

The runout on a drill, new or resharpened, is defined by the lip height – the height difference between the two lips (cutting edges) relative to the drill’s axis.
Ideally, a drill would be clamped at the cylindrical margins near the tip. However, due to the slight back taper present in all cylindrical margins (to prevent the drill from rubbing against the hole), clamping directly on the margins isn’t feasible. Therefore, the only viable method for holding the drill during sharpening on a CNC tool grinding machine is clamping it by the shank.
Next is the collet system’s accuracy. Even the highest quality collet has some runout.
To accurately resharpen a drill, a tool runout measurement and automatic compensation system must be used. This is typically integrated into most CNC tool design programs. The probe will contact the two cylindrical margins near the tip and make the appropriate compensation, so the entire point geometry can be ground true to the drill’s margins.
In addition to the TIR, two other drill point features are commonly used in high-performance drills.
Many drills used for holemaking are solid carbide and high-performance design, featuring an S-gash and an edge preparation known as K-land.
Most CNC drill programs incorporate the S-gash feature, characterized by a helical gash instead of the conventional straight gash. The S-gash design safeguards the drill center while facilitating successful material penetration along the axis. I recommend regrinding this S-gash as closely as possible to the original design.
CNC program options also include a feature that can grind a small chamfer (K-land) along the lip edge of the drill point. This prevents premature chipping of the cutting edge. Given the narrowness and shallow angle of this K-land, a digitizing program is necessary to determine the existing gash location and flute shape contour. The probing feature guarantees precise positioning and perfect parallelism of the K-land along its entire length.
Major manufacturing facilities frequently purchase drills and regrind them to their specific requirements before initial use. This practice guarantees consistent, predicted tool wear from the first use onward and throughout subsequent regrinds. While the geometry may not precisely match what the drill manufacturer provided, it can be closely approximated, while also giving users the flexibility to fine-tune the point geometry based on their experience and required performance criteria.
One more item: Long-flute drills need adequate support. Once the diameter-to-length ratio exceeds 1:7 or 1:10, use a steady rest or bushing to stabilize the point during grinding.
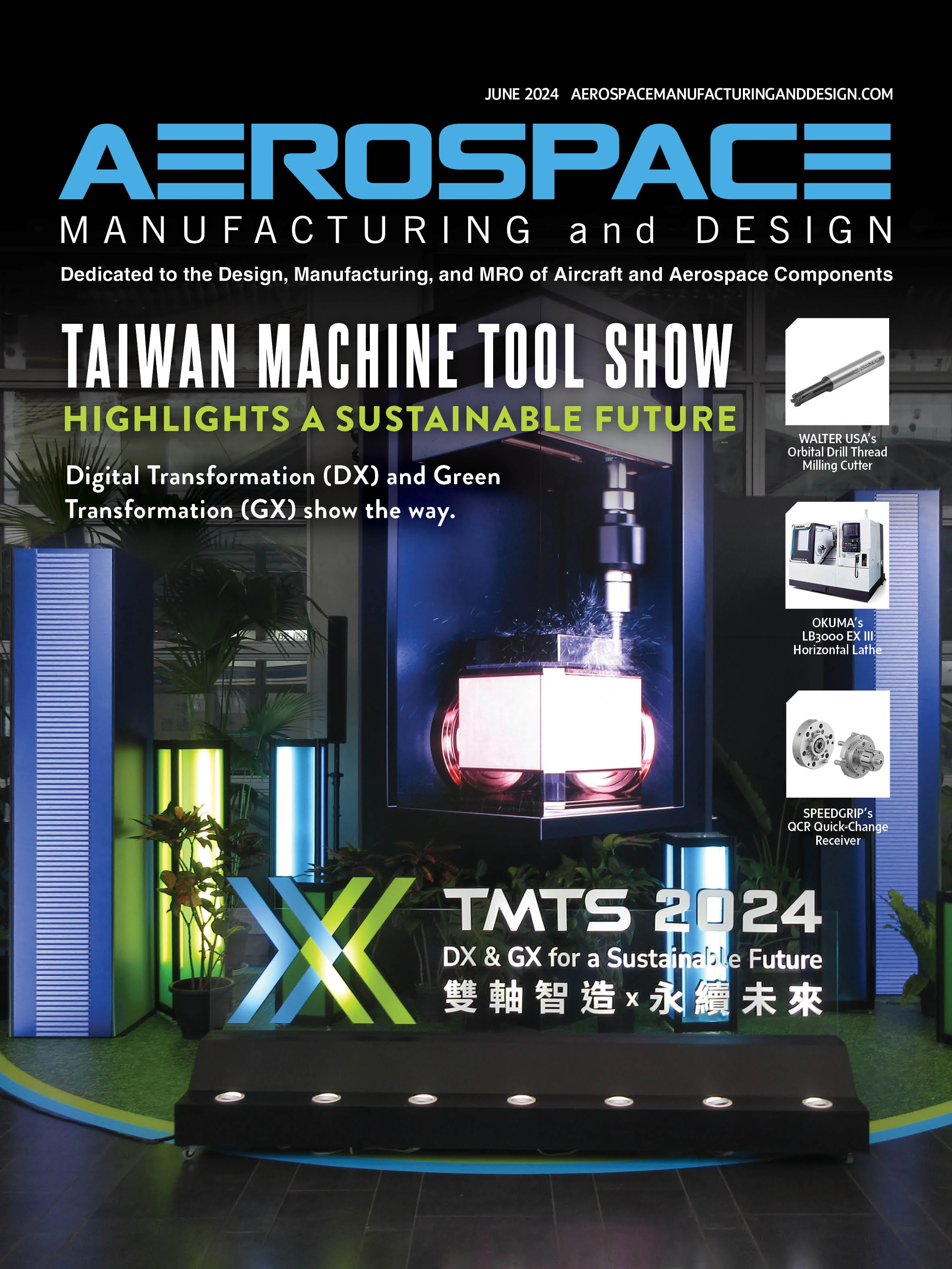
Explore the June 2024 Issue
Check out more from this issue and find your next story to read.
Latest from Aerospace Manufacturing and Design
- AIX shows aircraft interiors are a strategic priority for global airlines
- Machine Tool Builders Roundtable: Turn equipment into expertise
- No time to waste: How to machine MedTech parts more efficiently
- The 5 Best and Fastest Spindle Repair Services
- Mill smarter, not harder: How collaboration optimizes production
- Be proactive – stay ahead of tariffs and other economic and supply chain curveballs!
- Taiwan’s China Airlines orders Boeing 777X passenger, freighter jets
- Reamer re-tipping extends life of legacy tooling