
To make hydrogen-powered planes possible, engineers must develop the jet engines that will power them. Experiments by researchers at ETH Zurich are now providing the necessary basis for making these engines powerful and durable.
Europe is preparing for climate-neutral flight powered by sustainably produced hydrogen. In 2023, the EU launched a project to support industry and universities in developing a hydrogen-powered medium-haul aircraft. Among other things, jet engines will have to be adapted to run on the new fuel. Today’s engines are optimized for burning kerosene.
“Hydrogen burns much faster than kerosene, resulting in more compact flames, which must be taken into account when designing hydrogen engines,” explains Nicolas Noiray, professor in the Department of Mechanical and Process Engineering at ETH Zurich. Experiments by Noiray’s team now provide an important basis for this difference. The team’s results are published in the journal Combustion and Flame.
One problem is vibration, which engineers try to minimize. In typical jet engines, about 20 fuel injection nozzles are arranged around the annular combustion chamber of the engine. The turbulent combustion of the fuel there generates sound waves. These waves reflect from the chamber walls and have a feedback action on the flames. This coupling between the sound waves and flames can cause vibrations that induce a heavy load on the engine combustion chamber.
“These vibrations can fatigue the material, which in the worst case could lead to cracks and damage,” says Abel Faure-Beaulieu, a former postdoctoral researcher in Noiray’s group. “This is why, when new engines are being developed, care is taken to ensure that these vibrations don’t occur under operating conditions.”
An elaborate test and measurement facility at ETH Zurich allows Noiray to measure the acoustics of hydrogen flames and predict potential vibrations. As part of the EU HYdrogen DEmonstrator for Aviation (HYDEA) project in which he is involved, Noiray tests hydrogen injection nozzles produced by GE Aerospace.
“Our facility allows us to replicate the temperature and pressure conditions of an engine at cruising altitude,” Noiray explains. The ETH researchers can also recreate the acoustics of various combustion chambers, enabling a wide range of measurements. “Our study is the first of its kind to measure the acoustic behavior of hydrogen flames under real flight conditions.”
The researchers used a single nozzle and then modeled the acoustic behavior of the collection of nozzles as it would be arranged in a future hydrogen engine. The study is helping GE Aerospace engineers optimize the injection nozzles and pave the way for a high-performance hydrogen engine. In a few years, the engine should be ready for initial tests on the ground, and in the future, it could propel hydrogen fueled aircraft.
ETH Zurich
https://ethz.ch/en
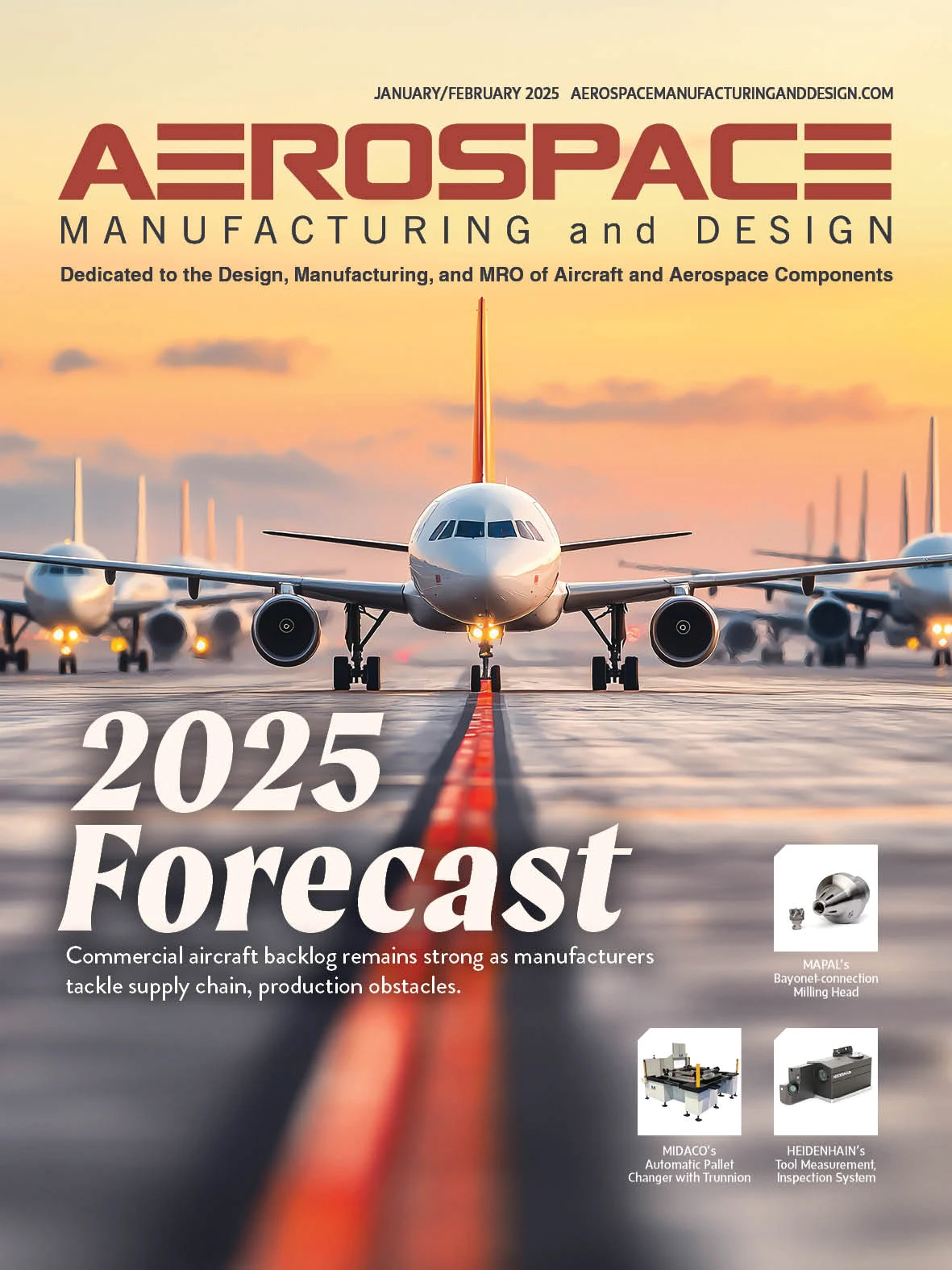
Explore the January/February 2025 Issue
Check out more from this issue and find your next story to read.
Latest from Aerospace Manufacturing and Design
- Piasecki acquires Kaman's KARGO UAV program
- PI Americas’ long-travel XY piezo nanopositioners-scanners
- AAMI project call submission deadline extended to May 12
- Jergens launches cast iron tooling column additions
- Airbus to acquire assets relating to its aircraft production from Spirit AeroSystems
- FANUC America's Cobot and Go web tool
- Chicago Innovation Days 2025: Shaping the future of manufacturing
- High-density DC/DC converters for mission-critical applications