
Global markets may demand the delivery of as many as 33,000 aircraft during the next 20 years. Increased demand for aircraft may be great for business, but it is exposing a mounting challenge for manufacturers in the aerospace industry: the widening talent gap. To meet demand, the aerospace industry will need to supply 679,000 new maintenance technicians between 2016 and 2035, according a report by Boeing. Yet, there is a massive shortage of skilled workers in the aerospace industry and beyond. Of the 3.5 million manufacturing jobs that will be created by 2025, the Manufacturing Institute estimates that 2 million will go unfilled. In that same time, another 2.7 million workers comprising the baby boomer generation will retire. As the pressure to fulfill orders mounts for airplane manufacturers and suppliers, companies across the industry are looking for innovative ways to upskill new and existing workers to keep their plants operating at maximum capacity.
Where technology can help
Wearable devices, smart glasses in particular, are gaining speed as aerospace manufacturers find applications to drive efficiency, accelerate production time, increase first-time quality, and train workers. Boeing is one example.
As the world’s largest aerospace company, Boeing is constantly evaluating new technologies to improve operating efficiency and meet production demands. The company found smart glasses – configured with assisted-reality applications that match workflows and existing tasks – can improve manufacturing processes and expedite employee upskilling. Boeing is seeing transformational results using smart glasses – as much as a 25% improvement in production time – in wire harness assembly.
Smart glasses can deliver critical, non-overlay information to Boeing wire assembling and troubleshooting technicians. Solutions visualize text, diagrams, checklists, and other reference material in the users’ line of sight, while allowing them to keep their hands free to complete tasks, keeping the team connected with data repositories containing information about wires and components. Voice commands can bring up reference images and instructional videos during workflow, allowing new and more tenured associates to train quickly and cover more ground. Technicians can respond faster to issues, and the entire team can produce higher- quality results.
“Improving productivity through wearable technology offers a step function change,” says Randall MacPherson, senior manager of Boeing’s Electrical Strategic Fabrication Center in Mesa, Arizona. “We’ve seen significant productivity increases in our wiring harness facility from this technology where we’ve tested it, and it resulted in a substantial improvement to first-time quality. Wearable technology is helping us amplify the power of our workforce.”
How to upskill with technology

Other aerospace manufacturers can leverage smart glasses to narrow the skills gap. Here are five ways how:
Provide advanced knowledge-capture capabilities. As experienced workers perform their jobs, they can capture videos, images, and audio of procedures and processes directly through their smart glasses. This captured tribal and organizational knowledge can be integrated into workflows built into the software powering the smart glasses, allowing new and less-skilled workers to immediately access recordings and tutorials while performing the task at hand. It also reduces cognitive load and shortens the learning curve by enabling on-the-job training.
Allow for task digitalization and reference. When performing complex manual processes, like aircraft wire harness assembly, workers wearing smart glasses no longer must rely on cumbersome files, PDFs, or instruction manuals. These materials are instead accessible by voice command and presented directly within the worker’s line of sight. Boeing’s MacPherson adds, “Anything that we can do to automate or augment the workers’ understanding of the routing sequence or routing direction is a huge step forward.”
Technicians also can use smart glasses to visualize defects on a specific part and quickly pull up repair guides and videos. As these engineers troubleshoot, they can document and record the procedure, taking before-and-after photos and creating an audit trail for quality assurance purposes.
Offer real-time collaboration and training. With smart glasses, workers can instantly communicate with other staff in the manufacturing facility or across manufacturing sites globally. One of the applications this is most commonly used for is remote expert guidance. If an error occurs on the plant floor and the technician is unsure how to handle the situation, he or she can use voice commands while wearing the glasses to call an expert for guidance. If necessary, the technician can provide see-what-I see live video to allow step-by-step instructions.
Improve resource allocation and utilization. With a more connected workforce, managers can optimally redirect resources to address bottlenecks and increase throughput. Regardless of the employees’ level of experience or trained expertise, smart glasses can allow workers access to multiple workflows, reference materials, and documented procedures, helping manufacturers to operate with greater flexibility, doing more with fewer employees.

Attract the next-generation of workers. A PwC study found that 59% of millennials say that an employer’s provision of state-of-the-art technology is important to them when considering a job. Embracing wearable technology helps aerospace manufacturers showcase their technology prowess and appeal to the next generation of young, tech-savvy, hands-on workers. Simultaneously, manufacturers can provide a solution that can impact the speed at which new workers can be trained and able to take on more advanced tasks to help close the talent gap.
“My objective is to attract and maintain and keep a younger generation,” MacPherson says. “How do you do that? Well, you introduce new technology that’s cutting-edge to show them that we’re on the cutting edge of technology. That is a powerful magnet for the younger generation, in particular.”
The use of smart glasses in manufacturing settings is gaining speed, with more dramatic results to be had. As aerospace companies look to meet increasing demand in production while bridging the talent gap, this new and promising technology provides a compelling solution that can be applied to nearly any executable task requiring hands-on work.
Jason DeStories, an R&D engineer at Boeing, agrees.
“I think the technology will go across the board, from cutting the wires and lining up the wires to inserting the wires,” he says. “From that point on, it just goes right out to the line. It’s going to increase the speed immensely.”
As aerospace companies deploy smart glasses to different areas within the manufacturing life cycle, they’ll extend the value of their investment and simplify their transition into the Industry 4.0 realm. Those who explore the possibilities of smart glasses now will find that meeting the demand for 33,000 new aircraft during the next two decades isn’t so daunting after all.
Upskill (formerly APX Labs)
About the author: Brian Ballard is CEO of Upskill. He can be reached by phone at 703.436.9283 or email at info@upskill.io .
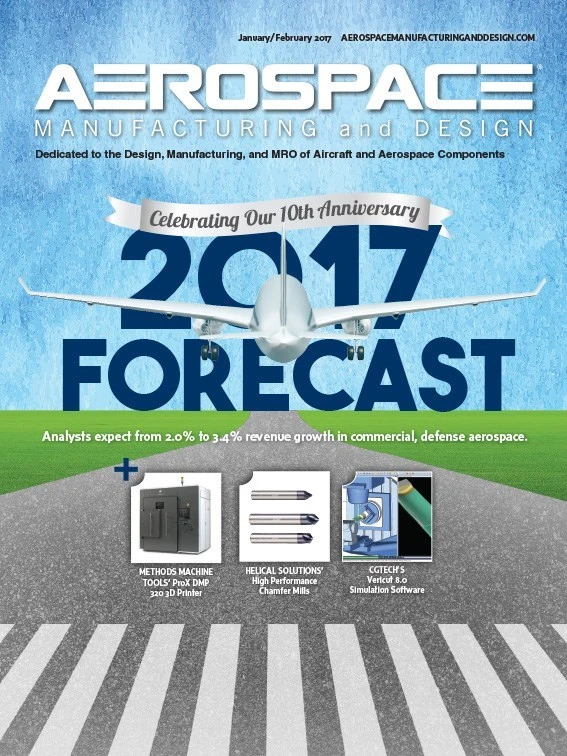
Explore the January February 2017 Issue
Check out more from this issue and find your next story to read.
Latest from Aerospace Manufacturing and Design
- Heart Aerospace relocates to Los Angeles
- Fixtureworks introduces Stablelock Clamps
- Piasecki acquires Kaman's KARGO UAV program
- PI Americas’ long-travel XY piezo nanopositioners-scanners
- AAMI project call submission deadline extended to May 12
- Jergens launches cast iron tooling column additions
- Airbus to acquire assets relating to its aircraft production from Spirit AeroSystems
- FANUC America's Cobot and Go web tool