
GIE Media

1) How have wire EDM machines evolved and how has the technology improved?
Traditionally, many manufacturers viewed EDM as a niche industry. For decades, machinists considered EDM a necessary evil. With cutting speeds much slower than milling or turning machines, around 2 square inches per hour, nobody was using an EDM machine except for cutting steel or aluminum.
Modern wire EDM machines have made vast technological improvements. Cutting speeds exceed 32 square inches per hour, and with core stitch and automatic wire feeding, EDM machines can go head-to-head with mills and lathes in specific applications.
Wire EDM machines are getting even better at what they were designed to do – removing precise amounts of material with surgical precision.
2) What are the benefits of using a wire EDM machine in aerospace component manufacturing?
EDM machines can cut through various tough metals, from high-strength nickel alloys to titanium. Moreover, they can machine intricate paths with virtually zero recast layers. These two attributes make them perfect for any aerospace manufacturer.
FANUC wire EDM machines are ideal for cutting complex shapes or patterns commonly required in aerospace manufacturing, and they’re versatile. Since the wire and the workpiece don’t make physical contact, it’s easy to transition from machining tough-to-cut metals to delicate composites.
3) How can wire EDM machining effectively manufacture components for the aerospace industry?
The advent of AC power supplies changed how wire EDM machines operate and what materials they could cut. These newer FANUC power supplies reduce or eliminate metal deformations and the part’s heat-affected zone, making it a practical choice for aerospace manufacturing. By cutting with AC, heat is reduced and transferred away from the workpiece.
4) How can someone get the most out of their wire EDM machine?
No two operations are exactly alike. It’s essential to work with your machine tool supplier to determine which system best fits your shop. Having those in-depth discussions and exploring your machining opportunities is a critical step of any manufacturing process, laying the foundation for your organization. Shop owners must discuss some details with their supplier: wire diameter, part tolerances, machine options, floor space, part size, etc.
Once you have a good idea of what machine will work for you, consider automation as a next step – a host of standard and custom automation cells can maximize throughput. It’s the most straightforward way to get the most out of your machine. Whether you’re looking to decrease cycle time or run your wire EDM machine lights-out during off-hours, automation can open a world of opportunities.
5) What are some ways to reduce long cycle times commonly associated with wire EDM machining?
The best ways to improve cycle times are larger wire diameters, specialty coated wires, and occasionally stacking parts to produce more parts per cycle. By using a larger wire, more current can be applied for faster cutting. When you pair a large diameter wire with a coated wire, you can further increase cycle time. There are many types of coated wires, ranging from zinc to gamma-phase designed to pull cutting process heat away from the wire’s core, helping eliminate wire breaks.
For more information: https://www.methodsmachine.com
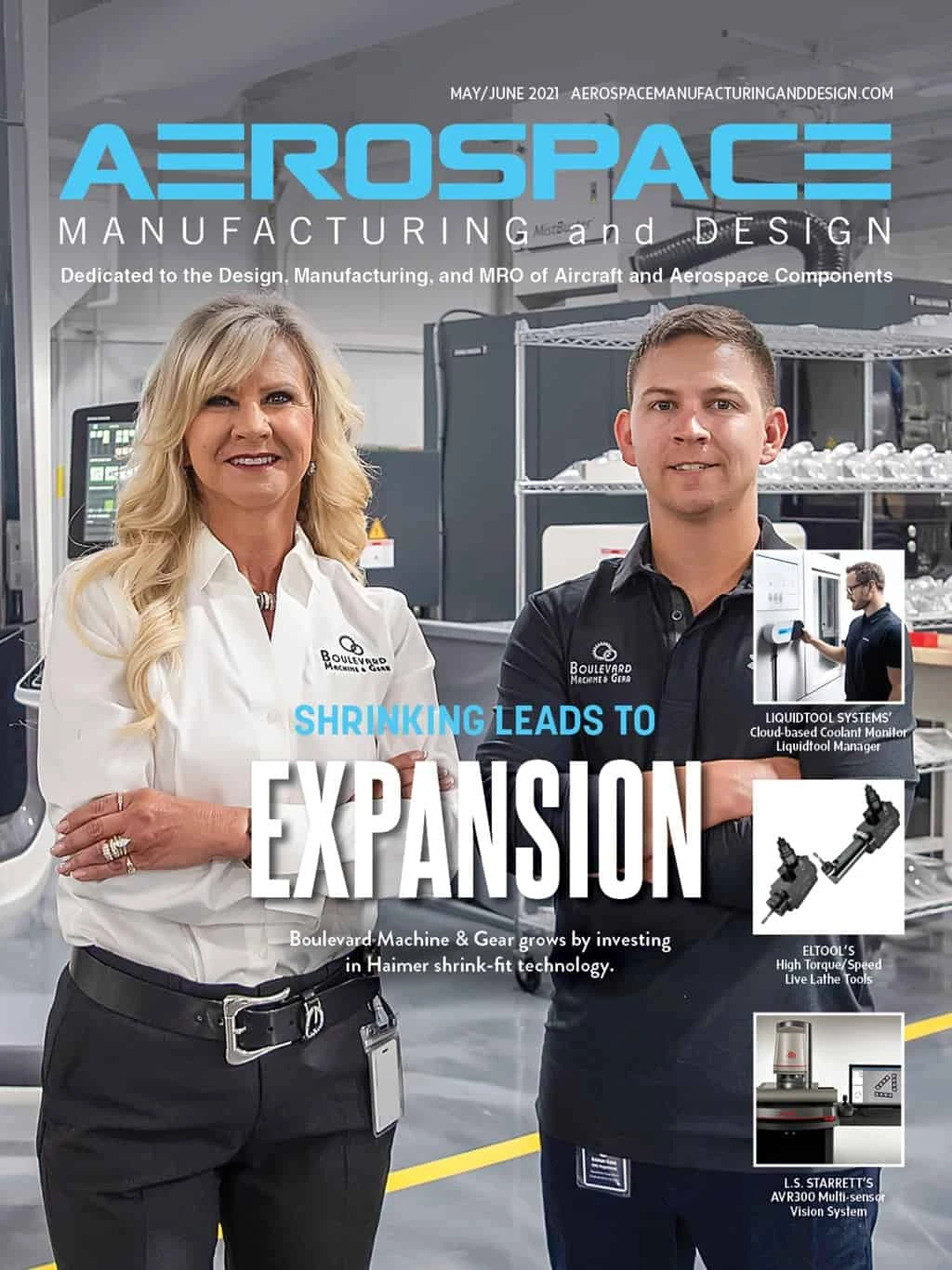
Explore the May June 2021 Issue
Check out more from this issue and find your next story to read.
Latest from Aerospace Manufacturing and Design
- Archer unveils vision for New York air taxi network
- Siemens launches its machine tool digitalization software portfolio MACHINUM in the US
- #58 - Manufacturing Matters - 2024 Metrology's Latest Advancements with Starrett
- Strategies to improve milling and turning for medical components
- Being proactive about your business despite uncertainty
- Optimizing production of high-precision components through collaboration
- An inside look at the defense maritime industrial base
- Safran inaugurates advanced manufacturing and engineering hub