
The DMP 35 high-speed machining center produces complex workpieces from aluminum to titanium within a 3.15m2 (33.9ft2) footprint.
Traverse paths of 350mm x 420mm x 380mm are on a width of only 1,285mm. An inline spindle with 15,000rpm, direct absolute path measuring systems in all axes, and a tool magazine with 15 places for tools up to 150mm long are standard. Optionally, 25 tool places are possible, which marginally increases the machine’s width to 1,410mm. The modular system also includes a 24,000rpm spindle and HSK-A40 or SK 30 interface. A table for 5-axis simultaneous machining, internal coolant supply, and a chip conveyor are available.
With 1.15m2 (12.4ft2) of additional floor space, the WH 3 compact automation solution increases productivity. New input programming on the WH 3 also simplifies and shortens setup, allowing inexperienced programmers to set up components quickly and easily.

Universal wiper geometries
FW5 and MW5 universal wiper geometries boost feed rates while maintaining consistent surface finish throughout a tool’s life, reducing machining time and aiding productivity. The wiper geometries for turning and facing, with circumference-sintered indexable inserts, reduce cutting pressure, and are suitable for thin shafts and internal machining.
The FW5 wiper geometries, with a new wiper curved cutting edge and V chip formation for short chips, can also be used on components with long overhangs due to reduced cutting pressure. A longer cutting edge makes the MW5 suitable for the highest feeds.
The FW5 and MW5 are available on various inserts. The geometries reduce machining time by increasing the feed up to 300% while maintaining surface quality and can allow users to combine roughing and finishing operations using the same insert.

Scrap bundle breaker
During metal scrap processing, conveyance systems using augers or steel belts frequently fail to consistently move bushy bundles of metal scrap because the augers and steel belts are unable to grab stringy wads. This limitation causes the bundles to bounce around the in-feed hopper until an operator manually breaks them up or forces the bundle up the conveyor. This practice is inefficient and unsafe.
The Bundle Breaker conveyor enhancement preconditions stubborn metal scrap bundles for improved material transfer, processing, and safety.
It installs in a conveyor’s in-feed hopper, where dual rotating cylinders agitate the material, shredding apart stringy wads of chips, turnings, and bundles for effective processing in downstream equipment. The Bundle Breaker may be added to an existing conveyor or incorporated into a new metal scrap processing system.
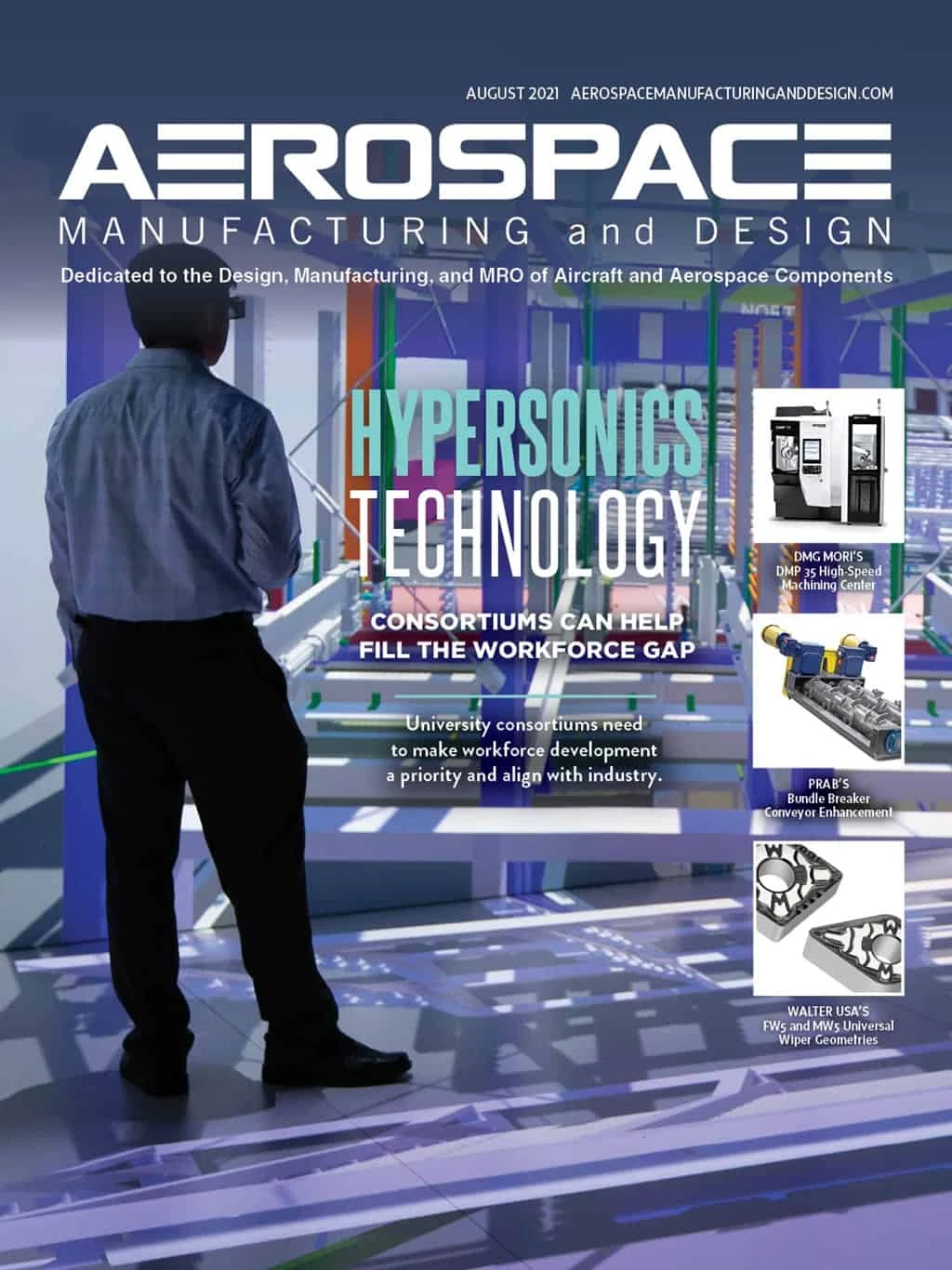
Explore the August 2021 Issue
Check out more from this issue and find your next story to read.
Latest from Aerospace Manufacturing and Design
- Revitalizing the Defense Maritime Industrial Base with Blue Forge Alliance
- Safran Defense & Space opens US defense HQ
- Two miniature absolute encoders join US Digital’s lineup
- Lockheed Martin completes Orion for Artemis II
- Cylinder CMMs for complex symmetrical workpieces
- University of Oklahoma research fuels UAS development
- Motorized vision measuring system
- Everyone's talking tariffs