
When an industry is at its most buoyant, as is the case in the current commercial aerospace market, it creates its own set of challenges. The surge in demand for airplane orders and maintenance is straining manufacturing and its associated supply chain. Backlogs at Boeing and Airbus illustrate this perfectly. In February 2016, the Airbus backlog was just short of 7,000 while Boeing was nearing 6,000.
Aerospace and maintenance and engineering companies need to ensure they are creating efficiencies in all areas and become knowledgeable on implementing change while maintaining quality standards and industry compliance.
Aerospace is a highly demanding industry when it comes to surface finishing performance requirements, and it is rightly renowned for its robust standards for the manufacture and repair of high-performance equipment. Components need to be able to withstand friction, extreme temperatures, and corrosive environments while continuing to operate at optimum levels. And, the manufacturing processes must meet increasingly stringent health and safety requirements.

When plating aerospace parts, engineers are faced with a challenge. Cadmium has long been used to provide a sacrificial coating that corrodes in preference to the substrate, a property which is especially important when the substrate is scratched or damaged. Low hydrogen embrittlement (LHE) cadmium plating remains the choice for aircraft components as the plating provides corrosion protection without degrading the mechanical properties of high-strength steels. But due to its toxic nature, there is tremendous pressure in Europe and in the U.S. to stop its use. So, identifying a suitable, LHE cadmium replacement is of great interest.
SIFCO Applied Surface Concepts (ASC) has developed Zinc-Nickel LHE and Tin-Zinc LHE brush plating solutions to meet this challenge. Coatings including nickel, nickel-tungsten, cobalt chromium carbide, and silver are also available to enhance other areas of the aircraft. These coatings can improve corrosion protection, wear resistance, and electrical conductivity, while enhancing lubricity, performance, and in-service life.
A proven process
The aerospace industry was one of the first to widely accept and approve the trademarked SIFCO Process – a form of selective plating – to restore worn and corroded metal components. An example is the Federal Aviation Administration’s (FAA) Advisory Circular 43.13-1B which contains methods, techniques, and practices (including selective plating) acceptable for the inspection and repair of non-pressurized areas of a civil aircraft when there are no manufacturer repair or maintenance instructions.
Although damage from wear, corrosion, or mis-machining can be repaired using selective brush plating, the SIFCO Process should not only be considered for repair or salvage. The full range of pure metal and alloy deposits available offer similar benefits for OEM component applications.
Selective plating is already approved worldwide by most major airlines, landing gear, and engine manufacturers, and is specified in overhaul manuals and standard practice manuals. SIFCO ASC works closely with aerospace customers to offer options for repairing and enhancing component surfaces. A travel kit for touch-up applications is designed for aircraft on ground operations where turnaround time is critical.
Cadmium LHE and Zinc-Nickel LHE are used for corrosion protection on structural components and as equipment packages for the application of AeroNikl/sulfamate nickel used for pre-braze applications in engine components.
_fmt.png)
The science
The range of metals used in selective plating is extensive. The process is suitable for applying any metals traditionally applied by tank electroplating, such as cadmium, zinc-nickel, nickel, copper, cobalt, nickel- tungsten, cobalt chromium carbide, silver, gold, and platinum.
Several steps are needed to prepare a surface to receive an adherent deposit, with the appropriate preparatory procedure determined by both the substrate of the component and the plating solution to be applied.
The thickness of the plating is controlled through use of an ampere-hour meter. Once the required ampere hours are reached, plating is stopped, finished with a water rinse, then dried.
Automating the process
The process can be carried out manually, it can be mechanized, or it can be automated for higher volume applications – something not traditionally associated with selective plating.
For example, one leading aerospace manufacturer tasked SIFCO ASC to design a machine for landing gear repair. The key challenge: localized areas on the bogie beams were getting damaged while being retracted into the fuselage. The engineering team designed and manufactured a robotic system that would automate the selective plating process for installation into a production line. The result reduced cost and boosted production efficiency for the customer while enhancing component supply chain control and traceability.

The future
Selective brush plating has evolved from its origins of touching up existing plating jobs and is now considered an overarching term describing a highly technical process used for repairing or improving surface properties. It is specified in the initial engineering design specification as well as being called out for component repair. The various advantages provided by the SIFCO Process, combined with the wide range of engineered deposits, make it a choice for OEM and repair applications. In a sector where time is at a premium, selective plating should always be considered a viable alternative to other methods of metal deposition – especially where already written into a specification.
SIFCO ASC
About the author: Derek Vanek is technical manager at SIFCO Applied Surface Concepts (ASC) where he oversees training, technical support, engineering, and R&D. He can be reached at 216.524.0099 or dvanek@sifcoasc.com.
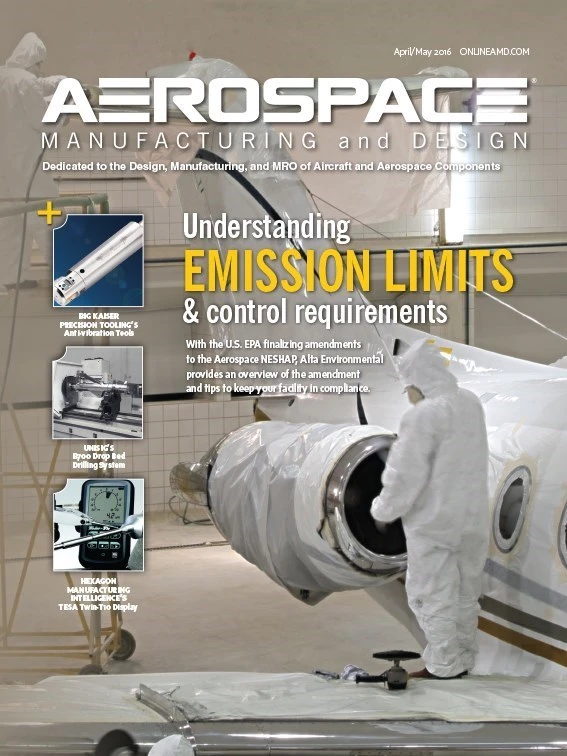
Explore the April May 2016 Issue
Check out more from this issue and find your next story to read.
Latest from Aerospace Manufacturing and Design
- Revitalizing the Defense Maritime Industrial Base with Blue Forge Alliance
- Safran Defense & Space opens US defense HQ
- Two miniature absolute encoders join US Digital’s lineup
- Lockheed Martin completes Orion for Artemis II
- Cylinder CMMs for complex symmetrical workpieces
- University of Oklahoma research fuels UAS development
- Motorized vision measuring system
- Everyone's talking tariffs