
Additive manufacturing is a process used to create three-dimensional parts from a digital file. It usually involves building up, or solidifying, thin layers of material to create complete parts. The technology is able to produce complex shapes which cannot be produced by ‘traditional’ techniques such as casting, forging and machining. Additive manufacturing introduces new design possibilities, including combining multiple components in production, minimize material use and reduce tooling costs.
We design and manufacture additive manufacturing systems for manufacturing components in a variety of metals using a process called metal powder bed fusion (or laser melting). Our expertise in process development and our experience in using the technology in our own manufacturing operations enable us to provide turn-key and optimized additive manufacturing solutions for a broad range of applications in industrial and healthcare sectors.
Where we specialize?
Productivity –The intelligent case flow design, and precise optical and mechanical control of the RenAM 500 series enables components to be produced with minimal pores and defects, typically >99.9% dense. Process emissions from melt pools are quickly removed from the build chamber, ensuring stable processing conditions and melting behavior. Real-time process monitoring capability provides traceability of the processing performance.
The RenAM 500 series of AM systems can be configured with a choice of one, two, three, or four lasers. The RenAM 500Q is configured with four high-power 500W lasers. Each laser is able to access the entire powder bed simultaneously to achieve the most efficient laser assignment, so the RenAM 500Q can achieve significantly higher builder rates, vastly improving productivity, and lower cost per part.
Performance – Improving the predictability of additive manufacturing to create a consistent and stable process boosts process throughput and the delivery of functional parts.
Solutions Centers – Renishaw Solutions Centers provide a secure development environment in which you can build your knowledge and confidence using additive manufacturing technology.
How can we help you?
Production manufacturers and sub-contractors – Developing additive manufacturing capabilities can be the natural next step in developing your company’s manufacturing capabilities.
Product owners and designers – Metal additive manufacturing allows metal parts to be built without the need for traditional tooling and with few limitations in geometry. Equally, it is complementary to traditional subtractive methods and can be readily integrated into existing production operation.
Service bureaus – Providing versatile systems to enable you to consult, design and build precision finished parts from a variety of materials for your customers. Renishaw’s end-to-end solutions enhance any additive manufacturing service bureaus capabilities.
Research and education – Renishaw partners with many universities, researchers and academic institution on metal additive manufacturing projects. The open parameter ethos for materials used on our systems helps to encourage development of parameters for new materials.
Renishaw is an experienced user of additive manufacturing as a complementary process to its conventional manufacturing operations and can provide expert advice to help in your adoption of additive manufacturing. To learn more about our additive manufacturing systems and services for your industry, visit: https://www.renishaw.com/additive.
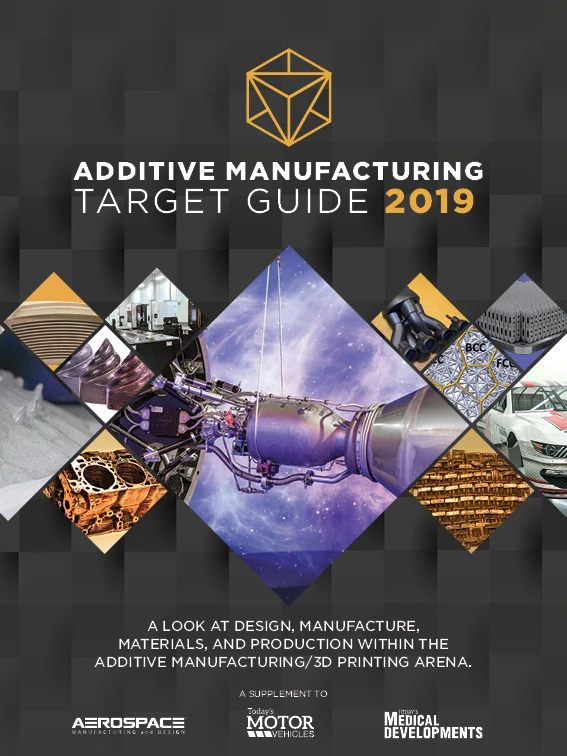
Explore the Additive Manufacturing Guide Issue
Check out more from this issue and find your next story to read.
Latest from Aerospace Manufacturing and Design
- Sandvik Coromant introduces CoroMill Plura barrel
- #54 - Manufacturing Matters - HMI Solutions for EV Industry from EAO
- Aerospace Industry Outlook returns for spring 2025
- Drop in for an interactive webinar on automation in manufacturing
- SW’s wing rib technology for the aerospace industry
- Mach Industries launches Mach Propulsion
- Murata Machinery USA's MT1065EX twin-spindle CNC turning center
- Electra reaches 2,200 pre-orders for its Ultra Short aircraft