Students in America’s high school metalworking shop classes have been turning out some impressive projects using CAD/CAM software and CNC machine tools, but how many can boast, “Hey Uncle Phil, I made something that’s circling the Earth right now on the International Space Station!” Great impressions are what David Tuttle’s Precision Machining Technology classes at Platt Technical High School in Milford, Connecticut, make with the area’s manufacturing businesses. Department head Tuttle and his fellow instructor, Greg Amende, have made the program challenging and rewarding for more than 90 students each year who have chosen to become proficient in many facets of advanced manufacturing.

Students at Platt Tech, some 800 in all, begin their freshman year checking out the various programs available to them. They are assigned to a group of about 20 students and travel to each of 14 trade programs for a few days, then pick their favorite three and go back and audit them for five days each. By December, they have decided which path to follow for the rest of their high school experience.
Those who have chosen Precision Machining Technology have been auditing the senior class and have had a good look at the facilities that will be at their disposal. This includes a large machine shop with nearly 40 milling machines and lathes, as well as hand tools, measuring equipment, and a computer-aided design/computer-aided manufacturing (CAD/CAM) lab with 36 seats of Mastercam software programming the work for more than a dozen CNC machines and Dassault Systèmes’ SolidWorks for the design. Watching older students working in the lab, running the machines, and demonstrating the various aspects of the program helps.
“Most of the industries in our region concentrate on defense, aerospace, medical, and tooling,” Tuttle says. “They all call for automated, high-precision manufacturing capabilities and these are the companies that will be looking to hire our graduates. During the past few years, we have been concentrating less on manual operations and more on CNC machining. Our curriculum has advanced to the point where we have introduced 5-axis machining. Sixteen of our machines are now CNC and we have a good mix of machines from different manufacturers, so our students can get used to the different CNC controls they’ll find in
Four-year program
Freshmen spend the balance of their first year learning the fundamentals of machining and becoming familiar with the operation of basic manual machines.
“When they get into their second year,” Tuttle says, “they continue with manual work, but we start to mix it up a little by introducing them to CNC at the same time. We don’t give them anything in depth, but they’ll have a chance to run the machines and do a little basic programming in the lab. We use early CNC programming lessons as a tool to strengthen their ability to read blueprints. To write a program, they need to study the blueprint in depth. Mastercam is also used for
In their junior year, students get into setup and in-depth operation of the CNC machines.

“They will also move on to full Mastercam toolpath programming applications,” Tuttle explains. “They will be provided with a blueprint that they will have to hand program with G-code while they are learning Mastercam. I don’t just teach the kids Mastercam without having them understand what goes into the program because every one of our local manufacturers told me they need people who can also read and understand G-code programming. When Mastercam posts a program and the programmers don’t know how to read it, they won’t understand what’s going to happen. Our students aren’t just learning Mastercam software, they’re learning to read the code selected by Mastercam.”
In addition to learning setup operations for various fixtures to hold their work on the machines, juniors are taught multi-part production by making 20 or 30 identical parts, as well as making a one-of-a-kind specialty item that involves 4- or 5-axis work.

“In their senior year, they are getting into advanced operations such as complex multi-tool jobs where they may have to set up 10 tools on a machine and do extensive programming operations in Mastercam that would require many tools for turning and milling,” Tuttle says. “Employers have been asking us for graduates who can walk up to a machine and set it up from scratch. That includes developing, designing, and making special tooling and fixtures to hold the parts. It’s not just making a part, it’s also coming up with the process and method for holding the component in various ways, other than just a simple vise.”
Tuttle receives a lot of input from local employers. “I communicate with them on a regular basis. I visit their companies, look at what they’re doing, and get ideas from them and they tell me what our graduates should know. Then we design projects specifically to develop those skills the employers are asking for. Who better for us, as teachers, to talk to than the people our graduates go to work for?”
About 50 members comprise Tuttle’s industrial advisors, the Technology Trade Advisory Committee (TTAC).
“As many as 40 of them come to the school twice a year,” Tuttle says. “Many of the students attend the meetings and have an opportunity to network with these future employers.”
Tuttle’s relationships with outside sources and manufacturers have resulted in a wide range of components for his students to program and machine.
“We’re permitted to take in this work as it offers opportunities for learning operations beyond standard pieces in the curriculum. Sometimes we take in projects that are joint ventures between our shop and another tech discipline’s shop, such as the engineering design program and mechatronics within this school, to produce products that teach the importance of communication within different manufacturing disciplines,” Tuttle says.

NASA’s HUNCH
One of the school’s vendors saw a story about NASA working with high school students and thought Tuttle might be interested in NASA’s High Schools United with NASA to Create Hardware (HUNCH) program. Tuttle sent an email to NASA expressing interest. Soon, representatives from NASA visited Platt Tech and were impressed with the shop’s facilities. NASA shipped a 3,000 lb supply of aluminum to Platt Tech to get them started with the HUNCH program.
“We make several of the larger parts that come together to fabricate storage lockers on the International Space Station that are used by the astronauts for a variety of experiments,” Tuttle says. “They look a lot like aluminum suitcases. The largest part starts out as a billet weighing about 60 lb. After CNC machining, the final piece weighs about 18oz. The smaller parts for the final assembly are made at other schools in the HUNCH program. Our students program all the
Whether it will be reaching out to space, or reaching for a nice paycheck, students graduating from the Precision Machining Technology program at Platt Technical High School are in the right orbit for success.
Mastercam (CNC Software Inc.)www.mastercam.com
Mitutoyo America Corp.
www.mitutoyo.com
NASA HUNCH program
https://nasahunch.com
Platt Technical High School
https://platt.cttech.org
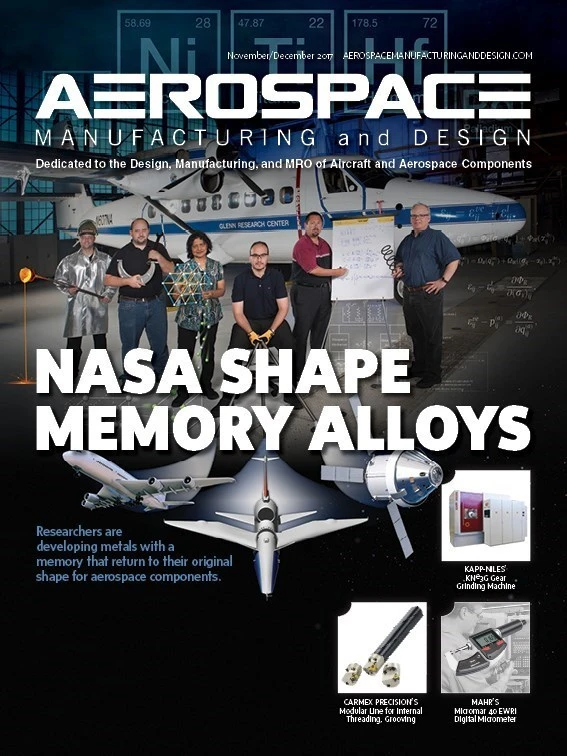
Explore the November December 2017 Issue
Check out more from this issue and find your next story to read.
Latest from Aerospace Manufacturing and Design
- AAMI project call submission deadline extended to May 12
- Jergens launches cast iron tooling column additions
- Airbus to acquire assets relating to its aircraft production from Spirit AeroSystems
- FANUC America's Cobot and Go web tool
- Chicago Innovation Days 2025: Shaping the future of manufacturing
- High-density DC/DC converters for mission-critical applications
- #59 - Manufacturing Matters: Additive manufacturing trends, innovations
- ACE at 150: A legacy of innovation and industry leadership