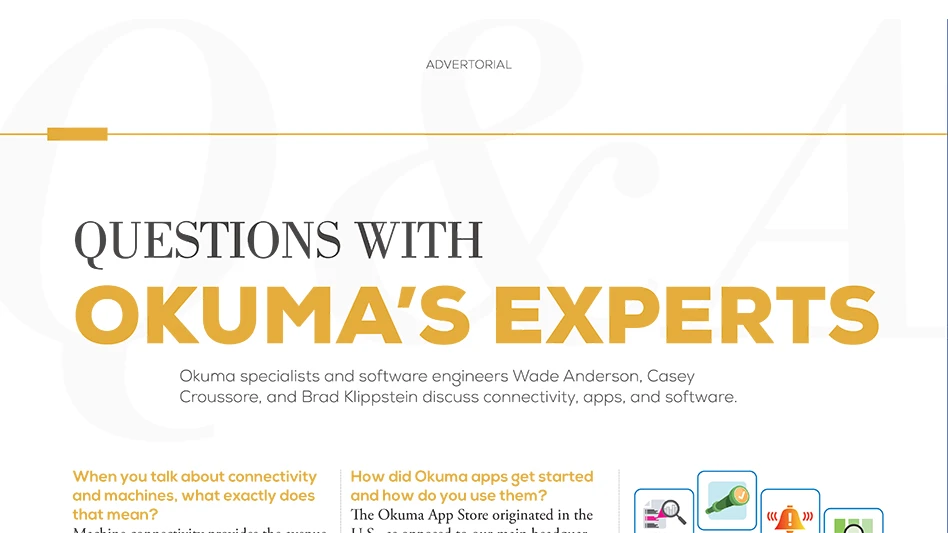
GIE Media

When you talk about connectivity and machines, what exactly does that mean?
Machine connectivity provides the avenue to help you better understand the digital assets you already own. It’s the first step to applying automation to your machine technology, so that you can use the technology to its fullest potential.
Maybe you didn’t know that automation techniques can be applied to your software as well. By connecting your equipment, you can enhance processes, incorporate logic into your operation, and prioritize scheduling. Integrating your shop floor can enable you to track and trend setup times, cycle times, alarm conditions, spindle loads, and tool life. All of this can increase your productivity by identifying critical, real-time shop floor information.
MTConnect is a great conduit for this information, since it’s a free, open-source solution that connects multiple devices into a common data stream. New Okuma machines come with the software pre-installed from the factory – ready for you to plug into all potential benefits.

How did Okuma apps get started and how do you use them?
The Okuma App Store originated in the U.S., as opposed to our main headquarters in Japan. The idea was to create a user-friendly, common place for Apps that had already been written for various machines. App Store Apps have been written by Okuma software engineers, our distributors, our partners, and even some customers. The open-architecture platform gives our customers complete control over their machines.
If you have experience with .NET programming, you have the power to create your own Apps from the ground up. Our application programming interface (API) comes with the purchase of an Okuma machine. The API is a library that connects what the machine sees (NC side) to what you see (Windows side) so you can code Apps to match specific needs.
What is a unique piece of software that you don’t typically hear about?
Our servo-navi software, essentially, is a feature that allows operators to optimize cutting processes by accelerating or decelerating cycle rates based on workpiece weight and cutting complexity. For example, the servo-navi process could slow down machining on heavy workpieces to improve quality of axis movements and then continually optimize the speed of the machining process as the workpiece becomes lighter. The result: optimized cycle times, optimized cutting performance, optimized finished part. It’s a great feature that comes on most of our lathes and machining centers.
For more information:
https://www.okuma.com
Get curated news on YOUR industry.
Enter your email to receive our newsletters.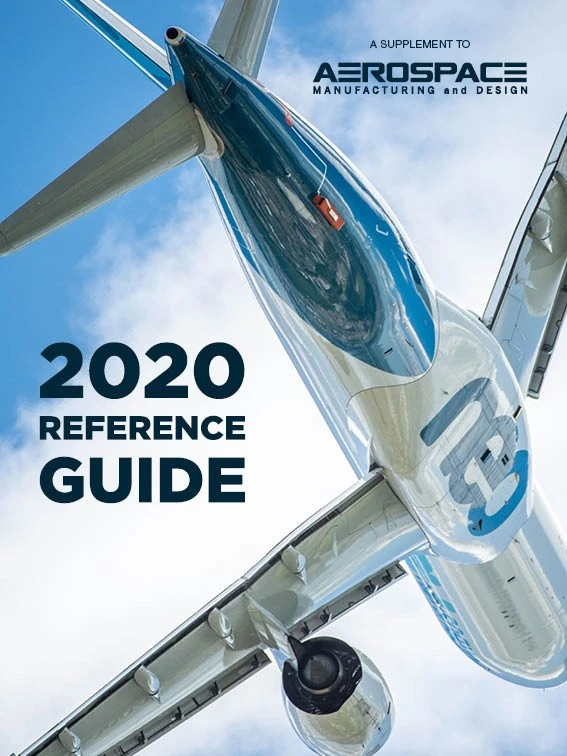
Explore the AMD Reference Guide 2020 Issue
Check out more from this issue and find your next story to read.
Latest from Aerospace Manufacturing and Design
- GE Aerospace secures Air Force engine contract
- Thomson Industries' online sizing and selection tool
- #53 - Manufacturing Matters - 2024 Leaders in Manufacturing Roundtable
- Join us for insights on one of the hottest topics in manufacturing!
- You can still register for March’s Manufacturing Lunch + Learn!
- Ohio creates Youngstown Innovation Hub for Aerospace and Defense
- Tormach’s Chip Conveyor Kit for the 1500MX CNC Mill
- How to Reduce First Article Inspection Creation Time by 70% to 90% with DISCUS Software