

Resharpening tapered endmills poses specific challenges. I’d like to discuss some fundamental aspects of tapered endmills in this column. There are two types of helically fluted tapered endmills: constant helix and constant lead. The majority of tapered endmills are of the constant helix type.
The definition of a constant helix is that the helix angle remains the same along the taper. This ensures uniform cutting performance throughout the cutting area. In contrast, the constant lead design means the helical advance per revolution is uniform along the tool axis, causing the helix angle to change along the taper.
Here are the formulas for helix calculations:
Lead = 3.1416 x Diameter
Tangent Helix Angle
Tangent Helix Angle = 3.1416 x Diameter
Lead
For example, a 15° inclusive tapered tool with a tip diameter of 0.25", a cutting length of 2.50", and a constant helix angle of 30° has a variable lead ranging from 1.360" at the front to 4.942" at the back.
In earlier years, when CNC tool grinding programs were less sophisticated, only constant-lead tapered tools could be successfully reground multiple times. However, with advancements in tool grinding software, most constant-helix tapered tools can now also be reground to some extent.
Imagine resharpening a straight endmill where the lead and helix angle remain constant. The grinding wheel follows the lead, restoring the same constant helix angle. This isn’t the case with a tapered tool. If the grinding wheel doesn’t follow the exact helical path of the flute (i.e. the lead), the effective helix angle will change. However, this change in helix angle is minor. Based on experience, when resharpening a 10° tapered endmill with a tip diameter of 0.25", the change in helix angle is only about 1° to 2° at the front and even less at the back. The higher the taper angle, the more the helix angle will change.
If the program is forced to restore the exact same helix angle, it’ll need to change the lead, resulting in unequal stock removal along the flute. This usually isn’t an issue, but after multiple regrinds, the land width in the front of the flute will eventually diminish and weaken.
This issue is more pronounced with ballnose endmills, as they require more stock removal to regrind the ball geometry at the front. On a tapered endmill, the land width naturally narrows toward the tip, making it challenging to maintain the original helix angle (or lead) consistently from the back (thick land) to the tip (thin land).
Most CNC tapered tool programs include an option to digitize the existing cutting edge. If you don’t resharpen the flute, you can simply regrind the primary and secondary O.D. angles while maintaining the same helix angle. However, flute resharpening is generally recommended because material deposits and residue may accumulate inside the flute. This is especially true in aerospace machining of aluminum and alloys.
About the author: Eric Schwarzenbach, founder of MyGrinding Inc., retired as president from Rollomatic Inc. – global builder of CNC grinding and laser cutting machines.
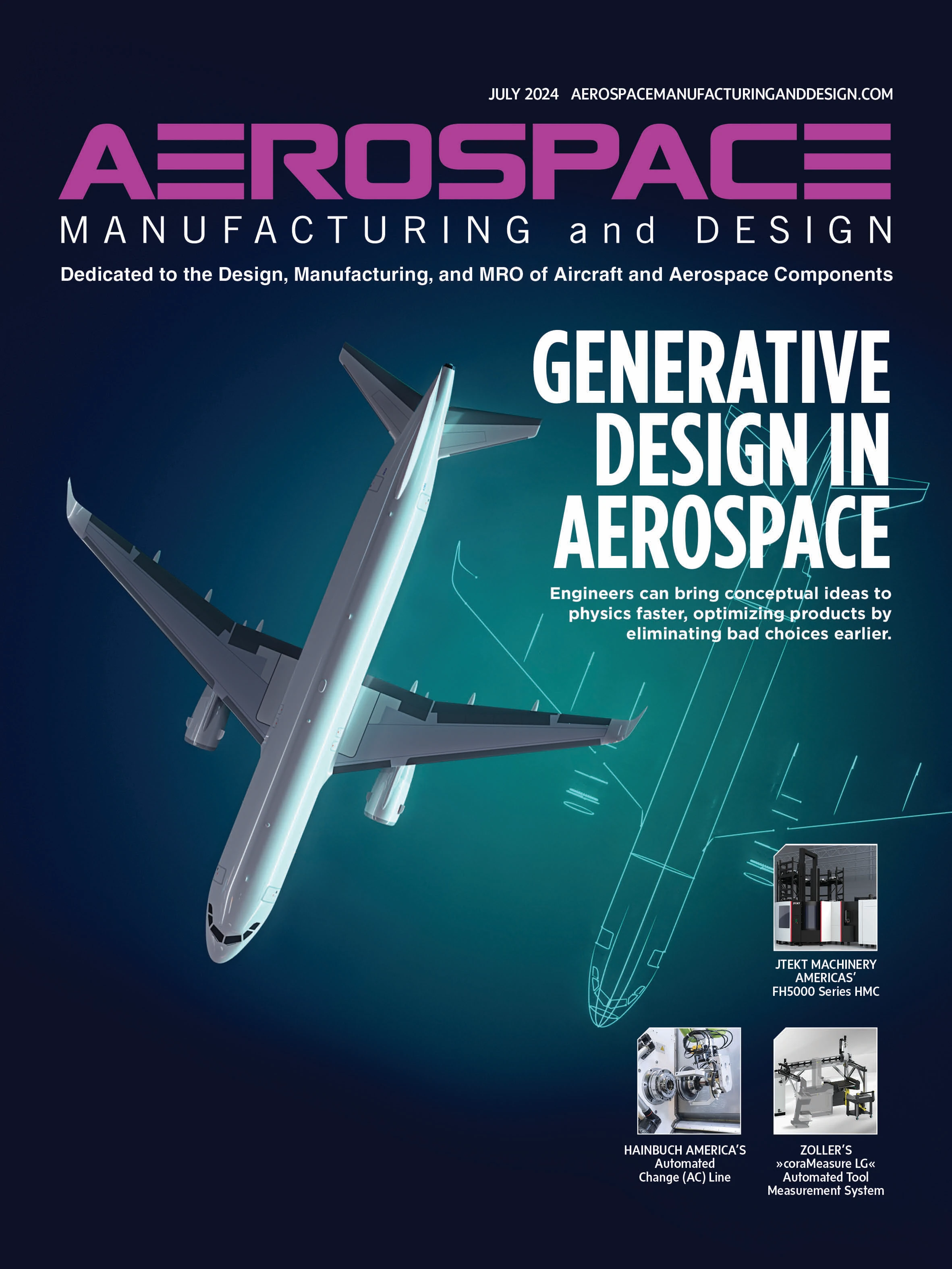
Explore the July 2024 Issue
Check out more from this issue and find your next story to read.
Latest from Aerospace Manufacturing and Design
- AIX shows aircraft interiors are a strategic priority for global airlines
- Machine Tool Builders Roundtable: Turn equipment into expertise
- No time to waste: How to machine MedTech parts more efficiently
- The 5 Best and Fastest Spindle Repair Services
- Mill smarter, not harder: How collaboration optimizes production
- Be proactive – stay ahead of tariffs and other economic and supply chain curveballs!
- Taiwan’s China Airlines orders Boeing 777X passenger, freighter jets
- Reamer re-tipping extends life of legacy tooling