
Electric motors powerful enough to propel aircraft the size of a Boeing 737 as part of a hybrid propulsion system could revolutionize aviation fuel economy. NASA recently awarded grants to a group making motors 5x lighter and more efficient than any in production.
Dr. Codrin-Gruie (CG) Cantemir, a research scientist at The Ohio State University’s Center for Automotive Research, was awarded the grant for his 10MW Ring Motor concept that includes a tuned coil and variable-cross-section windings married to technology that achieves direct contact between coils and coolant. This enables stator magnetic field production at high frequencies while minimizing specific high frequency losses in solid conductors. The motor is an induction machine in reverse (an out-runner) where the field generated by the internal stator induces currents in a squirrel cage located in the rotor. This interaction produces torque and power without needing permanent magnets (PMs). NASA encouraged Cantemir to explore using induction motors rather than PM systems because they are safer and more robust.
In a preliminary test of a validation 1MW induction motor, Ohio State, in partnership with NASA, set two world records: one for absolute normalized continuous power density and the other for continuous power density for an induction motor.
The previous record for normalized continuous power density was set by Siemens of Germany at approximately 2.05W/kg*rpm and used rare-Earth neodymium magnets and expensive cobalt-based magnetic material. The 2.60W/kg*rpm record uses only off-the-shelf magnetic materials without PMs.
One unexpected reason for the record is the use of aluminum rather than copper as the conductor in the stator coils. Theoretical work conducted with the grant showed researchers that in certain situations, aluminum will behave better than copper.
“It may be counterintuitive, but a power-dense motor uses less material and less tooling versus conventional, hence the cost saving,” Cantemir says.
A 2.7MW motor is being developed to further validate the concept’s performance.
The Ohio State University Center for Automotive Research
https://car.osu.edu
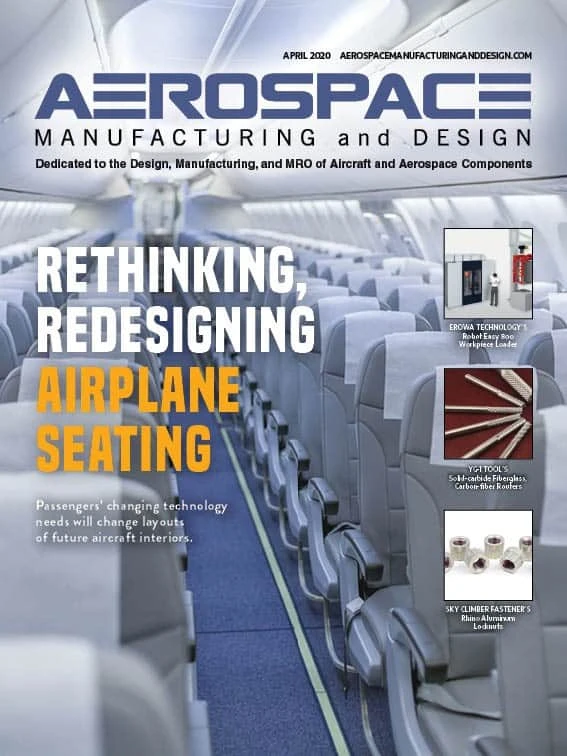
Explore the April 2020 Issue
Check out more from this issue and find your next story to read.
Latest from Aerospace Manufacturing and Design
- AAMI project call submission deadline extended to May 12
- Jergens launches cast iron tooling column additions
- Airbus to acquire assets relating to its aircraft production from Spirit AeroSystems
- FANUC America's Cobot and Go web tool
- Chicago Innovation Days 2025: Shaping the future of manufacturing
- High-density DC/DC converters for mission-critical applications
- #59 - Manufacturing Matters: Additive manufacturing trends, innovations
- ACE at 150: A legacy of innovation and industry leadership