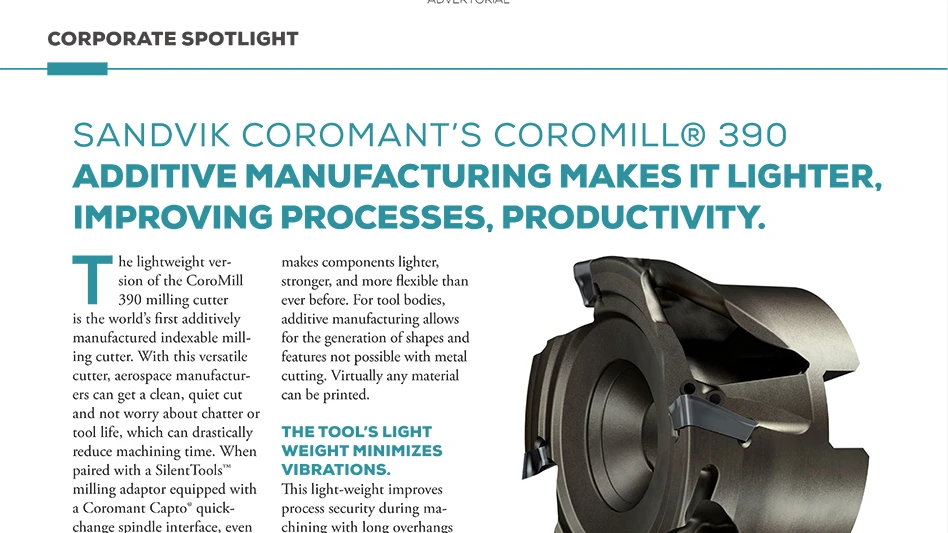
GIE Media

The lightweight version of the CoroMill 390 milling cutter is the world’s first additively manufactured indexable milling cutter. With this versatile cutter, aerospace manufacturers can get a clean, quiet cut and not worry about chatter or tool life, which can drastically reduce machining time. When paired with a SilentTools™ milling adaptor equipped with a Coromant Capto® quick-change spindle interface, even higher process security is achieved. Here are five things to know about the Lightweight CoroMill 390.
The cutter body is 3D printed in titanium alloy.
Additive manufacturing offers a superior way to produce complex structures with high precision and without joints. Using additive manufacturing makes components lighter, stronger, and more flexible than ever before. For tool bodies, additive manufacturing allows for the generation of shapes and features not possible with metal cutting. Virtually any material can be printed.
The tool’s light weight minimizes vibrations.
This light-weight improves process security during machining with long overhangs and also increases productivity. When designing the cutter body, material was tactically removed to create the optimal cutter design for minimizing mass. Called topological optimization, it makes the cutter more compact and significantly lighter than the conventional version, thus helping machine shops boost productivity for long-overhang milling operations.
For even more stability, it can be paired with a damped adapter.
When combined with Silent Tools™ milling adapters, this optimized tooling combination subdues vibration to help maximize productivity and process security in demanding applications involving long overhangs. The shorter distance between the damper in the adapter and the cutting edge improves performance and process security.

It offers light cutting action.
The Lightweight CoroMill 390 concept delivers light cutting action for smooth cutting performance. Process security is paramount in aerospace metal cutting applications. When milling long overhangs or complex component features, such as deep cavities, applications can be compromised by vibration, leading to slower production, shorter tool life, and poor surface finish.
It’s ideal for long-reach face milling…
And deep shoulder and side milling, cavity milling, and slot milling. This versatile tool is available in 40mm (arbor 16 coupling) and 50mm (arbor 22 coupling) diameter variants. Three or four inserts (size 11) can be specified to suit the demands of the application. Differential pitch and internal coolant are available on all cutters. To learn more about Sandvik Coromant’s Lightweight CoroMill 390, visit https://www.sandvik.coromant.com/coromill390.

Explore the October 2020 Issue
Check out more from this issue and find your next story to read.
Latest from Aerospace Manufacturing and Design
- Safran inaugurates advanced manufacturing and engineering hub
- Dillon pin location jaws
- NASA-supported technology outfits Venus Aerospace hypersonic engine
- To the Smoothest Surfaces, Finishes, and Beyond | Okuma GA26W
- Extraordinary Starts Where Limits End | Okuma
- Satair, Champion Aerospace sign multi-year distribution agreement
- EMUGE-FRANKEN USA expands N. American solid carbide drill program
- AURA AERO unveils INTEGRAL R to the US market