
GIE Media

1) Can LT-FREE improve shop safety?
Sawing, milling, and grinding often involve an exposed cutter within the operator’s reach, subjecting the operator to a significant injury risk. With LT-FREE, all cutting and marking happens in a safety-interlocked enclosure, allowing the operator to monitor machine operation from outside of the working area.
2) What are the advantages of laser cutting?
Laser cutting accuracy and repeatability are significantly better than traditional processes, as the laser beam does not wear or cause part deformation. Because laser hardware never touches the part, materials can be oriented in any direction, allowing them to be cut in any shape. Precision cuts made by lasers often require little to no post-processing. Highly focused energy and pressure allow cutting a much smaller area of material, significantly reducing thermal damage and scrap. Fiber laser technology can process highly reflective metals such as aluminum, copper, and brass.

3) What type of aerospace components are best suited for 5-axis laser cutting?
Any metal component requiring through-thickness cutting: hydroformed components, bent pipes and tubing, deep-drawn components, heat shields, cooling lines, hydraulic and fuel lines. We can cut materials such as stainless steel, nickel-base alloys (Inconel, Incoloy), cobalt allows, brass and copper. These materials are susceptible to work hardening that can prematurely wear conventional cutters, but this is never the case with lasers.
4) What type of configurations are available?
The LT-FREE complete family of machines offers various configurations for different features – optimized loading, robotic flexibility, compact fixed table operations – depending on the application.
BLM LT-FREE integrated robot handling eliminates restaging parts, delivering better accuracy and greater repeatability.
5) What are the challenges of operating an LT-FREE?
LT-FREE’s human-machine interface (HMI) eliminates complex machine programming and the need for laser machining expertise. From the 3D preview of the part, users can move or rotate any geometry with one click or add micro joints if necessary. Active Tools put laser technology know-how inside the machine
- Active Speed automatically optimizes parameters at actual speed without operator input
- Active Piercing improves piercing quality, reliability; process monitoring available
- Active Focus changes laser focus for each geometry; simplifies complex part management
- Active Grippers adds input/output (I/O) options, active tool management for high-accuracy applications; inputs can monitor contact points between part and fixture to identify non-compliant, incorrectly positioned parts
- Active Restart allows LT-FREE to restart after any stop position; minimizes part waste, maximizes efficiency
- Active Power onboard power meter qualifies laser intensity to certify final product was not exposed to excessive energy
For more information: https://www.blmgroup.com
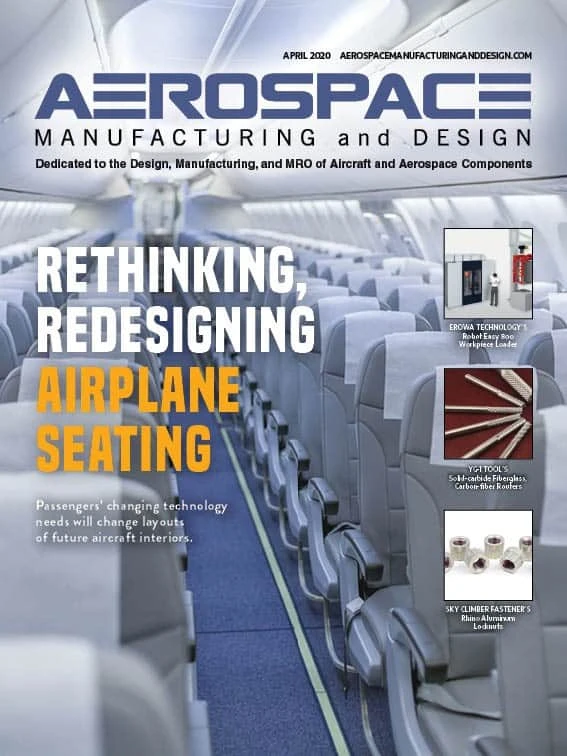
Explore the April 2020 Issue
Check out more from this issue and find your next story to read.
Latest from Aerospace Manufacturing and Design
- Piasecki acquires Kaman's KARGO UAV program
- PI Americas’ long-travel XY piezo nanopositioners-scanners
- AAMI project call submission deadline extended to May 12
- Jergens launches cast iron tooling column additions
- Airbus to acquire assets relating to its aircraft production from Spirit AeroSystems
- FANUC America's Cobot and Go web tool
- Chicago Innovation Days 2025: Shaping the future of manufacturing
- High-density DC/DC converters for mission-critical applications