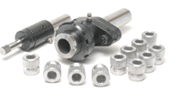
Manufacturers can cut internal and external forms rapidly and accurately into workpieces with rotary broach tooling and can produce precise hexes, squares, serrations, splines, and other custom shapes on CNC machines.
An internal live spindle holds an end-cutting broach tool at a 1° angle. In a lathe, the rotary broach toolholder is stationary while the spindle and rotary broach rotate 1:1 with the workpiece. Driven by the workpiece, the rotary broach tool’s corners continually change contact points on the workpiece, wobbling while it cuts each corner of the form rapidly.
In a mill or vertical machining center (VMC), the toolholder’s body rotates in the machine spindle while the holder’s spindle and broach remain stationary, creating the wobbling action while the rotary broach tool’s corners continually change contact points on the workpiece. Form sizes can be broached up to 2" in aluminum or brass and 1" in steel, with depths up to 1.5x the form’s minor diameter.
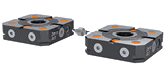
Workpiece positioning system
The connectable ZeroAct workpiece positioning system offers manual and electric zero-point clamping in milling, inspection, and finishing.
Modules rapidly and simultaneously open and close, generating 15kN clamp force. Up to three 40mm x 150mm x 150mm clamping modules can be attached in a row with connecting pins from 5mm to 105mm. By actuating the first unit, all three units clamp simultaneously.
An electric e-motion version uses 24V power that operates with a built-in electro-motor for fully automated loading and unloading. Pull-down pins are interchangeable with the manually operated ZeroAct and other APS/WPS zero-point systems.
Modules provide repeat accuracy of <0.005mm, are sealed against corrosion, and feature built-in air cleaning so the clamping system’s support surface remains clean and free of chips.
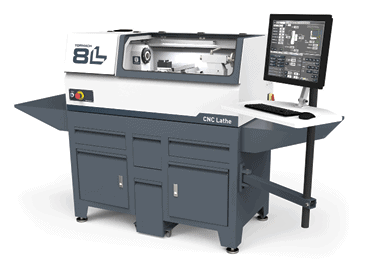
Compact lathe
The 8L lathe can fill turning needs in a variety of spaces. Rigid enough to cut plastic, stainless steel, or titanium, it can be equipped with an integral coolant tank, separate chip drawer, storage drawers, side shelving, and a tool holder/tool kit.
The lathe’s 5C spindle accommodates parts up to 1" diameter, and users can add a 3- or 4-jaw chuck to cut stock up to 8" in diameter.
Intuitive conversation lathe programming PathPilot software lets operators do rigid tapping and leverage built-in Dropbox support for transferring programs.
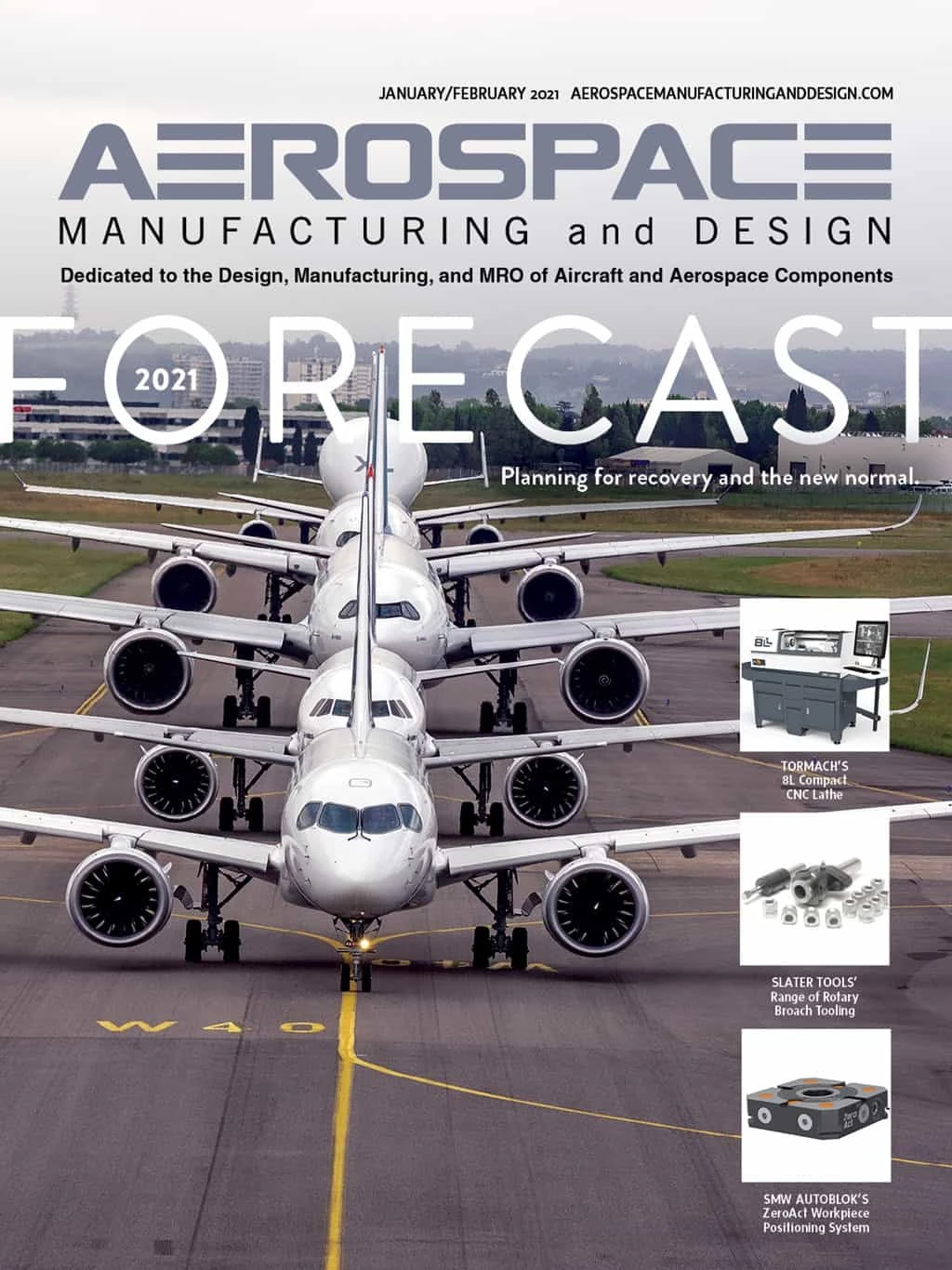
Explore the January February 2021 Issue
Check out more from this issue and find your next story to read.
Latest from Aerospace Manufacturing and Design
- AAMI project call submission deadline extended to May 12
- Jergens launches cast iron tooling column additions
- Airbus to acquire assets relating to its aircraft production from Spirit AeroSystems
- FANUC America's Cobot and Go web tool
- Chicago Innovation Days 2025: Shaping the future of manufacturing
- High-density DC/DC converters for mission-critical applications
- #59 - Manufacturing Matters: Additive manufacturing trends, innovations
- ACE at 150: A legacy of innovation and industry leadership