
GIE Media

1) What’s new in ISCAR’s World of Turning products for aerospace materials/applications?
ISCAR’s new ceramic grades, IS35 and IS25, are proving very successful in many of the difficult-to-machine materials found in aerospace turning applications. JETCUT tooling (JHP tooling), is another area of continuous improvement for ISCAR. For finishing applications, a new chipformer (F3S), along with a new carbide grade (IC804) has been introduced, providing enhanced chip control and more wear resistance. Finally, all companies involved in turning should be aware of the innovative LOGIQ4TURN tool family.

2) What’s different about the JHP designs and what are the benefits?
High-temp materials used in jet engines are designed to withstand heat and require extreme machining temperatures to plasticize the material when creating a chip (i.e., chip control).
ISCAR’s new JHP turning tools can deliver high-pressure coolant at precise locations in the cutting zone, elevating cutting parameters, improving tool life, and managing chips.
3) What latest grades from ISCAR benefit typical aerospace materials/applications?
High-temp materials most often need to be machined at lower surface speeds and feed rates when using typical carbide inserts. ISCAR’s new IS35 and IS25 ceramic grades are silicon nitride-based ceramics (SiAlON) combined with aluminum, oxygen, and nitrogen. These SiAlON ceramics offer excellent heat resistance and mechanical strength in machining aerospace materials, enabling much higher material removal rates in roughing operations.
4) Insert geometry design is important to performance. What new product designs can benefit aerospace companies?
In most aerospace applications, dimensional tolerances are extremely small, so in finish turning, heat or stress can’t be introduced as this would cause the material to move or distort. Some companies use carbide inserts in finish-turning at lower speeds and ISCAR has developed the new F3S chipformer in carbide grade IC804. This chipformer maintains controllable chip formation, even at smaller finishing depths of cut. The hard titanium aluminum nitride coating of the IC804 carbide grade makes a great combination for finish-turning aerospace materials.
5) How does adopting these new cutting tool technologies positively impact productivity?

ISCAR’s mantra is “Where Innovation Never Stops” and this plays out in a recently introduced turning line/insert that is very innovative and different. The LOGIQ4TURN product line includes a new insert (CXMG) capable of outperforming traditional turning tools, such as those using CNMG inserts. The neutral or negative inclination of traditional turning tools and corresponding insert geometries, such as the CNMG, can introduce unwanted stress and pressure in turning applications. ISCAR’s CXMG is a free cutting, positively positioned insert with 4 cutting edges. Another feature of the LOGIQ4TURN insert is a dovetail clamping mechanism that securely and accurately holds the insert in the pocket. This allows the positive CXMG insert to achieve feed rates and depths of cut typically only achieved by negative (stronger) inserts. Innovative insert design with new grades and chip formers proves extremely successful for turning materials used in producing aerospace components.
For more information: https://www.iscarusa.com
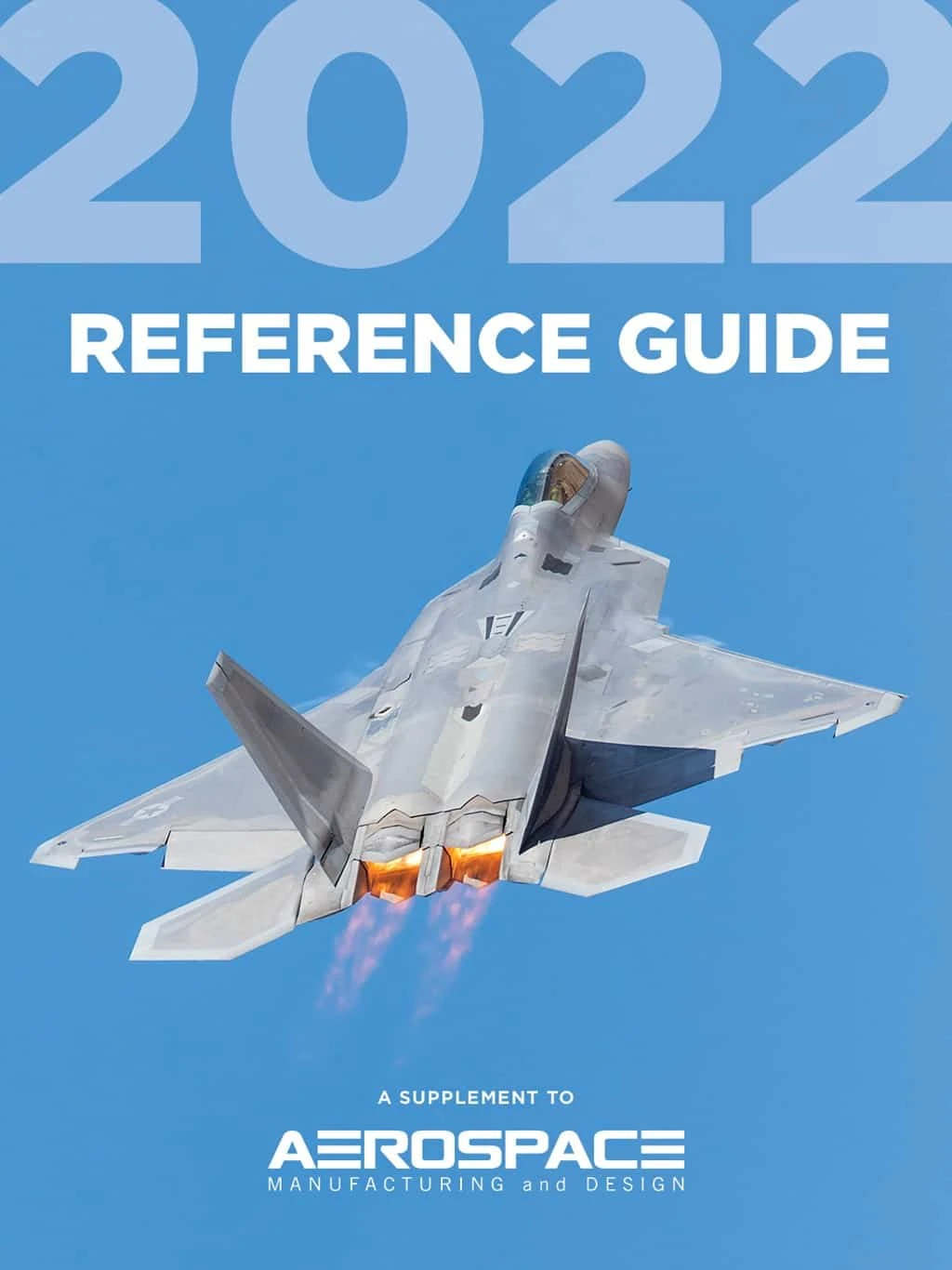
Explore the AMD Reference Guide 2022 Issue
Check out more from this issue and find your next story to read.
Latest from Aerospace Manufacturing and Design
- AAMI project call submission deadline extended to May 12
- Jergens launches cast iron tooling column additions
- Airbus to acquire assets relating to its aircraft production from Spirit AeroSystems
- FANUC America's Cobot and Go web tool
- Chicago Innovation Days 2025: Shaping the future of manufacturing
- High-density DC/DC converters for mission-critical applications
- #59 - Manufacturing Matters: Additive manufacturing trends, innovations
- ACE at 150: A legacy of innovation and industry leadership