
Interest in metal additive manufacturing (AM) has grown throughout the past five years, however many challenges prevent wider adoption. Thankfully, manufacturers can overcome these challenges by following several steps.
Standards
AM lacks accepted standards that ensure machines will offer consistent quality and meet product requirements. AM companies have started to develop standards, but we are a long way from the defined standards that casting or injection molding producers have used for years. The ASTM AM Center of Excellence has brought together universities and other research entities to collaborate on limits/standards for AM product quality.
Speed
AM is only faster than traditional manufacturing when part geometry limits the ability to make the part any other way or when designers use AM to combine multiple parts. If a part can be CNC-machined easily, it’s likely going to take longer to print in metal. Adding multiple lasers to a system could speed production by printing faster. Spee3D’s cold spray system, for example, creates near-net shapes in minutes rather than hours but requires post machining. Another option is ExOne’s binder jet process which prints large lots of parts quickly, but requires a secondary sintering operation which causes the parts to shrink, forcing users to predict the shrinkage.
Size
Older metal laser sintering systems had 10" x 10" x 10" build volumes for many years, but newer printers have volumes up to 31.5" x 15.75" x 19.7". This is still not enough to build large parts for heavy machining or tool and die. Wire feedstock printing supports larger volumes using arc, electron beam, or laser, but the resulting poor surface finish often requires post machining. Often faster than traditional forging, it still can take weeks or even months to build a 1,000 lb product.

Cost
Machines can cost $750,000 to $4 million. New technologies, such as the Desktop Metal or Markforged extrusion base processes, bring the costs to less than $200,000. However, these don’t typically build solid parts, filling interiors with a lattice instead. And these processes require secondary sintering which causes shrinkage. Xact Metal is now offering a $150,000 laser sintering machine with a 5" x 5" x 5" build size.
Powders
Powders, the primary feedstock of most metal AM technologies, have a lot of variation among materials. For metal printing, spherical powder is typically best, but some powders have more porosity or varying compositions. The better the powder quality, the higher the cost. Many companies are trying to figure out efficient ways to print with low-cost powder. Another challenge is that most machine vendors provide a universal printing parameter which may not be optimum for the part geometry or specific powder composition. Companies often cannot perform design of experiments to tailor parameters for specific parts to optimize output.

In-process monitoring
Manufacturers are adding cameras or pyrometers to review image data and determine if a part is built correctly. If a part takes two weeks to build, it is better to find out early if something went wrong in the first few layers than after the build. Detecting failure in real-time and modifying parameters on subsequent layers is another option. This fix, however, requires very fast data processing to crunch data and apply corrections.
Automated process
Downtime and delays can occur when an operator isn’t present to switch a build to the next step when it finishes in the middle of the night. Automation can complete tasks such as taking the build from the machine to a de-powdering station, then on to stress relief/heat treat, plate & support removal, and post-finishing, reducing downtime between process steps.
Software tools
AM software has been cumbersome in the past. Improved programming and setup tools are being developed to simulate the build and provide predictions on optimized support structures or to detect potential failure points. Topology optimization tools use a mathematical model to optimize the material placement, ensuring the best properties for applied loads with minimal material. These tools enable organic structures that are perfect for AM, reducing weight and overall part cost.
Training, education
There is a huge shortage of trained AM operators because college and vocational programs are not being developed fast enough, forcing companies to invest in in-house training.
Despite many challenges, metal AM is making its mark. Every industry should be considering AM, because in many cases adoption can revolutionize products and set a company apart from its competitors.
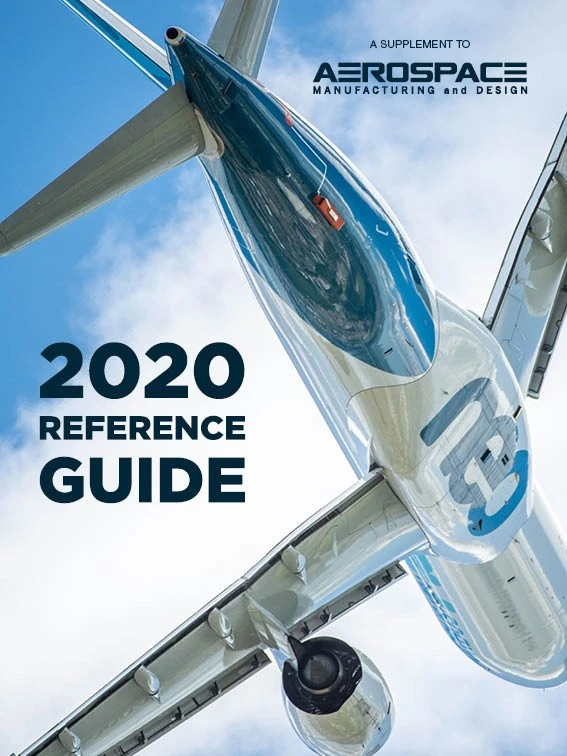
Explore the AMD Reference Guide 2020 Issue
Check out more from this issue and find your next story to read.
Latest from Aerospace Manufacturing and Design
- GE Aerospace secures Air Force engine contract
- Thomson Industries' online sizing and selection tool
- #53 - Manufacturing Matters - 2024 Leaders in Manufacturing Roundtable
- Join us for insights on one of the hottest topics in manufacturing!
- You can still register for March’s Manufacturing Lunch + Learn!
- Ohio creates Youngstown Innovation Hub for Aerospace and Defense
- Tormach’s Chip Conveyor Kit for the 1500MX CNC Mill
- How to Reduce First Article Inspection Creation Time by 70% to 90% with DISCUS Software