
GIE Media

1 My parts have been laser printed. Is cleanliness still a concern?
Generally, laser printed parts are free of oils and coolants; however, we’ve seen build plates with contamination that’ve been resurfaced via conventional machining. Often post-additive manufactured (AM) geometries hold residual oils and debris, which if not removed, can discolor and contaminate your build. Also, consider extraneous powder inside the build itself. While these powder particles may not affect the build’s integrity, they may end up deposited on your furnace shielding and heating elements.

2 To keep my build bright and clean, what vacuum levels should be achieved when stress relieving, annealing, or aging?
Many new additive AMS specifications provide guidance on vacuum levels to maintain (i.e., 1x10-4 Torr or lower or <5x10-5 Torr) during processing. These vacuum levels in a clean, baked-out furnace with clean fixturing should be easy to achieve and maintain. Limiting leak rates to 5 or 10 microns/Hg per hour is important when processing many titanium alloys, PH grades, and all zirconium/niobium alloys.

3 How do I ensure proper temperature on my AM part?
Use calibrated/surveyed furnaces along with contact work thermocouples (Work T/Cs). If Work T/Cs can’t be placed into the part, place them into a representative cross-sectional thickness block of the same alloy. In many cases, placement of Work T/Cs in AM parts is different. Consider 0.250" thick printed parts on a 12" sq. build plate that’s 3" or 4" thick. Build plates act as heat sinks and prevent printed parts from reaching the required temperature for the full amount of time specified, so place a Work T/C in the thickest portion of the build plate for reference.
4 My furnace is clean, parts are clean, what else should be considered?
Know the purity and dew point of your process gasses (nitrogen, argon, helium, and hydrogen), and check oxygen levels. The furnace can be tight, clean, and hold a deep vacuum for the duration of the run but cooling with contaminated process gas can ruin the load. Solar has written extensively on process gas purity and how to properly monitor gas quality.

5 My build contains many different cross-sectional thicknesses/geometries. How can I minimize distortion?
Some complex geometry builds never uniformly heat or cool, leading to distortion. Solar has a video outlining steps to minimize distortion by stress relieving, and it discusses heating ramp rates, cooling rates, and thermocouple differentials. See if those variables fix the problem. Recently we had a complex build that varied from 0.090" to 1" thick with holes, vents, pockets, and large voids. We convinced the customer to print a 3D clam shell (two halves) to place around the part for more uniform heating and cooling.
FOR MORE INFORMATION:
Solar Atmospheres

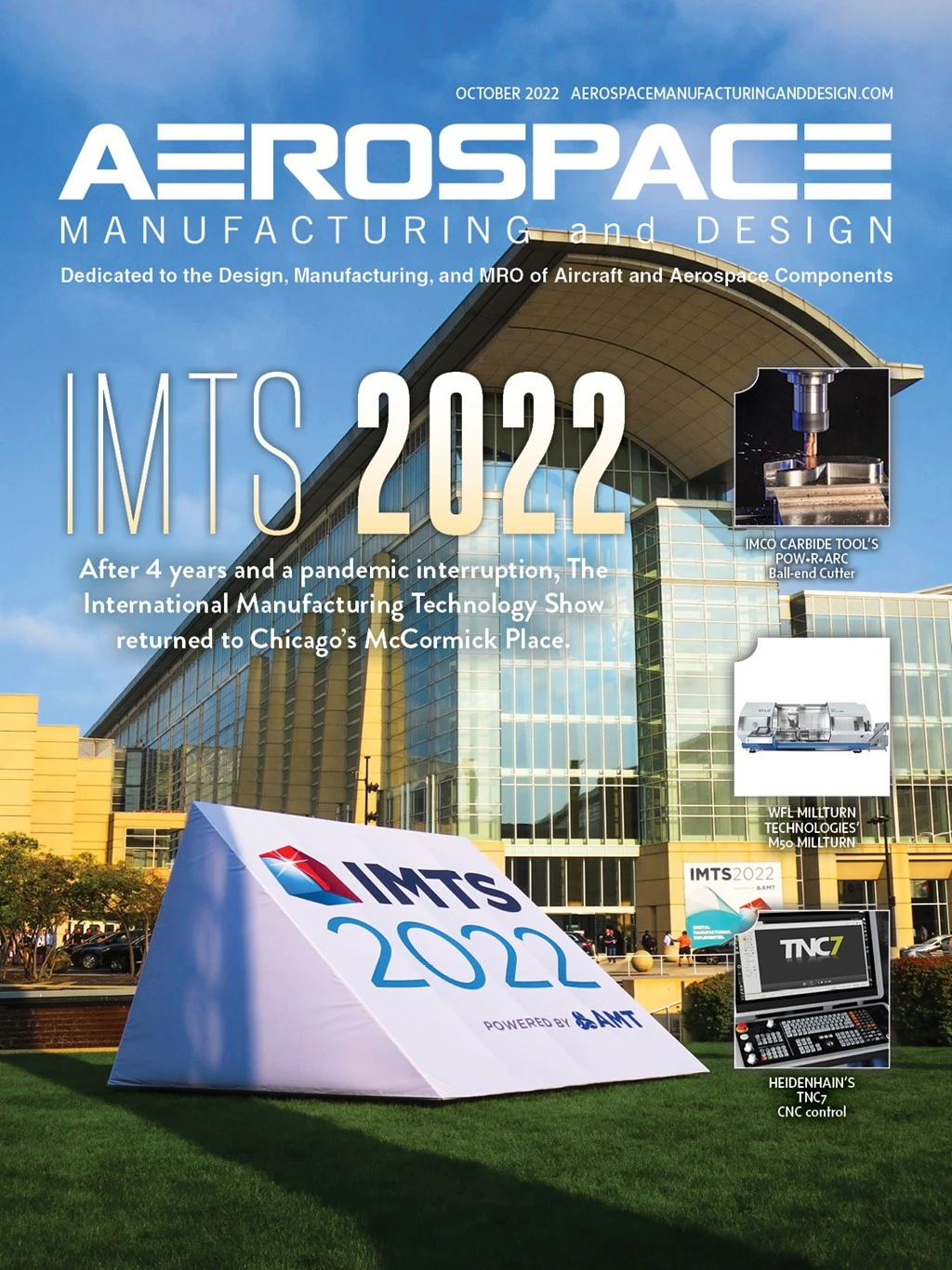
Explore the October 2022 Issue
Check out more from this issue and find your next story to read.
Latest from Aerospace Manufacturing and Design
- BOC Aviation orders 120 Airbus, Boeing jetliners
- Mazak’s INTEGREX j-Series NEO
- Embraer tests wing for new technologies demonstrator
- Mitutoyo America’s SJ-220 portable surface roughness tester
- #55 - Manufacturing Matters - A Primer on Defense Contract Manufacturing
- Registration is open for April’s Manufacturing Lunch + Learn!
- Natilus begins search for new home to build world's most efficient commercial aircraft
- Aerospace Industry Outlook webinar is back by popular demand