
From the early 20th century through the post-World War II period, Long Island, New York, was a center of aircraft manufacturing. Builders including Grumman, Republic, Curtiss, Fairchild, and Sikorsky operated plants that turned out combat and commercial aircraft. While major manufacturers have relocated or been acquired by other companies, one job shop associated with their history combines past experience and the latest technologies to meet some of the most difficult applications for an international customer base.
Founded in 1960 as a screw machine shop, family-owned Alro Machine Co. Inc., of Lindenhurst, Long Island has evolved, now supplying parts and services for fixed- and rotary-wing aircraft. Ultimately, a strategic decision was made to concentrate on the machining and assembly of close-tolerance aerospace components and complex parts requiring hard machining, including tungsten, titanium, and high-temperature steel alloys.
Alro President Steve Young explains, “Although we’re a relatively small shop – we have just 14 people – we’ve invested in an extended capacity that enables us to machine large and small parts. Our work includes landing gear components and structural products. All our tolerances are under 0.001" and some parts require a 2µm finish. Our customers have worked with us for years and know that we can deliver. We’ve made parts for the F-35, C-130, B-1B, and 767, among many others, and we’ve invested heavily to meet our customers’ needs.”
Among the significant investments Alro has made are two high-capacity Niles- Simmons lathes with mill-turn capability. The most recent purchase is a pre-owned N30MC, a double machining head design based on two 5-axis turning-boring-milling units and equipped with a counter spindle with pick-up function. A similar machine, in use at a leading jet engine manufacturer, allows complete machining of turbine discs within two clamping operations simultaneously in a single machine. When purchased, the N30MC was equipped with a Hainbuch centroteX system. Developed for high-precision workholding of large rotational parts, the centroteX is also a quick-changeover clamping system.

Hainbuch America Corp. Northeast Regional Sales Manager Brian Eaton, says, “centroteX uses a machine adaptor plate equipped with bayonet coupling receptors that are fitted to the lathe. The plate accommodates clamping device adaptors in various sizes to easily fit into the coupling which are further strengthened by quick-tightening rapid-action screws. Alro’s system includes 100mm Spanntop collet chucks, Mando T812 ID gripping mandrels for ID work, and a 3-jaw chuck mounted to the interface plates. Changeover time is 10 minutes or less. Changeover accuracy is <0.002mm (2µm).”
Because of the sizes of the components involved, the centroteX system includes a Monteq mounting aid for larger and heavier clamping devices. An arc-shaped holder, suspended from a spring-mounted attachment, is equipped with quick-action bolts. The operator can quickly and easily secure a chuck or other clamping device for installation or removal. A specially designed roller cart provides clean, orderly, and secure storage for the clamping devices.

“When we first purchased the Niles- Simmons machine, we were unsure of how the Hainbuch system worked and why it had been installed,” Young says. “Once we learned about the quick-change capability, we were extremely happy to have it. Although large engine manufacturers might use a machine like this for long production runs, in our business, medium to short runs have become the norm, and the faster we can change over between parts, the more productive we become.”
As an example, Young cites two parts machined on the N30MC:
- 15-5PH stainless steel expansion arbor - Operations performed: milling, turning, boring; cycle time: 20 minutes to 4 hours, depending on job’s complexity
- 4340 steel chucking operation - Operations: milling, turning, boring, with similar cycle times; approximate changeover time between operations: no more than 10 minutes between chuck, collet/arbors
Eaton adds, “Steve and the team at Alro were quick to realize the potential that the Hainbuch centroteX system offers, both in terms of maintaining repeatability in hard machining operations and time savings in quick changeover. While our standard clamping devices excel in most operations, our engineering group is always ready to work with customers like Alro on the development of special customized sizes and designs for unique applications. Alro’s forward-looking attitude keeps the company ready to meet new challenges in the ever-changing aerospace industry.”
Young says, “The fascinating thing about what we do is the fact that we are at the forefront of manufacturing technologies. Methods and materials that start in aviation and aerospace find their way into other industries in time, and at Alro, we are proud to say, ‘We did it first.’”
Get curated news on YOUR industry.
Enter your email to receive our newsletters.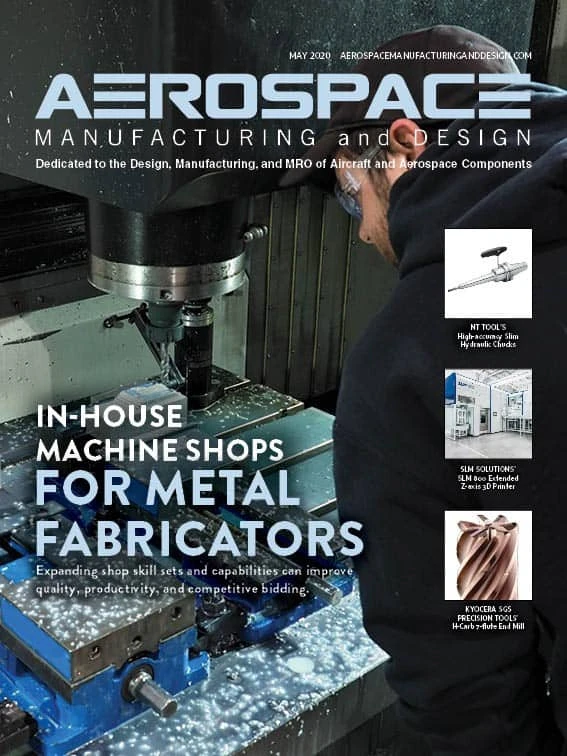
Explore the May 2020 Issue
Check out more from this issue and find your next story to read.
Latest from Aerospace Manufacturing and Design
- Ralliant to establish global headquarters in North Carolina
- Philatron MIL-DTL-3432 military cables
- Beyond Aero refines its hydrogen-electric light jet
- Americase's advanced protective solutions
- Social media - what are your thoughts
- GE Aerospace secures Air Force engine contract
- Thomson Industries' online sizing and selection tool
- #53 - Manufacturing Matters - 2024 Leaders in Manufacturing Roundtable