
To help make lightweight composites that won’t crack or break after prolonged exposure to environmental or structural stress, researchers at the National Institute of Standards and Technology (NIST) have developed a way to embed a nanoscale damage-sensing probe into a lightweight epoxy and silk composite.
The probe, known as a mechanophore, could speed up product testing and potentially reduce the time and materials needed to develop new composites.
The NIST team created their probe from a dye known as rhodamine spirolactam (RS), which changes from dark to light in reaction to an applied force. In the experiment, the molecule was attached to silk fibers contained inside an epoxy-based composite. As more force was applied to the composite, stress and strain activated the RS, causing it to fluoresce when excited with a laser. The change was not visible to the naked eye, but an NIST-designed-and-built red laser and microscope photographed the composite’s inside, showing minute breaks and fissures, revealing points where the fiber had fractured.
The epoxy was combined with silk filaments prepared by Professor Fritz Vollrath’s group at Oxford University using Bombyx mori silk worms. Fiber-reinforced polymer composites such as the one used in this study combine the strength of the fiber and toughness of the polymer.
The resilience of the interface where the components meet is critical to a composite’s ability to withstand damage. However, thin, flexible interfaces favored by designers and manufacturers make it challenging to measure a composite’s interfacial properties.
“There have long been ways to measure the macroscopic properties of composites,” says researcher Jeffrey Gilman, who led the NIST team. “But for decades the challenge has been to determine what was happening inside, at the interface.”
One option is optical imaging. However, conventional methods for optical imaging can only record images at 200nm to 400nm. Since some interfaces are 10nm to 100nm thick, such techniques can be ineffective for imaging the composites’ interphase. By installing the RS probe at the interface, the researchers could determine interface damage using optical microscopy.
The NIST research team plans to explore how such probes could be used in other kinds of composites. They also want to use such sensors to enhance the composites’ ability to withstand extreme cold and heat and prolonged exposure to water.
Additionally, the team plans to search for more ways the study’s damage sensors could be used to improve existing composite standards and create new standards, ensuring that the materials are safe, strong, and reliable.
“We now have a damage sensor to help optimize the composite for different applications,” Gilman says. “If you attempt a design change, you can figure out if the change you made improved the interface of a composite or weakened it.”
National Institute of Standards and Technology
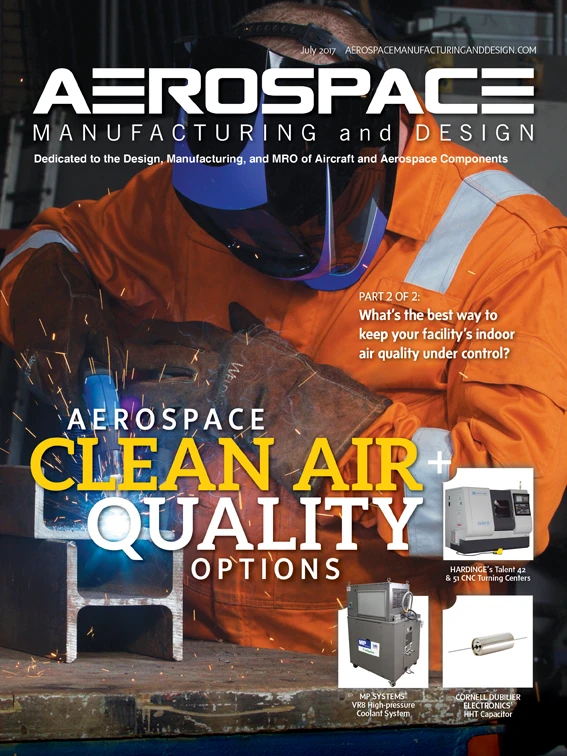
Explore the July 2017 Issue
Check out more from this issue and find your next story to read.
Latest from Aerospace Manufacturing and Design
- Address the challenges of machining high-temperature aerospace components
- Elevate your manufacturing operations with April’s Manufacturing Lunch + Learn
- America Makes announces IMPACT 3.0 Project Call worth $4.5M
- Updated parting and grooving geometries from Sandvik Coromant
- AIX showcases the future of air travel
- Sunnen Products' PGE-6000 gage
- #41 Lunch + Learn Podcast - SMW Autoblok
- Revolutionizing aircraft design without sacrificing sustainability