
Segen Quick Change sockets complement existing series of knobs and cylinders to speed setup. The sockets, available in three sizes, work with standard Segen knob sizes including the PD250 micro, the 375 mini, and the 438. These sockets mate with standard 3/8" socket drives; no special tooling is required.
The Quick Change system replaces nuts, bolts, fasteners, and hand tools, to reduce the time spent on industrial setups, changeovers, workholding, toolholding, clamping, fixturing, and alignment. They are well-suited to thermoforming and injection mold tooling, robotic fixturing and end-of-arm tooling, CNC machining, and ultrasonic welding fixtures.
Tooling Tech GroupFull grip jaws

With maximum contact area for a solid gripping surface, full grip jaws provide more friction for drive with reduced part distortion. A comprehensive lineup of full grip jaws in standard and custom configurations suit varied workholding applications. Manufactured from 6061 aluminum, 1018 steel, cast iron, and brass, full grip jaws won’t mark or mar workpiece surfaces. Standard sizes available to 32" in diameter. Custom designs are available with special heights, diameters, materials, and configuration to securely grip a workpiece, including a matching serration location perpendicular to the slots. Full grip jaws can reduce and simplify setup times. Full-grip chuck jaws, made in the U.S., are for high-speed machining as well as precision boring, tapping, drilling, and finishing.
The wrap-around top jaws distribute more of the gripping pressure across the workpiece, reducing part distortion. Standard and custom full-grip jaws are available in serrated, tongue and groove serrated, Acme serrated, and square serrated designs.
Modular grinding machines

Platform 3 modular grinding machines were developed based on the latest market requirements: small lot sizes and increasing part variety, combining the need for flexibility with a high-performance grinding machine.
The JUNICOR covers conventional corundum grinding requirements. High-speed grinding machines, such as the JUMAT, JUCAM, QUICKPOINT, and JUCRANK offer CBN and diamond grinding wheels. Flexibility and precision keep the balance, and the high-performance grinding machines are suitable for producing individual parts in small batches and larger workpiece series. Objectives are increased flexibility and cost-effectiveness by optimizing a modular system. Customers will benefit from shorter lead times achieved from quicker production throughputs, an advantage of the modular system that includes a uniform basis for all models of Platform 3.
The basic machine can be configured with options such as individual table assemblies and grinding spindle heads. The configurations range from standard to custom-made solutions to achieve the best efficiency, flexibility, and economic results. Platform 3 is versatile and suited to the needs of small or large series production at tier suppliers or one-piece requirements in a research and development (R&D) environment. Depending on accuracy, customers can choose between different guiding and driving systems on the X- and Z-axis.
Another highlight of Platform 3 is integrated automation, with the machine loaded manually or automatically. The internal gantry loading system can quickly adapt to new workpiece configurations, ensuring smooth workpiece handling. The system offers access to all components outside and inside the machine, combined with optimized setup capability. The machine allows individual grinding tasks due to various wheel-head variants, with or without an automatically swiveling B-axis. Up to 3 grinding spindles can be mounted on one single wheel head.
The Platform 3 enables cylindrical, non/cylindrical grinding for O.D. and I.D. applications, plunge and angular plunge grinding, more complex operations such as profile, face, surface, and groove grinding, as well as the Junker QUICKPOINT grinding/peel grinding process.
Milling inserts

The MA90 milling series features 4-edge tangentially mounted inserts, ensuring body rigidity, superior chip evacuation, enhanced tool life, and excellent surface finishes.
Available in inch and metric end mill, face mill, and modular head sizes, the MA90 gives customers additional benefits compared to conventional cutters. MA90 mills are designed with rigidity and ease-of-use in mind. Due to its design with tangentially mounted inserts where the insert screws are on the side, cutting forces are directed into the insert pocket corner. On conventional mills where the screw is on the front, cutting forces directed over the edge of the insert can build tension on the screw. The tangential design also allows for more teeth per diameter, better chip evacuation, and larger web thickness giving significant rigidity to the body.
PR18 series insert grades incorporate MEGACOAT NANO EX coating technology, delivering strong wear resistance and durability. By using a double lamination technique with special nano multi-layers for abrasion, wear, and heat resistance, this coating surpasses conventional grades, delivering excellent performance and extending the lifespan of the tools.
Solid carbide reamers

Solid carbide reamers enhance chip control with a through-coolant outlet for optimal chip evacuation, eliminating scrapped parts, jamming, and edge damage to increase safety, part quality, and tool life.
On blind and through bores, solid carbide reamers extend the performance of Nanofix products with through-coolant outlets that stop chip jamming and enhance application stability. The tool design delivers a powerful, precise stream of lubrication directly to the cut zone for optimal chip evacuation and tool life. Along with production stability, shops can rely on solid carbide reamers to maintain cutting speeds and part quality.
The range of multi-flute reamers comes in eight grades and more than 10 geometries, along with custom sizes and tolerances. The tools work with any precision toolholder, holding tolerances from 10μm to 15μm (0.0004" to 0.0006") and surface finishes from Ra 0.2μm to Ra 1.2μm (Ra 8μ" to Ra 50μ").
Solid carbide reamers are available in stock and custom diameters down to 1.461mm (0.057"). Through the online MyDesign tool configurator, shops can obtain customized tools.
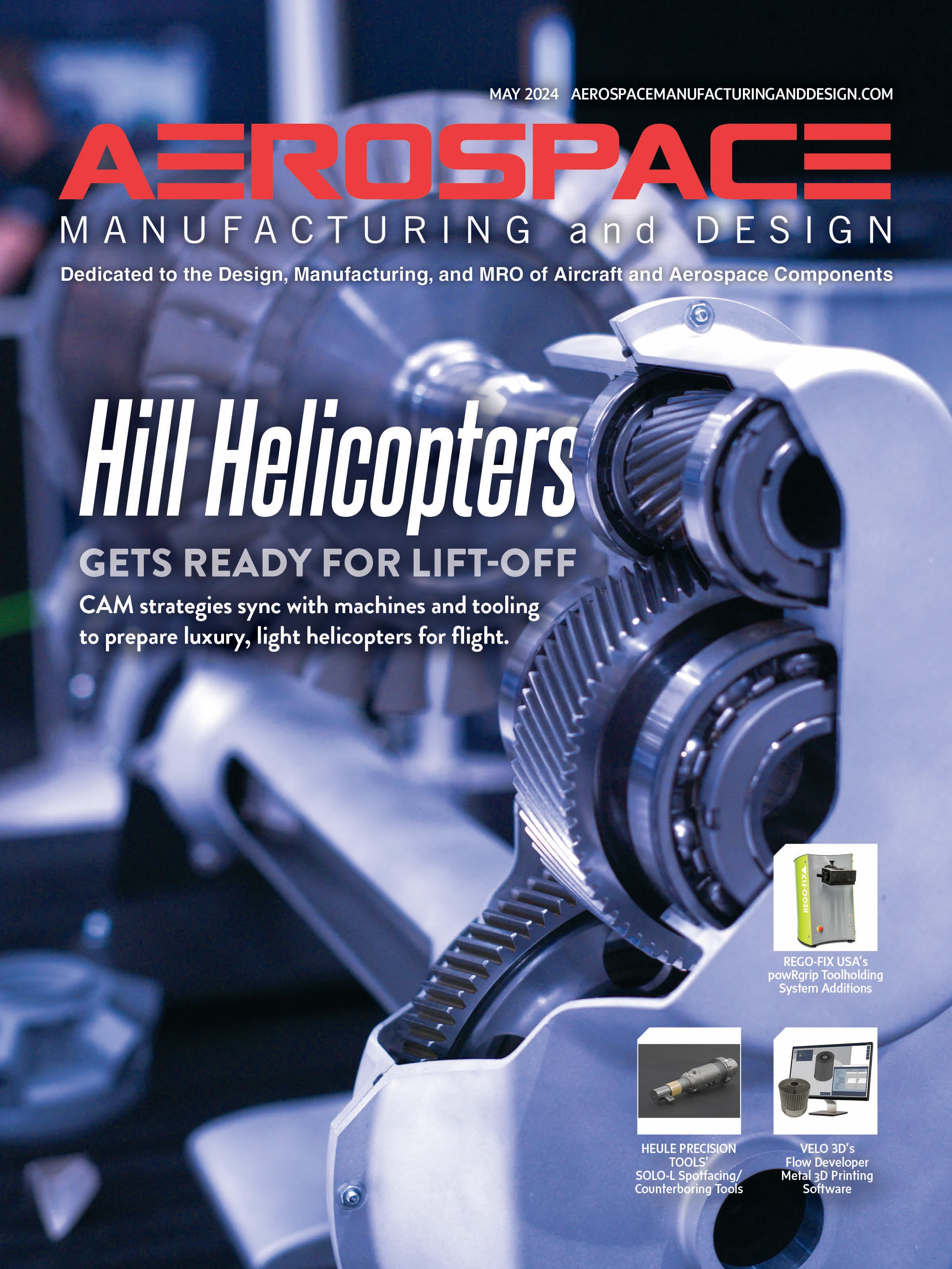
Explore the May 2024 Issue
Check out more from this issue and find your next story to read.
Latest from Aerospace Manufacturing and Design
- Extraordinary Starts Where Limits End | Okuma
- Satair, Champion Aerospace sign multi-year distribution agreement
- EMUGE-FRANKEN USA expands N. American solid carbide drill program
- AURA AERO unveils INTEGRAL R to the US market
- Creform Tite-Space AGV fleet
- Cyient Group, Deutsche Aircraft finalize multi-year contract
- High surface quality at high speed
- #57 - Manufacturing Matters - Agile & Robust Supply Chain Management with Lisa Anderson