
Satellite propulsion company, Benchmark Space Systems, designs and develops turnkey bi-propulsion thrusters for smallsat and cubesat projects through evolved secondary payload adapter (ESPA) and orbital transfer vehicle (OTV) class spacecraft in low earth orbit (LEO), geostationary orbit (GEO), and beyond. The company provides propulsion procurement and integration through a range of non-toxic propellants and qualified subsystems such as thrusters, propellant tanks, modular control electronics, and guidance, navigation, and control (GNC) integration frameworks.
The company’s Halcyon Avant rocket thrusters use green propellants that are safe to handle.
The Benchmark system made its debut as part of the SpaceX Transporter-3 mission, a rideshare mission which placed 13 payloads into multiple orbits, including four microsatellites and five cubesats in sun synchronous orbit (SSO) at about 342 miles altitude. The additional four cubesats were deployed after the Benchmark Space Systems green propulsion subsystem maneuvered the craft down to a 310-mile altitude.
Benchmark Space Systems’s Ocelot rocket thrusters are designed for in-space satellite and spacecraft propulsion for commercial and government use. Chemical propulsion systems offer maneuverability and deployment of satellites to operational orbits.
In the design of the thrusters, Benchmark needed to join the stainless steel head section to the niobium alloy nozzle used for the thruster’s hot section. Niobium is used because almost any other metal will melt under the 2,000°F temperature differential produced. Stainless steel can’t be welded directly to niobium because a conventional weld would shatter.

Incorporation of explosion bonded transition rings solved the challenge. The transition rings, designed and manufactured by Atlas Technologies, allowed Benchmark Space Systems to make the nearly impossible work. The 2,000°F temperature differential happens within a span of less than 1/2" and the bimetallic transition ring sits at this critical joint in the system.
According to Jake Teufert, Benchmark’s chief engineer on the project, “The thruster could not be built without the Atlas Technologies joint.”
Atlas Technologies specializes in creating solutions for challenges such as the Benchmark Rocket Thrusters through the precision design and machining of a variety of explosion bonded and diffusion bonded materials. Transition rings, such as those used by Benchmark, allow for a clean no-flange transition from one metal to another. They’re available in a broad variety of combinations to provide reliable transitions.
Niobium isn’t only used in rocket engines but also in cars, bridges, buildings with low environmental footprints, and pipelines that safely carry high volumes of gas. Atlas supplies precision components for use in sophisticated devices, including the Hadron collider, large-scale telescopes, spacecraft and satellites, and industrial and chemical processing applications.
When companies such as Benchmark Space Systems require robust dissimilar metal-bonded components that must be precision machined, coated, and polished, they rely on Atlas Technologies because the company has been involved in advanced vacuum technology products and services for more than 20 years. The bimetallic technology allows them to offer aluminum flanges with robust industry standard stainless-steel knife edges, enabling ultra high vacuum (UHV) all-metal seals on aluminum chambers. Additionally, the bimetallic technology can solve challenging problems found in the industry, providing standard products and custom and semi-custom capabilities to customers.
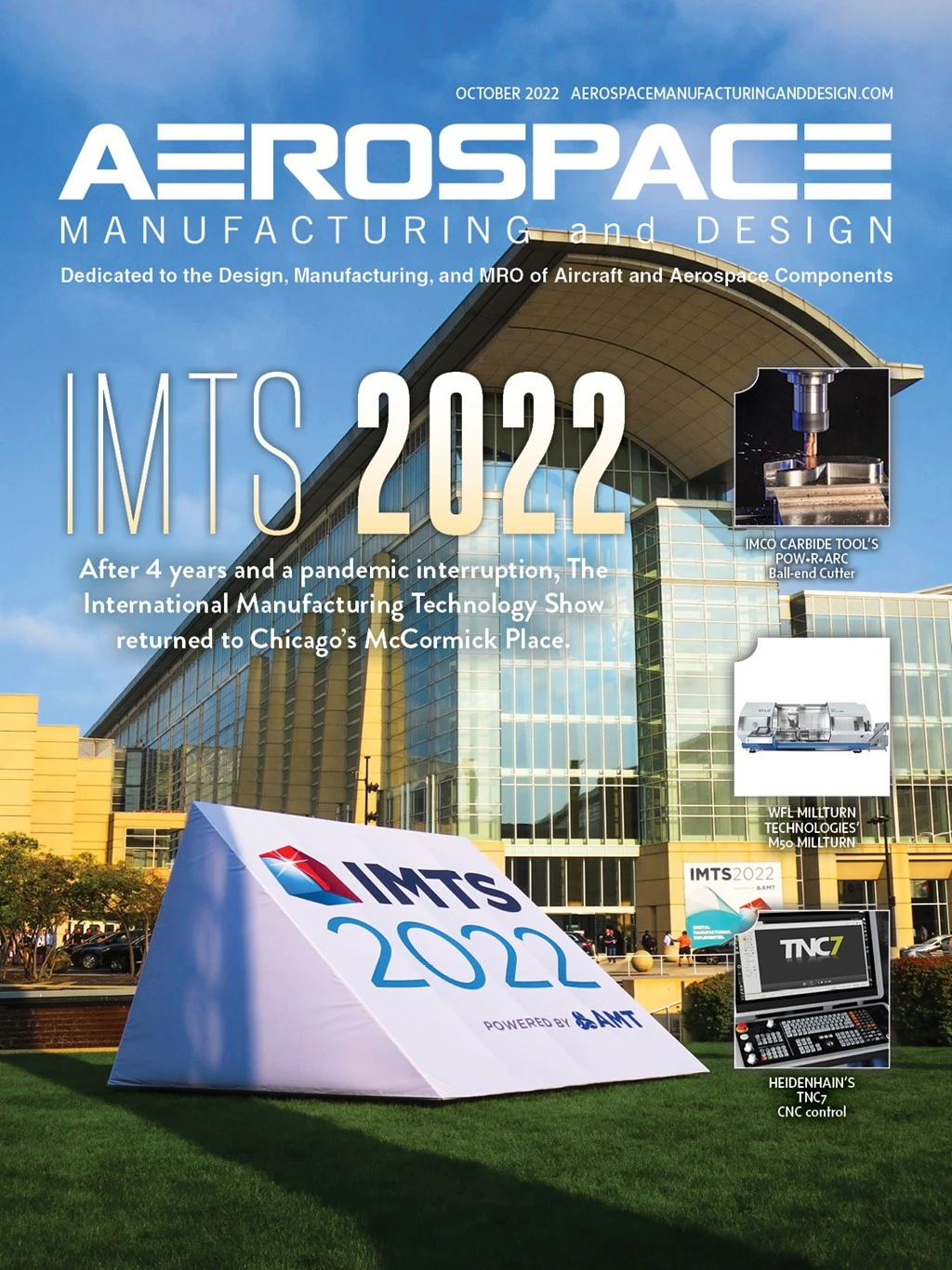
Explore the October 2022 Issue
Check out more from this issue and find your next story to read.
Latest from Aerospace Manufacturing and Design
- Taiwan’s China Airlines orders Boeing 777X passenger, freighter jets
- Reamer re-tipping extends life of legacy tooling
- Revitalizing the Defense Maritime Industrial Base with Blue Forge Alliance
- Safran Defense & Space opens US defense HQ
- Two miniature absolute encoders join US Digital’s lineup
- Lockheed Martin completes Orion for Artemis II
- Cylinder CMMs for complex symmetrical workpieces
- University of Oklahoma research fuels UAS development