
Since 1904, Okuma has developed machines that cut metal to create a finished part. Now, the company is broadening its approach – creating machines that can add or subtract material for precision manufacturing. With the latest “do-it-all” technologies, Okuma’s machines advance multitasking and bring unparalleled ease of use and flexibility to today’s shop floors.
The MU Laser EX multitasking machine offers milling, turning, and laser metal deposition while the MULTUS Laser EX offers
“At Okuma, we are the one source for every major component on our machines,” explains David Fischer, lathe product specialist at Okuma. “We are known to provide our own controls, motors, and drives. With the Laser EX, we are partnering with Trumpf Inc., a recognized leader in laser technology, and want to be able to provide the customer all the pieces of the puzzle to make this work.”
One part of that puzzle is the machine’s laser. The Trumpf TruDisk laser offers flexibility across a wide power range with excellent maximum beam quality. The 4kW laser powers up to six machines, offering an advantage unique to hybrid machining where the laser may be used for just a fraction of the total machining time, resulting in lower cost and better laser utilization. This system also provides “on the fly” variable control of laser spot diameters from 0.4mm to 8.5mm which increases laser efficiency and resolution.
The disc laser design ensures a long laser lifetime and eliminates risks associated with other fiber-delivered, solid-state lasers. A plug-and-play optical fiber connection allows the use of multiple fiber diameters for optimum processing results. Power stability of <1% is achieved throughout the laser’s lifetime. Possible applications for the laser include cutting, remote welding, deep penetration welding, large-area welding, brazing, deposition, and laser hardening.
“Unlike other fiber-delivered, solid-state laser technologies, the disk laser is insensitive to back reflection, making it a robust and reliable manufacturing tool for processing even highly reflective materials such as aluminum and copper,” says Frank Geyer, product manager for additive manufacturing at Trumpf.
The laser’s power output and beam size are controlled by Okuma’s OSP-P300 control, which handles all the machine’s operations including motion control, laser control and operation, and powder feed.

Laser metal deposition
The machine implements laser metal deposition (LMD) to form parts in a variety of shapes and sizes through a controlled process. While, in the past, Okuma machine tools have always removed materials, LMD permits additional material to be added to parts, so users can clad a functional surface or build up a structure, even on an existing 3D surface.
“This process is a mature means of manufacturing and is being used in many industries, even in aerospace,” Geyer says. “The ability to process a large variety of materials and join dissimilar materials makes it a very interesting option for users.”
With LMD, four different materials can be used simultaneously, and the user can easily switch back and forth. By the end of the process, the user can come in with cutting tools to create a very fine finish.
Due to the shield gas,
With LMD, users can also perform metal cladding. Rather than selecting

Applied safety measures
To protect the machine and users from the laser and metal powders, Okuma implements several safety systems into the machine. The machine is sealed against laser emissions and contains the metal powder. Mist and dust collection is critically important, so Okuma worked with Camfil to provide units based on the specific machine envelope. Meanwhile, the Nilfisk 118 EXP vacuum cleaner uses an immersion-type system to clean inside the machine when changing over from one setup to the next, as well as cleaning up after changing out powder in the powder hoppers.
Technology of the future
“If you look back at the original Okuma machine tool up to the introduction of the Laser EX, we have always removed material,” Fischer says. “So, this is really a huge change for the industry. Now, with the same machine, we can add material. It’s the first time we have been able to do it… and that allows us to do a lot of exciting things.”
One capability the machine allows users to do is select the material they want, where they want it. Geometric freedom is also possible, which permits any necessary changes to the physical makeup of the part.

For example, a customer can switch between materials on the fly and combine materials if required. The physical
The machine also excites interest in repair work. If a component is worn, whether it is a die-mold component or large engine components, the worn part can go into the machine, where the Laser
“Much greater consistency is possible using the Laser
“We are going to be amazed about where the technology takes us,” Fischer explains. “That’s my feeling. But there are a lot of
Although the Laser
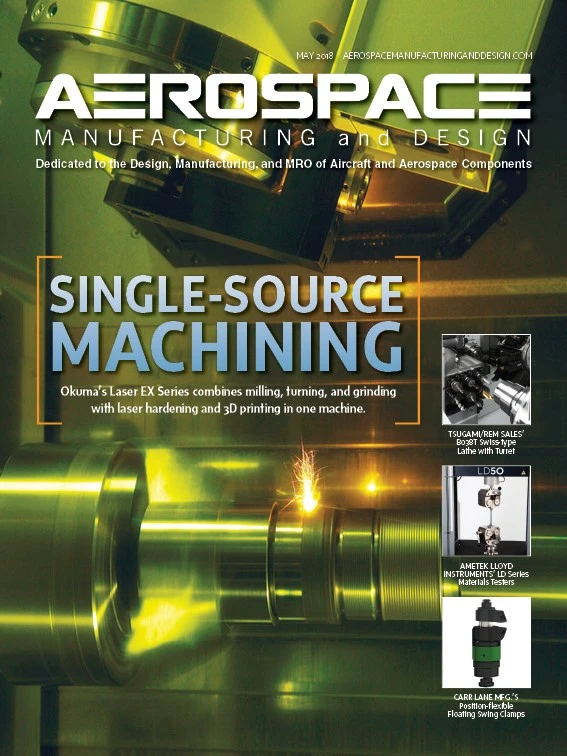
Explore the May 2018 Issue
Check out more from this issue and find your next story to read.
Latest from Aerospace Manufacturing and Design
- #57 - Manufacturing Matters - Agile & Robust Supply Chain Management with Lisa Anderson
- Take control of your manufacturing business despite supply chain turmoil
- Strengthening the defense maritime industrial base for national security, economic resilience
- Register now to learn solutions for high-temperature aerospace machining challenges
- Expertise on machining, joining offered in April’s Manufacturing Lunch + Learn
- NASA offers free high school engineering program this summer
- Pemamak's PEMA Vision 3D software
- Aerospace Industry Outlook - Spring 2025, presented by Richard Aboulafia