
GIE Media
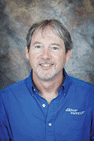
Is Independent G-Code Verification necessary? It is if you want to stay in business!
1) My CAM system already has machine simulation. What does VERICUT do that my CAM system doesn’t?
Unlike most CAM systems, VERICUT processes true G-code rather than internal CAD/CAM cutter location (CL) data. The same post-processed code loaded into your machine drives the VERICUT simulation. This becomes extremely valuable, especially when commanding working plane shifts, using multiple work offsets, working with subroutine calls, or validating rotary behaviors. These are just a few examples where CL data will not show the true picture.
VERICUT produces a feature-rich solid model called a Cut Stock used for collision checking and material removal, and its features can be directly interrogated for historical data related to associated tool paths.
2) How can VERICUT improve CNC programs?
VERICUT’s flexibility allows for custom control configuration to parse almost any G-code. This enables detailed syntax checking of program files and subroutines before simulation. Users can import a model of the finished part and have AUTO-DIFF automatically compare it to VERICUT’s Cut Stock model to clearly see any differences. The Cut Stock model’s accuracy can produce optimized code using VERICUT’s optimization modules. The high level of program validation allows users to eliminate prove-outs on the shop floor. By using VERICUT’s full capabilities, customers can ensure design intent, reduce cycle times, save on cutter costs, protect their machines, and feel confident in the entire process.
3) Can VERICUT simulate complex subroutines and branching logic?
Yes, VERICUT can initiate and update user and system variables just like the real machine. This allows VERICUT to properly navigate through complex branching logic and subroutines for virtually any control, including but not limited to Siemens, Fanuc, Okuma, OSP, and Heidenhain.
4) Can VERICUT simulate complex tool attachments, pallet changing, and head changing?
VERICUT allows for almost any type of attachment configuration including auxiliary rotary axis, angle heads, broaching tools, flash tooling, and bottle boring or facing heads that contain a secondary axis and allow for turn-milling operations. Spindle attachments can be loaded onto the machine using automatic M-code commands or through command comments in the NC program.
Part loading and pallet changing are supported using additional kinematics for the linear and rotary axes. Additive and hybrid manufacturing as well as composite fiber placement processes are also supported.

5) What kind of support can we expect from CGTech?
CGTech offers standard training classes for verification, machine/control building, and optimization. Customized training or services are also available and can be conducted virtually, on-site, or at a nearby authorized CGTech training facility. We can also come to your facility to review your process and identify how we can better help you do what you do best!
For more info: https://www.cgtech.com
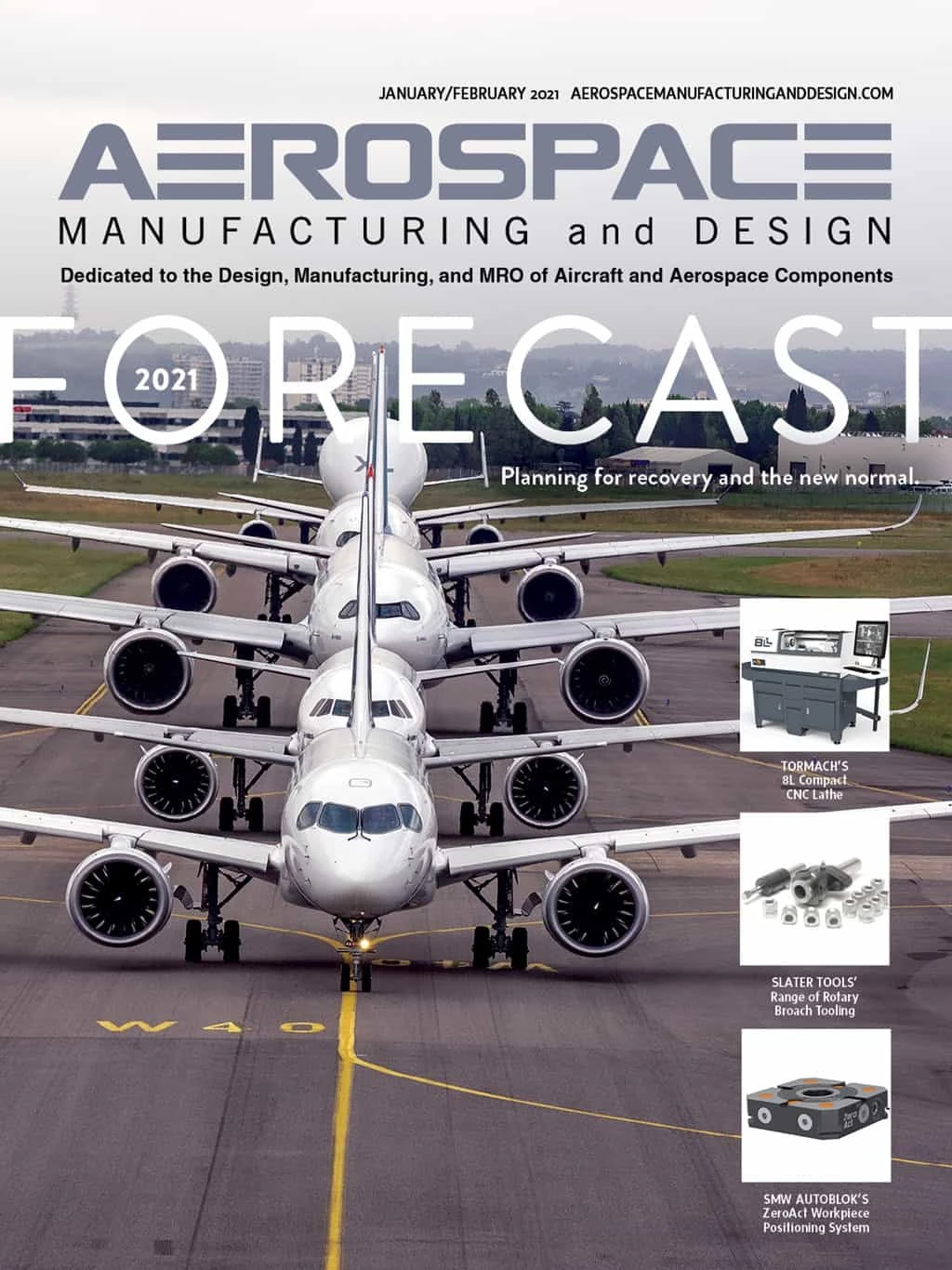
Explore the January February 2021 Issue
Check out more from this issue and find your next story to read.
Latest from Aerospace Manufacturing and Design
- AAMI project call submission deadline extended to May 12
- Jergens launches cast iron tooling column additions
- Airbus to acquire assets relating to its aircraft production from Spirit AeroSystems
- FANUC America's Cobot and Go web tool
- Chicago Innovation Days 2025: Shaping the future of manufacturing
- High-density DC/DC converters for mission-critical applications
- #59 - Manufacturing Matters: Additive manufacturing trends, innovations
- ACE at 150: A legacy of innovation and industry leadership