
Chandler, Arizona-based Refrac Systems has contracted Solar Manufacturing in Souderton, Pennsylvania, and Beckwood Press & Machinery/Triform in Saint Louis, Missouri, to help design and build a 100-ton load gas fan quench vacuum hot press (GFQVHP) system for its aerospace diffusion bonding operation. The furnace chamber for this unit was built by Amity Industries of Douglassville, Pennsylvania, and the control console unit was built by Optima Stantron in Lawrenceville, Georgia.
Refrac Systems, working with Solar’s engineering team, selected a derivative of Solar Manufacturing’s HLF-5748-2IQ internally quenched 2-bar vacuum furnace as the base design. The new system is designed to be an automated vacuum hot press and make super plastically formed and diffusion bonded (SPFDB) aerospace structures.
Solar Manufacturing expects to ship the GFQVHP system in July 2016, with final assembly, testing, and startup projected for Q4 2016. www.refrac.com; www.solarmfg.com; www.beckwoodpress.com

High-torque spindle chews through titanium
Fives recently demonstrated the highest known titanium metal removal rate using a single spindle at 33.1in3/min. Using a Giddings & Lewis HMC 1600 that combined the machine’s 42.3kN (9,500 lb) cutting thrust with high-torque T-Rex spindle, the test for an aerospace customer on titanium 6Al-4V used a Harvi indexable-insert end mill with 76.2mm (3") tool diameter. The tool was driven at 245rpm with an axial depth of cut at 76.2mm (3") and a radial depth of cut at 25.4mm (1.0"), with a feed rate of 1.14mm/rev (0.044"/rev).
“This cut produced an excellent surface finish with no sign of chatter and virtually no vibration,” says Pete Beyer, director of product strategy and development at Fives Giddings & Lewis. www.fivesgroup.com

Boeing 787-10 Dreamliner begins major assembly
Major assembly of the first Boeing 787-10 Dreamliner is underway. Boeing partner Kawasaki Heavy Industries Ltd. began installing the circular frames into the mid-forward section of the fuselage on March 14, 2016, two weeks ahead of schedule.
Based on the 787-9, which entered service in 2014, 95% of the design and build of the 787-10 and 787-9 will be identical, reducing complexity, cost, and risk across the production system. The 787-10 will undergo final assembly at Boeing South Carolina in North Charleston, with deliveries beginning in 2018. To date, the 787-10 has won 153 orders from nine customers around the world, accounting for 13% of all 787 orders. www.boeing.com

Orion hardware in testing
An international team of engineers and technicians at NASA Glenn’s Plum Brook Station in Sandusky, Ohio, have begun tests to verify the structural integrity of Orion’s service module for Exploration Mission-1, the spacecraft’s first flight. The service module, which will power the vehicle and supply it with air and water, is built by Airbus Defense and Space for the European Space Agency. www.nasa.gov

The MFG Meeting focuses on industry trends, economy; raises funds for skills training
In March, more than 400 manufacturing executives gathered in Palm Desert, California, for The MFG Meeting, a four-day event that emphasized emerging developments and business forecasts for American manufacturing.
Organized by AMT – The Association For Manufacturing Technology and the National Tooling and Machining Association (NTMA), “The MFG Meeting is where builders, distributors, and end users converge to shape the future of manufacturing – an industry embracing change and critical to a healthy American economy,” says outgoing AMT Chairman Jerry Rex. “We continue to face difficult challenges from the skilled worker shortage to slower growth rates expected until the fourth quarter. During the meeting we explored solutions, shared experiences of effective practices, and made plans to advance the manufacturing technology industry.”
“Attendees came away with a deeper understanding of the connected factory, as well as inspiration and insight from leaders of the most innovative companies in the world today,” AMT President Douglas Woods notes.
The MFG Meeting included a Miles for Manufacturing (M4M) 5k Run/Walk benefiting the Max S. Hayes High School in Cleveland, Ohio, which offers customized learning programs including courses in CNC machining, CAD, and welding, along with courses in automotive repair and computer design. The top three M4M 5K finishers were Will Rassieur, Bob Bodde, and Lars Reich. The next M4M 5k will be held Sept. 19 at IMTS 2016 in Chicago, Illinois. www.themfgmeeting.com; www.amtonline.org; www.ntma.org

Airbus Group CEO joins Perlan 2 strato-glider team
Airbus Group CEO Tom Enders worked alongside the all-volunteer flight test team for Airbus Perlan Mission II as the program started pressurized flights. The Perlan 2 glider is designed to soar on wind currents to 90,000ft.
Enders received a detailed briefing on the custom-built glider and its systems from Airbus Perlan Mission II chief pilot Jim Payne in the program’s home hangar in Minden, Nevada. Perlan 2 relies on mountain waves – updrafts generated by winds crossing mountain ranges – to carry it aloft. To reach the record-breaking altitudes necessary for its research program, however, the team will deploy later this year to a region in Argentina where mountain waves fed by the polar vortex travel all the way to the stratosphere.
The test flight program took a significant leap forward with a successful flight validating the newly pressurized cockpit system that will allow pilots to operate safely without wearing the bulky pressure suits that hampered previous efforts to soar to the stratosphere in the unpressurized Perlan 1 glider. The crew of Perlan 2 breathes 100% oxygen from a rebreather system similar to what astronauts use in space.
“This aircraft will fly in a region of our atmosphere where no other aircraft has operated for sustained periods, and in doing so it will change our fundamental understanding of how our atmosphere works,” Enders says. “But we also hope it will change people’s thinking about what is possible, and inspire a new generation of aerospace pioneers to push beyond their limits.”
For Enders, part of the project’s appeal is aeronautics, but it’s also operating at the edge of space. “The only way to stay competitive at the edge of technology is to invest in innovation.” Enders adds.
The Perlan project is supported by Airbus Group and other sponsors that include Weather Extreme Ltd., United Technologies, and BRS Aerospace. www.perlanproject.org; www.airbusgroup.com/perlan
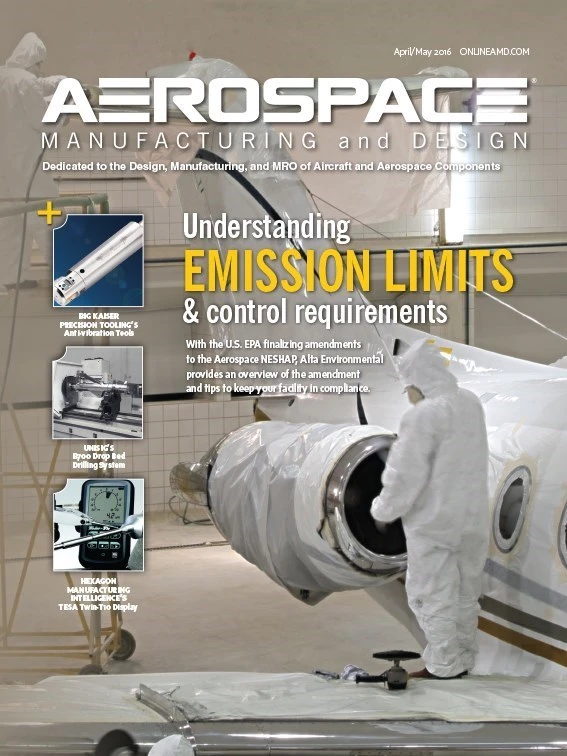
Explore the April May 2016 Issue
Check out more from this issue and find your next story to read.
Latest from Aerospace Manufacturing and Design
- 2024 Favorites: #10 Article – How 3D-printed aviation parts can accelerate return to air
- 2024 Favorites: #10 News – Boom Supersonic completes Overture Superfactory
- OMIC R&D hosts Supporting Women in Manufacturing Day 2024
- 4D Technology's AccuFiz SWIR interferometer
- Seventh Lockheed Martin-built GPS III satellite launches
- KYOCERA AVX's CR Series high-power chip resistor
- UT researchers receive Air Force grant for wind tunnel
- Monticont's linear voice coil servo motor