
CFM International – a joint-venture of GE Aviation and Safran – is ramping up production of the LEAP aero engine for use on fleets of single-aisle Airbus A320neo, Boeing 737 MAX, and Comac C919 jetliners. LEAP engines offer greater fuel efficiency and a lower cost to maintain, and CFM has logged nearly 3,000 engine orders. It plans to double LEAP production in 2018 to approximately 1,100 to 1,200 engines as part of a ramp-up that will lead to more than 2,000 LEAP engines per year by 2020.
To meet this demand, French company Safran Aircraft Engines uses a multiple-sourcing strategy and contracts production of low-pressure turbine (LPT) blades to its supply chain. One of the sources is in France, the other in Japan.
“It is unusual for small-to-medium enterprises in Japan to win mass-production contracts directly from global original equipment manufacturers (OEMs) within the aircraft-engine industry,” says Jun Morinishi, president
Created
AeroEdge’s core competency in processing difficult materials – titanium-aluminum and Inconel alloys – made it a suitable fit for manufacturing LPTs. Each variant of LEAP engine has a different profile for its LPT blades, complicating production.
To secure the business of making LPT blades for Airbus and Boeing LEAP engines, AeroEdge prepared a new factory site at Ashikaga, Japan, north of Tokyo. Built in less than a year, the 51,560ft2 facility was ready for production with machines installed by December 2016.
To mill the LPT blades, AeroEdge needed a machine with a spindle capable of high-acceleration/deceleration and able to efficiently handle small workpieces. The company chose Mitsui Seiki’s Vertex 55XII 5-axis vertical machining centers, fitted with a strengthened spindle motor and modified axis parameters.
Small but mighty
Despite its small size – 72
Mizuta, who spent two years in the United States, first at Cornell University to study at the carbon fiber science lab and then at Duke University for management studies, guides AeroEdge’s strategic innovation.
“All processes AeroEdge undertakes on LEAP engines are difficult, including grinding and polishing,” Mizuta explains. Making LPTs begins with examining how the alloy’s contents can affect quality.
“It’s important to keep watching materials and their data
Materials are not the only part of the process. Machining is considered just as carefully. The combination of machine design and materials – “all must be optimized,” Mizuta says. “We have to find a robust set of parameters to avoid unacceptable defects.”
Working well with a partner is essential to the company’s philosophy. AeroEdge is still investing to meet LEAP engine demand, and it carefully evaluates the advantages of a range of production tools to optimize its processes – from cutting to inspection.
Morinishi says the accuracy that Mitsui Seiki machining centers offered was a principal reason for choosing them as the primary machine tools for LPT production.


“Mitsui Seiki listened to our customer voice in a strategic collaboration to develop machines together that
Compact, the Vertex is a cube-on-cube design with a heavy base. The factory has
Managing coolant and chips was important to maximize the LPT production rate, so AeroEdge specialists worked closely with
Future investments
Although not suitable for manufacturing LPTs, AeroEdge engineers are looking into additive manufacturing for other applications, such as using
“Customized machines always challenge machine makers to work with us,” Mizuta says. “If no machine is available, we can help design it.”

Mizuta also is eyeing other technologies to bring into AeroEdge. “Industrial Internet of Things (IIoT), visualization,
Another project he’s working on is software to automate part inspection using artificial intelligence (AI).
AeroEdge is seeking to broaden its LPT blade manufacturing expertise in automotive, medical, and energy industries as well as aerospace, domestically and internationally. It has moved rapidly to capture a key business, but its managers know they can’t rest on their accomplishments thus far.
“To survive in the aviation industry, we must incorporate the latest technology and continue to win the price advantage and quality competition worldwide,” Morinishi says.
AeroEdge has put in place strong groundwork to ensure it can compete.
AeroEdge Co. Ltd. CFM International Mitsui Seiki USA Inc.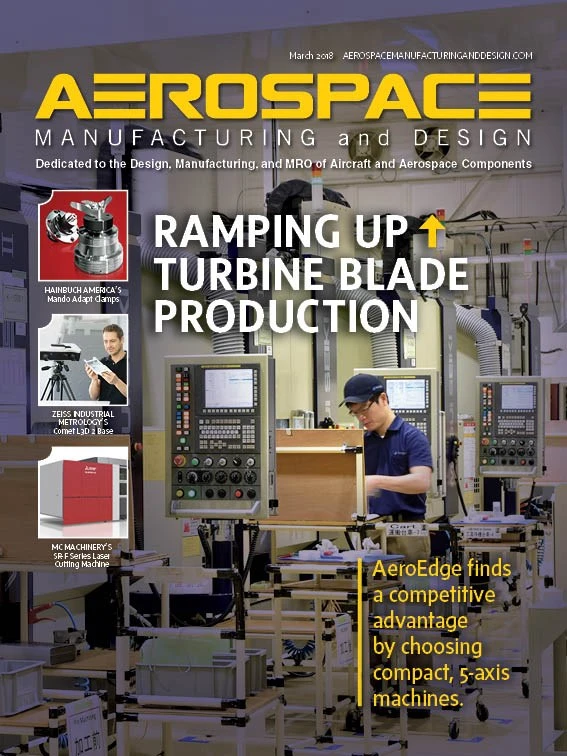
Explore the March 2018 Issue
Check out more from this issue and find your next story to read.
Latest from Aerospace Manufacturing and Design
- AIX shows aircraft interiors are a strategic priority for global airlines
- Machine Tool Builders Roundtable: Turn equipment into expertise
- No time to waste: How to machine MedTech parts more efficiently
- The 5 Best and Fastest Spindle Repair Services
- Mill smarter, not harder: How collaboration optimizes production
- Be proactive – stay ahead of tariffs and other economic and supply chain curveballs!
- Taiwan’s China Airlines orders Boeing 777X passenger, freighter jets
- Reamer re-tipping extends life of legacy tooling