

As the lead contractor for the European space launchers Ariane 5 and Ariane 6, ArianeGroup is responsible for the entire life cycle of a launcher – from design, to production, marketing, and operation – through its subsidiary, Arianespace.
Ottobrunn, near Munich, Germany, is home to the ArianeGroup Liquid Propulsion Centre, where components for engines for European Ariane launchers are developed and produced. The focus is currently on the thrust chambers for the Ariane 6 main-stage engine the Vulcain 2.1 and the new re-ignitable upper stage engine, Vinci.
“We have almost 300 employees here in Ottobrunn, around 100 of whom work in production,” says Stefan Winter, head of production at Ottobrunn. “The majority of our processes are carried out in our production center, from machining and welding (EB and TiG), to integration and quality testing. Electroplating and component cleaning take place in neighboring buildings. These short distances are a huge advantage.”
Ariane launchers achieve orbit with solid rocket boosters delivering a thrust of around 13,000kN and lift the 800-metric-ton rockets in the first two minutes after launch. The main stage with the Vulcain-2 engine provides further thrust until the rocket has reached a height of approximately 160km around nine minutes after launch. Then the upper stage takes over, powered by the Vinci engine in Ariane 6. Depending on the mission, this engine is operational for around 15 minutes to put the upper stage with the satellites into the correct orbit.
The thrust chamber – the heart of the Vinci engine – is manufactured in Ottobrunn.

Vinci works with cryogenic hydrogen and oxygen: “First, the hydrogen flows around the combustion chamber, cools it, and vaporizes. The gases produced drive fuel pumps and are injected into the combustion chamber with the oxygen and burned,” Winter explains. “Although the hydrogen is allowed through the cooling channels to cool the chamber, the clever design means it remains in the chamber for a long time, until it’s as hot as possible. We then use the expanding gas to drive the turbo pumps. This is the big advantage of the Vinci engine.”
M80 Millturn and the Vinci engine
Most of the engine parts from Ottobrunn are manufactured on a WFL M80 machine, including the engine’s combustion chamber base body. Two processes previously carried out on two machines are now done on one. Thanks to the M80 Millturn, both processes – turning the inner contour and milling the outer contour – are combined with stable clamping ensured. This is a huge advantage, especially for long, thin parts such as the Vinci combustion chamber. The zero-point clamping system also provides maximum flexibility in production.
A patented copper-silver-zirconium alloy characterised by high strength, exceptional heat transfer value, and excellent machinability is used for the Vinci engine’s base body. Due to the long, thin design, material properties are very important. The material is first cast in blocks and then forged into the desired shape. Ultrasound ensures quality before it’s released for production.
The main production steps for a Vinci combustion chamber blank are turning, milling, electroplating, welding, and finishing. Eighty percent of the workload is performed with the M80.
“We’re working with extremely expensive materials in accordance with the highest industrial standards and to the highest levels of quality. When a rocket is launched, there are no second chances, so we can’t make any mistakes,” Winter adds. “Quality-driven personnel are essential here and we have them.”

Why Millturn?
“When it comes to machining times, our investment in the WFL M80 Millturn/3000mm brought enormous added value,” Winter says.
The WFL replaced a 3-axis lathe and a 3-axis milling machine. A zero-point clamping system was implemented on the M80 so setup’s still very quick, reducing the lead time and wait times by at least 30%.
“One of the biggest advantages of the WFL machine is its large tool magazine. Because of the Inconel machining, we always have between four and six sister tools in use, so we need sufficient tool stations. This isn’t a problem thanks to the magazine’s modular concept. If we need even more tools, we can just buy another tool turret disc. In the past, three processes would require three NC programs or more. Now we only need to release and maintain one NC program for the same work. It also makes configuration management much easier, as there’s less data to manage. This was a big step forward,” Winter explains.
When asked why they opted for a Millturn and the M80 model, Winter responds: “Ultimately, the machine kinematics and references won us over. A quick supply of spare parts, components from renowned manufacturers, and proximity to the manufacturer were also important to us.”
The machine is equipped with a pick-up magazine and WFL system boring bar. “We worked with WFL and Sandvik to procure a special 1.4m-long boring bar so in future we can also machine the Vinci’s inner contour on the WFL,” Winter explains. “To turn the inner contour on the WFL, we also developed a new device.”

The machine also had to satisfy reliability and accuracy requirements. “It had to meet a tolerance of around 1/100 in the required working range. Temperature influences play a huge role here, so our production hall is also air-conditioned and regularly checked. The machine is also temperature-monitored,” Winter says.
Sealing surfaces are manufactured at ArianeGroup using the Utronix software cycle – the virtual U-axis. Circular surfaces are needed on certain workpieces, at every angle.
“At around 135°, we have to circular-machine a sealing surface of 28mm around a 20mm hole with a boring bar. This then becomes increasingly larger. So the Utronix cycle is often in use here and is very important,” Winter notes.
He also emphasises how the new machine is an advantage when the team was asked to manufacture a nozzle demonstrator. “The challenge was to manufacture a complex conical inner contour with cooling channels. Thanks to the machine’s stability, we completed the broaching process with a length of almost 500mm. The combination of stability, flexibility, and the required working area in the machine allows this kind of special machining.”
Innovative spirit

In addition to manufacturing Vinci parts, the production team also uses the Millturn to produce satellite parts, as well as in R&D and for jig construction.
“We’re currently working on components for the drive of the future – Prometheus for example,” Winter says.
The various versions of the Prometheus engine will be driven by liquid hydrogen and liquid oxygen or liquid oxygen and methane. These will be the first European engines with controlled combustion, enabling them to adapt to the launcher’s flight conditions during various mission phases. A digital system will provide control across a range from 30% to 100% maximum thrust. Prometheus will also be equipped with artificial intelligence (AI) and a health monitoring system for engine function diagnostics.
The family of Prometheus demonstrators also benefits heavily from the latest 3D-printing technology. Parts produced this way account for 70% of the total weight of the engine.
“The WFL is very well suited for all of these exciting future projects,” Winter adds.
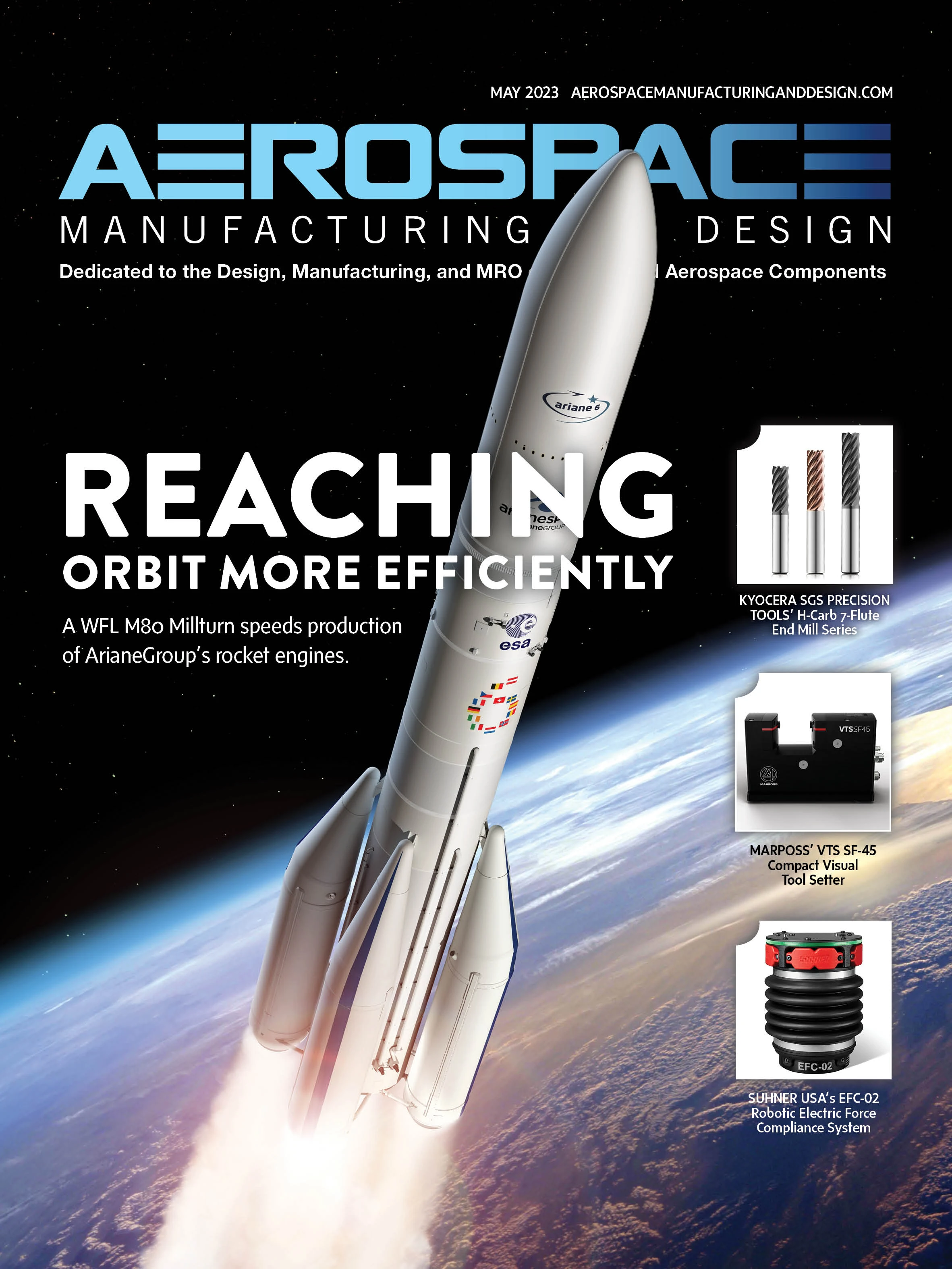
Explore the May 2023 Issue
Check out more from this issue and find your next story to read.
Latest from Aerospace Manufacturing and Design
- BOC Aviation orders 120 Airbus, Boeing jetliners
- Mazak’s INTEGREX j-Series NEO
- Embraer tests wing for new technologies demonstrator
- Mitutoyo America’s SJ-220 portable surface roughness tester
- #55 - Manufacturing Matters - A Primer on Defense Contract Manufacturing
- Registration is open for April’s Manufacturing Lunch + Learn!
- Natilus begins search for new home to build world's most efficient commercial aircraft
- Aerospace Industry Outlook webinar is back by popular demand