

The FH630SXi 5-axis machine performs complex part production and multi-surface processing in one setup on a 630mm platform. A tilting swivel motion processes large workpieces.
The pallet, pallet height, and workpiece restrictions (swing, height, and weight) match existing FH630SX-i horizontal machining centers.
It features an 8,000rpm high-torque spindle, with an optional 15,000rpm high-power, multi-use spindle and a replaceable taper design for high maintainability. The tilting spindle comes with a C-axis drivetrain and an enlarged C-axis swivel range of 230° for wider components.

Rotary encoders
ECN/EQN 1000S, ROC/ROQ 1000S, and ECN/EQN 1100S rotary encoders with integrated Siemens Drive-CLiQ interface feature a compact design with 35mm diameter, while permitting an operating temperature of 95°C.
The combination adds to existing small-diameter 1000/1100 series encoders with the same mounting dimensions using EnDat and SSI interfaces.
ECN/EQN 1100S encoders for motor integration feature a 23-bit single-turn resolution and a 12-bit resolution mechanical multiturn gear. The encoders also include a 6mm hollow shaft with anti-rotation element and a stator coupling. They are mechanically connected by axial clamping with mechanical fault exclusion.
ECN/EQN 1000S series rotary encoders are available with a 6mm blind hollow shaft for radial clamping and a stator coupling, while the ROC/ROQ 1000S series encoders are available with a 4mm solid shaft and a synchro flange.

Workpiece positioning system
The manual WPS and WPS-PPD workpiece positioning systems feature a manual zero-point clamping system for turning, milling, inspection, and finishing. They can reduce setup time up to 90% without requiring conventional clamping devices. Accessories and adapters ensure flexible clamping (without interfering with machining or contours) of nearly every workpiece geometry, making them suitable for 5-axis machining. All clamping modules are proof-line sealed, reducing maintenance.
WPS series’ clamping pins with adapter for workpiece clamping or top mounting are case hardened with corrosion-resistant coating. The M12 or M16 mounting screws maxize stability and stiffness. Clamping modules come in 40mm, 60mm, 80mm, and 160mm heights. Clamping modules can be mounted on a T-slotted table or grid plate manufactured with tempered steel with a coating to protect against rust and contaminants.
Get curated news on YOUR industry.
Enter your email to receive our newsletters.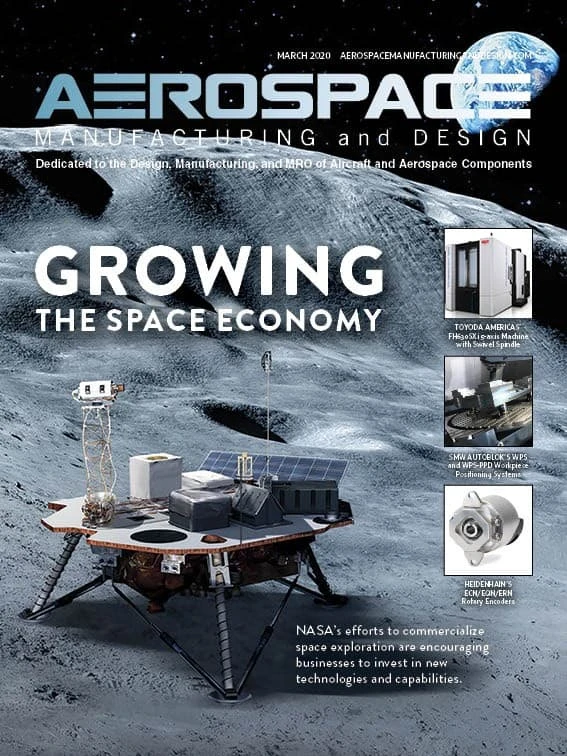
Explore the March 2020 Issue
Check out more from this issue and find your next story to read.
Latest from Aerospace Manufacturing and Design
- Ralliant to establish global headquarters in North Carolina
- Philatron MIL-DTL-3432 military cables
- Beyond Aero refines its hydrogen-electric light jet
- Americase's advanced protective solutions
- Social media - what are your thoughts
- GE Aerospace secures Air Force engine contract
- Thomson Industries' online sizing and selection tool
- #53 - Manufacturing Matters - 2024 Leaders in Manufacturing Roundtable