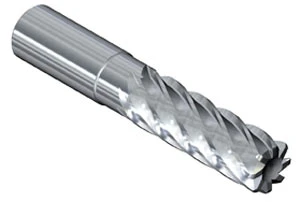
The increase in titanium aircraft components, and the need to quickly optimize the process for machining them, has recently led some leading manufacturers to seek a single-source supplier for capital equipment, specialized cutting tools, and applications engineering programming expertise including CATIA V5 programming services.
Responding to this trend, the Productivity Solutions business of MAG Maintenance Technologies has teamed up with sister company MAG Cincinnati to supply a comprehensive solution from a single source.
MAG Maintenance Technologies specializes in providing proprietary tooling for the optimized cutting of titanium and other materials in combination with part programming expertise. Metal removal rate and tool life improvements range from 5x to 30x higher than traditional methods, while applications programming further improves overall manufacturing efficiency.
MAG Cincinnati has introduced and installed a wide range of new products. A specially configured 5-axis, multiple-spindle profiler, named the Ti Profiler, has emerged as a titanium processing champion. MEGA Series 4- and 5-axis horizontal machining centers, U5 Universal 5-axis/5-sided universal machining centers, and special build machines round out the MAG Cincinnati roster of machine tools for titanium processing.
Meeting the demand for titanium parts production has been both a challenge and an opportunity. Key suppliers to aircraft programs such as the Boeing 787, Airbus A380, and the latest-generation military aircraft including the Joint Strike Fighter and the Eurofighter, have required huge gains in cubic-inch-per-minute metal removal rates from tooling to supplement their ramped-up acquisition of machine spindles capable of machining titanium.

MAG Cincinnati H5 800 5-Axis Horizontal Machining Center provides excellent high-torque titanium cutting performance, at lower speeds, with the versatility of the 180° rotating A-axis. The machine features 100 BAR through-tool coolant supply.
MAG Maintenance Technologies is helping manufacturers meet the challenge with a series of cutting tool solutions that balance feedrate improvements, surface finish results, tool life and tool cost. The brazed-carbide Raptor, for instance, provides up to a 30x productivity bonus, with tool life doubled. One of the newest offerings of specialized tooling, the Lightning cutter, is a solid carbide, uncoated tool with a uniform flute divide. Additionally, MAG's Mega-Flute is being employed when the very fastest cutting speeds, up to 2,000mm/min (79ipm), are required.
Other products from the Productivity Solutions Group include a tool management system, adaptive control and monitoring software, and software modules for optimizing milling feedrates and tool life. Specialized teams within the group are also focused on supporting the machining operations of heavy truck manufacturers and the oil exploration industries. mag-ias.com

Explore the May June 2008 Issue
Check out more from this issue and find your next story to read.
Latest from Aerospace Manufacturing and Design
- 2024 Favorites: #5 Article – Solving workforce issues with digital transformation
- 2024 Favorites: #5 News – GE Aerospace is investing in manufacturing
- 2024 Favorites: #6 Article – Mastering complex precision machined parts
- 2024 Favorites: #6 News – Boeing to acquire Spirit AeroSystems in $8.3B deal
- Season's greetings
- 2024 Favorites: #7 Article – Deep drawing aerospace components
- 2024 Favorites: #7 News – GKN Aerospace completes sale of St. Louis facility to Boeing
- 2024 Favorites: #8 Article – Beyond uptime