
GIE Media
Use of solid carbide end mills is on the rise. However, special consideration is essential when machining HRSA and titanium alloys characterized by poor thermal conductivity and strength and hardness at high temperatures.
1. Trochoidal machining techniques are becoming more widespread with CAM providers supplying their own methods.
Be light and fast by using a radial engagement less than 20% of the tool diameter. By using large AP and low AE, along with a controlled maximum chip thickness, the cutting forces are controlled and provide a smooth cut. Low AE engagement improves stability and allows for higher feed rates, ultimately improving productivity and tool life. Solid carbide end mills perfectly support this technique.
2. Optimized grades and geometries play a vital role in improving machinability.
Sandvik Coromant end mills meet material machinability demands. For nickel alloys, CoroMill® Plura solid carbide end mill grade GC1710 delivers a sharp, controlled edge-line with a hard, wear-resistant, fine-grained substrate. The grade resists high working load when machining hard, highly adhesive, work-hardened materials such as aged Inconel 718. The end mills for titanium are available in GC1745 grade, developed with a new coating technology providing excellent wear resistance and low thermal conductivity. The grade is based on a tough, sub-micron, cemented-carbide substrate with sharp, controlled edges for demanding aerospace milling operations. These tools are unevenly pitched to avoid chatter while reaching higher speeds for increased productivity and process security.

3. Where reaches up to 10xD are required, look to a modular system such as the Coromant EH solution.
This system offers the required reach and accessibility with a variety of shanks and adapters. Couple the Coromant EH system with the versatile CoroMill® 316, the exchangeable-head milling system tailored to your unique applications and materials.
4. Machining components with slots and pockets is a challenge.
Apply a plunge milling strategy to make manufacturing small, deep slots and pockets more time-efficient and cost-efficient. The unique CoroMill® Plura Gannet solid carbide end mill is designed exclusively for plunge milling and is ideal when tool diameter is limited and a long overhang is required. The CoroMill® Plura Gannet is a secure, productive solution for roughing blisks and impellers using its optimized grade and geometry for HRSA materials.

5. Though frequently overlooked, tool holding is extremely important to the performance of solid carbide tools and security of your application.
For a versatile solution, try hydraulic chucks such as the CoroChuck® 930. With the best pull-out security on the market, CoroChuck® 930 eliminates vibration for excellent stability and accessibility. These tools can quickly and easily be tightened and released without needing external equipment, such as induction heating units. These tools also offer tolerances of a few microns to improve surface finish, precision, and quality.
Author William Durow is Sandvik Coromant’s Global Engineering Project Office Manager - Aerospace, Space, and Defense
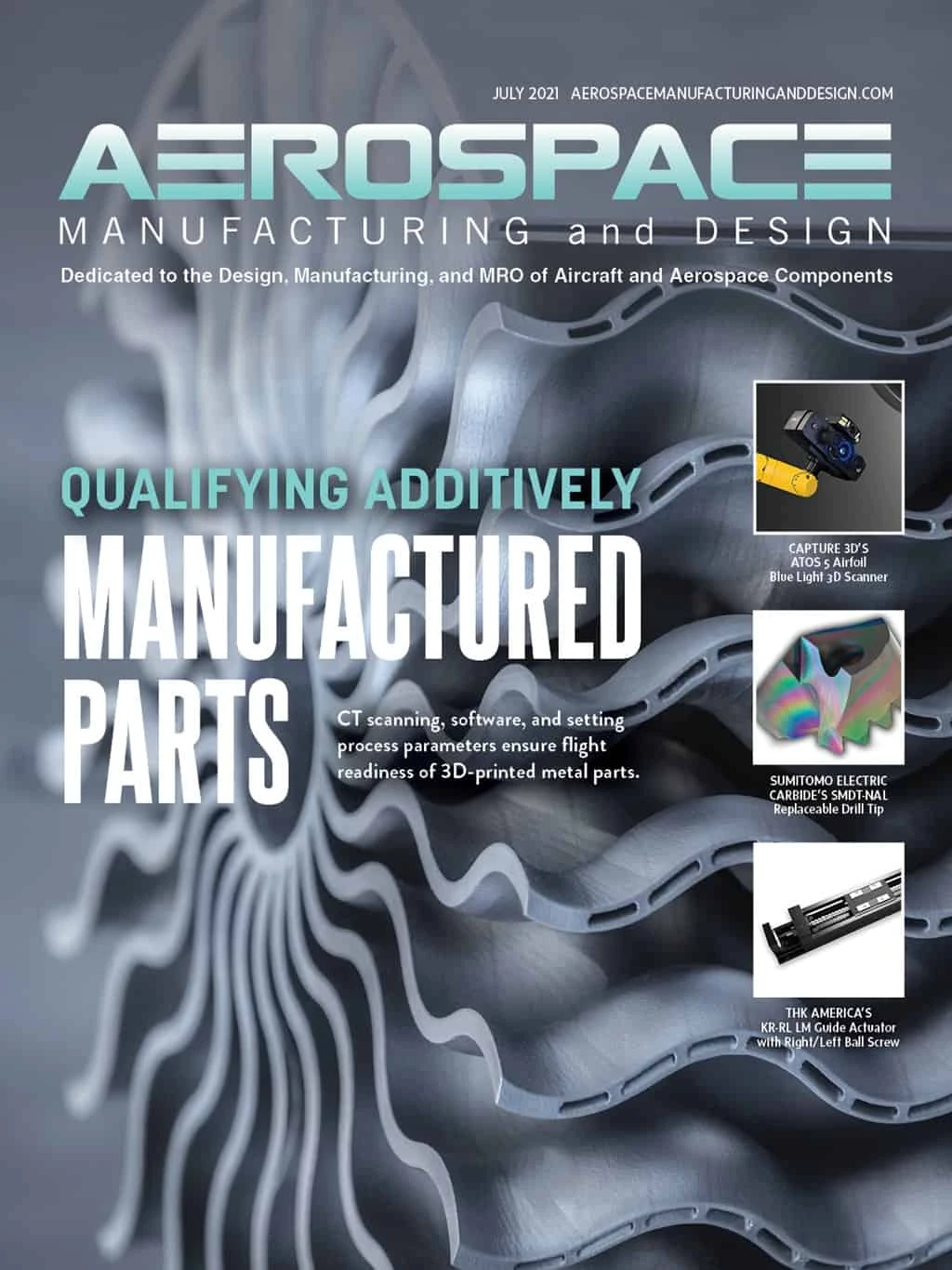
Explore the July 2021 Issue
Check out more from this issue and find your next story to read.
Latest from Aerospace Manufacturing and Design
- Taiwan’s China Airlines orders Boeing 777X passenger, freighter jets
- Reamer re-tipping extends life of legacy tooling
- Revitalizing the Defense Maritime Industrial Base with Blue Forge Alliance
- Safran Defense & Space opens US defense HQ
- Two miniature absolute encoders join US Digital’s lineup
- Lockheed Martin completes Orion for Artemis II
- Cylinder CMMs for complex symmetrical workpieces
- University of Oklahoma research fuels UAS development