
Earlier in this series, we explored the history and uses of titanium, as well as some ways to achieve satisfactory tool life while machining it. Yet even the best cutting tools and toolpaths will fail without a robust way to hold those tools, grip the workpiece securely, and support toolpaths with a solid and accurate machine tool. Being successful with titanium requires all this and more; for example, predictable process control is as important as what equipment and tooling is used.
In this final installment, we’ll put together the other pieces to this challenging material puzzle.
Ways and means
Let’s start with the machine tool. In an ideal world, CNC lathes and machining centers wouldn’t deflect when subjected to tool pressure. There would be no expansion or contraction of the machine base when the temperature of the shop changes, and heat from cutting processes would have no effect on the spindle and machine guideways. Shops could buy a one-size-fits-all machine tool that performs equally when cutting aluminum as it does with steel, iron, and superalloys. Sadly, that’s a fantasy. As a rule, high-end equipment performs better under a wider range of cutting conditions than do commodity machines. Boxways and geared headstocks are generally more effective in heavy cuts, while linear ways and direct-drive spindles work best for non-ferrous alloys such as aluminum and magnesium, and for high-speed contouring work in mold cavities and medical components.
Titanium weights roughly 50% more than aluminum but is twice as strong. Despite its superior qualities, however, titanium is expensive to manufacture and machine, so is used primarily for critical airframe structures, engine components, and other parts where high strength and low weight is needed. Both metals are a favorite for aerospace components, many of which require large amounts of material removal, making machining efficiency paramount. Unfortunately, the similarities between the two end there.
Machine tools must be very rigid to withstand the extreme cutting forces encountered when machining titanium. Cutting speeds are generally low and feed rates relatively high. This calls for large amounts of spindle torque and axial thrust, and since abrupt tool movements and dwelling in the corners is a big no-no with titanium, responsiveness in the drive system is likewise a must. Also, a suitably sized HSK or similar spindle interface with dual face/taper contact is better able to handle heavy loads than one designed for CAT and BT-flange tooling.
Whether your machine is a spring chicken or an old geezer, regular tune-ups are a must. Spindle drawbar force should be measured frequently and adjusted as necessary, eliminating many problems with chatter and tool chipping. Regular ballbar or laser measurement to minimize axial backlash and runout is a good idea no matter what materials your shop machines. It is also important to keep it clean to assure proper guideway lubrication and prevent cutting fluid contamination.
Predictable process
“Oh great,” you’re thinking. So much for using that old machining center for the titanium job you just quoted. Well, maybe so, but even ho-hum machine tools can be used to cut titanium. The trick is development of a predictable process. Eliminate variables by closely monitoring wear on cutters, drills, and inserts, and replacing them at regular, predetermined intervals long before dull tools negatively impact part quality or breakage occurs. And always use the best cutting tools possible. Perform cutting tests with your top vendors, document the results, and once the winner has been determined, continue to use that brand and style of tool for the duration of your project.

For workholding, unpredictable part movement can be avoided by pre-machining workpiece blanks to make locating surfaces square and burr free. Ditching the traditional 6" hand-tightened machinist’s vise in favor of hydraulic or even pneumatic workholding is an excellent way to eliminate process variables and reduce operator fatigue. If mechanical clamping must be used, always employ a torque wrench so the same amount of force is applied from part to part. Many shops achieve gripping success with dovetail-style vises or serrated jaws that bite into the workpiece, especially on 5-axis machining centers, where relatively small amounts of material along the bottom of the blank are used to secure parts.
Toolholders are another make-or-break aspect of titanium machining. Horror stories of end mill pullout while roughing expensive billets of titanium are enough to keep veteran machinists and shop owners awake at night. Well-maintained hydraulic toolholders are one solution, as is shrink-fit tooling, but toolholders with dedicated anti-pullout devices are the best bet with heavy cutting, as these feature a positive mechanical stop that eliminates tool movement under side loads.
Look for cutter bodies with reinforced insert pockets and secure clamping mechanisms. These prevent the micro-shifting that often leads to chipped or broken tools and unpredictable processes. Integral shank tooling, though slightly more expensive, will provide better results than two-piece tooling solutions. Quick-change toolholders are a great way to save time, especially on CNC lathes, where tool changeover times are typically longer. Note that these should use a dual-contact design and plenty of locating surface area for maximum rigidity.
Plan for success
The right cutting tools and toolholders, robust workholding, rigid machine tools, and righteous toolpaths – these are all important success factors when machining titanium. Just as important, though, is having a good machining strategy. For those job shops with general-purpose tooling and equipment, don’t despair. The lighter cuts necessitated by less than optimal conditions can still get you to the finish line, provided a stable process is developed first.
It might be a pain in the neck, but good documentation is key to spotting trouble in advance. Keep track of what feeds and speeds were used, when they were changed and why, which cutting tools work and which ones don’t, and do a root-cause analysis of failures and near misses.
And remember, even though a stable, predictable process is important with titanium, continuous improvement shouldn’t be discounted. With the aerospace industry’s increased emphasis on lightweighting and fuel-efficiency, titanium’s not going away anytime soon. This means cutting tool and tooling manufacturers will continue their endless search for a better mousetrap to tame both this and other tough materials. Availing oneself of these technologies can make the difference between a winner job and one you’d just as soon forget. Happy cutting.
Sandvik Coromant
IMTS 2016 Booth #W-1500
About the author: Michael Standridge is an aerospace industry specialist with Sandvik Coromant and can be reached at 800.Sandvik or us.coromant@sandvik.com.
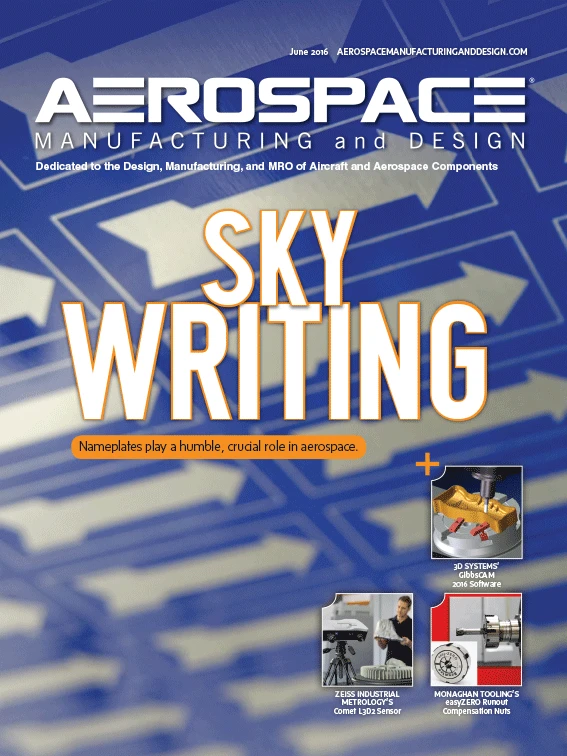
Explore the June 2016 Issue
Check out more from this issue and find your next story to read.
Latest from Aerospace Manufacturing and Design
- Revolutionizing aircraft design without sacrificing sustainability
- GE Aerospace awarded subcontract for FLRAA next phase
- KYOCERA Precision Tools publishes 2025-2026 Indexable Cutting Tools Catalog
- BOC Aviation orders 120 Airbus, Boeing jetliners
- Mazak’s INTEGREX j-Series NEO
- Embraer tests wing for new technologies demonstrator
- Mitutoyo America’s SJ-220 portable surface roughness tester
- #55 - Manufacturing Matters - A Primer on Defense Contract Manufacturing