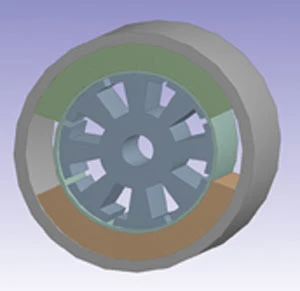
Customers were asking for a modeling preprocessor that would shrink the prep time for finite element analysis, but creating the software in-house from scratch wasn't feasible for ANSYS Inc. Customers typically work from CAD data that they import into their ANSYS applications. But it takes a lot of work to ready a CAD model for simulation. The main problem is that there's too much information in the CAD model. This level of detail makes the analysis mesh so large that it takes a prohibitively long time to run the simulation calculations. "What analysts need to do is simplify the CAD model," explains Barry Christenson, manager of product marketing at ANSYS. "The longer it takes them to do that, the longer it takes to get the analysis results. And if a company is going to use simulation results to guide a design, as many companies do these days, they need results quickly."
In the past, analysts either used a CAE preprocessor with some geometry capabilities to manually make simplifications to the CAD model's geometry or they used a regular CAD program to create their own simplified version of the design. Both methods were time-consuming, but the more serious drawback was that all that preliminary work was lost when the original design model changed. ANSYS, listening to customers' requests for a more streamlined approach that would deliver analysis results sooner, knew it needed to offer a better preprocessor. Ideally, the new one would provide unique model simplification capabilities while also maintaining associativity with the original CAD model. The catch: tight constraints in terms of dollars and development personnel.
Expertise Nearby
Instead of developing the new geometry creation and editing preprocessor in-house from scratch, ANSYS decided that it would be a better use of its resources to leverage Parasolid's state-of-the-art geometric modeling functionality and make it the foundation of its program. One of the component software tools from Siemens PLM Software, Parasolid is the world's leading geometric modeling kernel.

ANSYS DesignModeler was used to produce this blade.
ANSYS has been using Parasolid successfully, in meshing and analysis applications, since 1998. "We recognized there was little value for us in trying to recreate something that is commercially available and so wellproven in the marketplace," says Mike Carroll, a technical fellow at ANSYS and the person in charge of creating the new preprocessor. "Parasolid demonstrated its value in our meshing applications. Not only is it extremely stable, it is powerful enough to let us create the kind of unique features we wanted in the new preprocessor, such as tools for intelligently simplifying a CAD model."
Another important benefit for ANSYS was Parasolid's wide industry acceptance. Parasolid is the foundation of many of the world's leading CAD programs. More than one million CAD users worldwide work with Parasolid- based software. "The fact that a Parasolid foundation would make our preprocessor compatible with this huge community of users was also important," Carroll says. "The alternative, requiring customers to perform file translation before they could import files into our preprocessor, is inefficient and would work against sales, and against our goal of delivering analysis results sooner."
Right Software at Right Cost
Four developers created the new product, which ANSYS named ANSYS DesignModeler. Using Parasolid, ANSYS was able to give ANSYS Design- Modeler the unique model simplification features analysts had been asking for. For example, ANSYS DesignModeler can import assembly models and convert them automatically to a single part. It can convert solid models to surface models and interpret userspecified points as spot welds or "hard points" for loads representing real manufacturing processes.
Users can create patch areas to represent thin sheet metal parts. These capabilities save a great deal of time in preparing a model for analysis, achieving the goal of delivering results sooner. Also, models created in ANSYS DesignModeler are associative to the original CAD model so that changes to the original do not necessitate a complete revision of the simulation model. When the CAD model changes the simulation model can be updated automatically.
"Without a versatile geometric modeling kernel such as Parasolid, we wouldn't have undertaken the task of creating a new preprocessor," says Carroll. "Parasolid made the project possible by making it cost-effective, and by allowing us to deliver precisely what our customers wanted - modeling software uniquely packaged for their needs."

Explore the May June 2008 Issue
Check out more from this issue and find your next story to read.
Latest from Aerospace Manufacturing and Design
- 2024 Favorites: #5 Article – Solving workforce issues with digital transformation
- 2024 Favorites: #5 News – GE Aerospace is investing in manufacturing
- 2024 Favorites: #6 Article – Mastering complex precision machined parts
- 2024 Favorites: #6 News – Boeing to acquire Spirit AeroSystems in $8.3B deal
- Season's greetings
- 2024 Favorites: #7 Article – Deep drawing aerospace components
- 2024 Favorites: #7 News – GKN Aerospace completes sale of St. Louis facility to Boeing
- 2024 Favorites: #8 Article – Beyond uptime