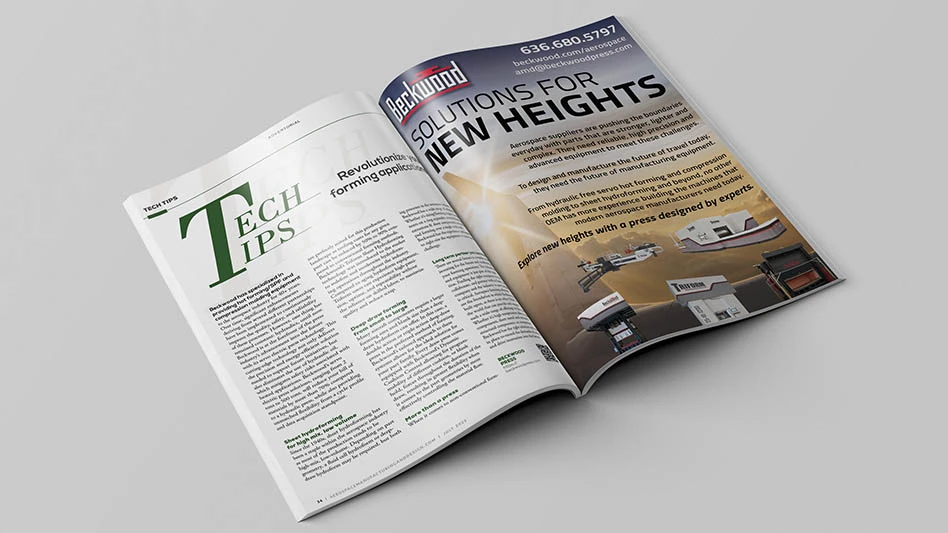
Beckwood has specialized in providing hot forming/SPF and compression molding equipment to the aerospace industry for 40+ years. Over time, significant enhancements deriving from several different partnerships have been implemented to continuously improve the quality, safety, and reliability of these processes. However, one thing has remained constant: hydraulics, until now. Beckwood is at the forefront of the press industry’s advancement into the future with its servo electric press technology. This cutting-edge technology not only delivers the precision and energy-efficient solution needed to support future initiatives, but also eliminates the use of hydraulic oil, which mitigates safety risks associated with heated applications. Beckwood’s servo electric press solutions, ranging from 2 tons to 500 tons, will reduce your bill of materials by more than 70% compared to a hydraulic press, while also providing unmatched flexibility from a cycle profile and data acquisition standpoint.
Sheet hydroforming for high mix, low volume
Since the 1940s, sheet hydroforming has been a staple within the aerospace industry as most of the production tends to be high-mix, low-volume. Depending on part geometry, a fluid cell hydroform or deep-draw hydroform may be required, but both are perfectly suited for this production landscape as tooling costs for any given part can be reduced by 50% to 90% compared to conventional forming methods. Beckwood’s Triform Sheet Hydroforming technology was introduced to the market to redefine and modernize hydroforming operations throughout the industry. Compared to aging hydroform equipment, Triform users can experience high-precision, uptime, and repeatability without the reliance on skilled labor, to maximize quality and reduce scrap.
Deep draw forming from small to large
Many aircraft components require a larger forming area and blank size than a deep-draw hydroform can offer. In this case, a double action or triple action deep-draw press is the preferred method of forming. Beckwood’s tailored approach to these systems allows for the ideal solution for your part family. Every draw press comes equipped with Beckwood’s Dynamic Cushion Control allowing for programmability of different cushion, or blank hold, forces throughout the duration of the draw, resulting in greater flexibility when it comes to the part geometries by more effectively controlling the material flow.
More than a press
When it comes to non-conventional forming processes in the aerospace industry, Beckwood has a wide range of solutions. Whether it’s sizing/forming engine components on a ring expander, stretch forming extrusions & sheet components, or rubber pad forming over a single male tool, Beckwood has the experience and expertise to right-size the equipment to your specific challenge.
Long term partner you can trust
There are several factors to consider when investing for the future and modernizing your forming operations. The technology and equipment is just part of the equation. Finding the right company to trust, collaborate, and partner with to lead your company and the industry to new heights is critical. Aerospace forming solutions are the foundation in which Beckwood is built upon, as there is no other OEM in the world that can provide and support such a wide range of offerings in this space. Whether it’s high temperature alloy engine components, sheet metal and extrusion structural components, or composites, Beckwood has the right solution and team in place to exceed the demands of today, and drive innovation into the future.
Get curated news on YOUR industry.
Enter your email to receive our newsletters.
Explore the July 2023 Issue
Check out more from this issue and find your next story to read.
Latest from Aerospace Manufacturing and Design
- You can still register for March’s Manufacturing Lunch + Learn!
- Ohio creates Youngstown Innovation Hub for Aerospace and Defense
- Tormach’s Chip Conveyor Kit for the 1500MX CNC Mill
- How to Reduce First Article Inspection Creation Time by 70% to 90% with DISCUS Software
- Jackson Square Aviation orders 50 Airbus A320neo aircraft
- Beckhoff's motion control automation solutions
- #40 - Lunch & Learn with Fagor Automation
- Air Methods to purchase up to 28 Bell helicopters