
More than 120 experts in the aviation industry from Europe, North America, and Asia attended the recent Starrag Group Aero Structures Technology Days 2016 at the factory in Mönchengladbach, Germany. Highlighting the theme of high-precision production of titanium and aluminium aircraft structural components was a demonstration of the 100th Ecospeed 5-axis machining center.
The model F 1540 with 120kW spindle and 1,500mm x 4,000mm pallet size is designed for medium-sized structural components such as wing ribs and fuselage sections.
All of the machining centers of this series feature a Sprint Z3 tripod drive kinematic machining head. This type of head was developed in 1999, and all machines sold with it since then are still in use and have completed more than 4 million operating hours, according to Dr. Norbert Hennes, head of the new aerospace and energy business unit.
Specialists from the Starrag Group and its technology partners – Ceratizit, CGTech, GMN, Haimer, Ingersoll, Iscar, Kennametal, Sandvik, Siemens, and Walter – provided experts from Belgium, China, Germany, France, Britain, Korea, North America, Russia, and the Czech Republic with information about the manufacture of these components.
Sixteen of the 100 Ecospeed machining centers sold so far are in use at Premium Aerotec, a European Tier 1 supplier with around 9,000 employees and a turnover of approximately $2.1 billion. The machining centers are used to produce large aircraft structures from aluminium, titanium, and carbon fiber composite materials (CFRP). www.starrag.com, IMTS 2016 Booth #S-8696
Trumpf Laser Technology Center celebrates 20th anniversary

In June, the Trumpf Laser Technology Center in Plymouth Township, Michigan, celebrated its 20th anniversary. The event was held in conjunction with the annual open house and Advanced Laser Applications Workshop (ALAW). Nearly 200 people gathered in the remodeled customer showroom for the keynote given by Dr. Cornelius Schinzel, director of international sales. His speech chronicled many of the highlights over the past 20 years and included a note from Klaus Loeffler, managing director, sales and service, of the laser technology for the Trumpf Group who helped to establish the Michigan facility and served as its first managing director.
Trumpf’s Laser Technology Center has matured from a small facility with a handful of employees to a sales, service, and spare parts location for lasers and multi-axis systems supported by a staff of more than 100. These employees support the needs of more than 1,500 customers – a number which continues to rise as the latest laser technologies enable new opportunities and applications. The Laser Technology Center contributes to Trumpf’s 11,000 employee, $3 billion global business.
Dr. Schinzel’s address was followed by a champagne toast led by Dr. Christof Lehner, the current general manager of Trumpf Laser Technology Center. Attendees were then free to explore Trumpf’s latest laser technologies for cutting, welding, marking, and surface treatment. www.us.trumpf.com, IMTS 2016 Booth #N-6223
Finmeccanica changes company name
Multinational aerospace, defence, and security company Finmeccanica, headquartered in Rome, Italy, is changing its name. The company’s name will be Leonardo-Finmeccanica S.p.a. until Dec. 31, 2016, and Leonardo S.p.a. effective from Jan. 1, 2017.

The new name is inspired by Leonardo da Vinci, recognized as a symbol of creativity and innovation – as well as a visionary of helicopters, a globally recognized product of the company with more than 47,000 employees worldwide. As of Jan. 1, 2016, the Helicopter Division has absorbed the activities of AgustaWestland.
The company has also rebranded its Finmeccanica Global Services to Leonardo Global Solutions, which manages more than 12,000 suppliers and procures services for the company worth $1.3 billion annually. The board of directors also approved incorporation of the firm’s wholly-owned subsidiary Sirio Panel S.p.A. into Leonardo-Finmeccanica. www.leonardocompany.com
Element grows following Cascade TEK rebrand
After completing the formal rebranding of newly acquired Cascade TEK laboratories, Element Materials Technology is expanding its aerospace product qualification testing (PQT) footprint into the U.S. West Coast aerospace markets.
The former Cascade TEK laboratories will now be known as Element Portland (Oregon) and Element Denver (Colorado). The integration of these two locations to Element’s global platform extends the company’s technical capabilities, particularly in RTCA/DO 160 and MIL-STD 810 environmental testing services. Element Portland and Element Denver will work closely with Element’s existing Seattle, Washington, laboratory to service clients within these local markets.
Element Portland and Element Denver already hold test approvals with many aerospace primes and their supply chain partners, including Boeing, Honeywell, and Rockwell Collins.
Element now has a total of 15 laboratories dedicated to the provision of PQT services. www.element.com
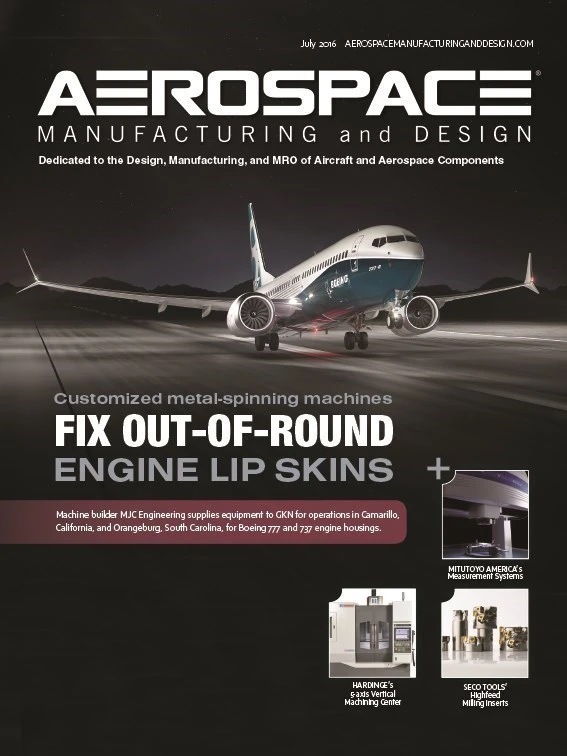
Explore the July 2016 Issue
Check out more from this issue and find your next story to read.
Latest from Aerospace Manufacturing and Design
- Season's greetings
- 2024 Favorites: #7 Article – Deep drawing aerospace components
- 2024 Favorites: #7 News – GKN Aerospace completes sale of St. Louis facility to Boeing
- 2024 Favorites: #8 Article – Beyond uptime
- 2024 Favorites: #8 News – NASA, Lockheed Martin reveal X-59
- 2024 Favorites: #9 Article – 5 tips for upskilling your aerospace machinists
- 2024 Favorites: #9 News – Siemens acquires Altair Engineering
- 2024 Favorites: #10 Article – How 3D-printed aviation parts can accelerate return to air