaf is excited about the opportunities for growth as we look toward the future.

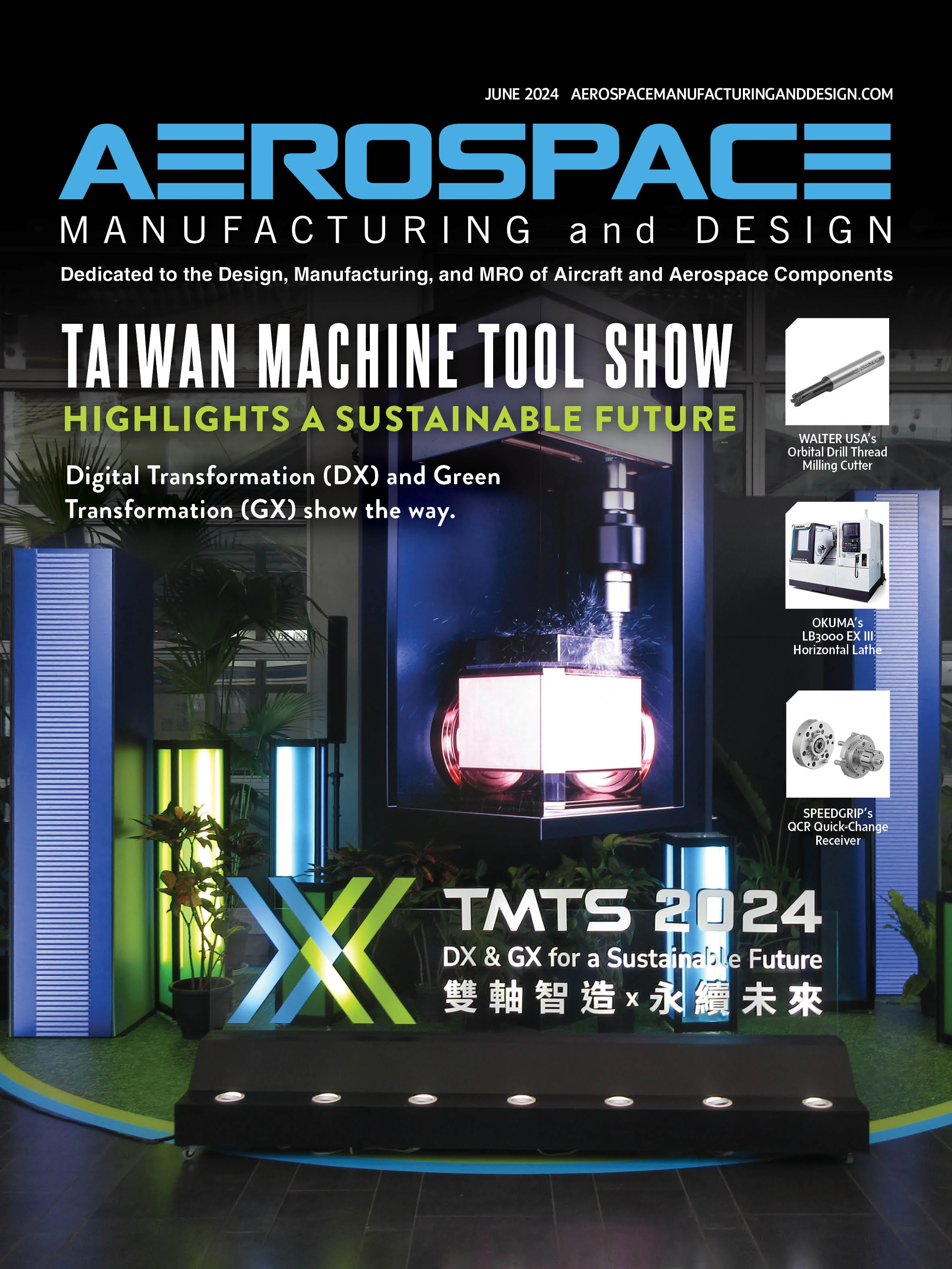
Explore the June 2024 Issue
Check out more from this issue and find your next story to read.
Latest from Aerospace Manufacturing and Design
- Talking machine tools with the professionals who build them
- Tools and strategies for improving your machining processes
- America Makes announces QTIME project call
- Innovation meets precision for 40% faster machining
- Upcoming webinar: Pro tips from a supply chain strategist
- Heart Aerospace relocates to Los Angeles
- Fixtureworks introduces Stablelock Clamps
- Piasecki acquires Kaman's KARGO UAV program