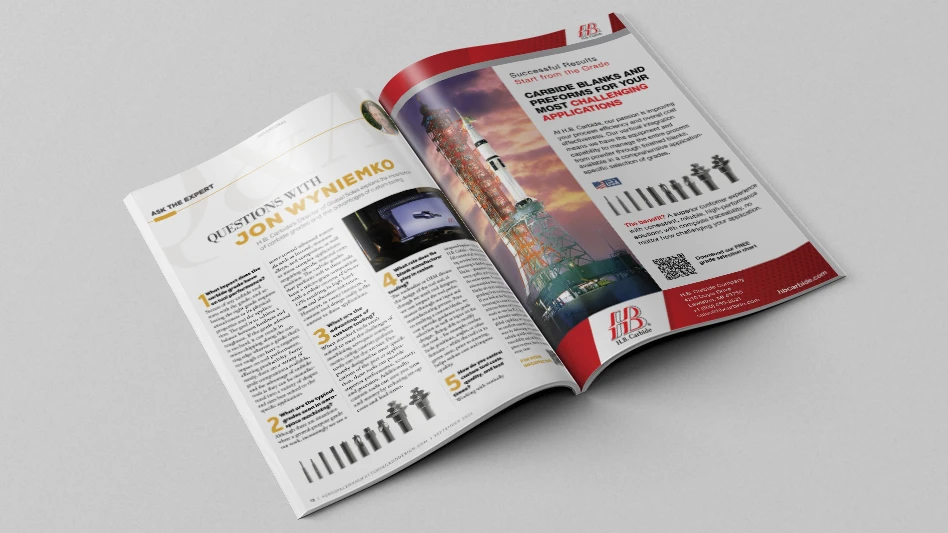
GIE MEDIA
1. What impact does the carbide grade have on tool performance?

Success of any carbide tool starts with the grade, and selecting the right grade requires attentiveness to its physical properties and the application. The goal is to achieve a balance between hardness and toughness. If the grade selected is too hard, it can result in micro-chipping along the cutting edge whereas a grade that’s too tough can have a negative impact on tool performance, affecting productivity. Fortunately, there are a variety of grade compositions available, and the advantage of carbide tools is they can be manufactured into a variety of shapes and sizes best suited to the specific application.

2. What are the typical grades seen in aerospace machining?
Although there are situations where a general-purpose grade can work, increasingly we see a move toward advanced materials such as Inconel, titanium alloys, and composites, as well as more complex applications requiring specific material composition. The carbide grades that perform well in these tools have a micro-grain composition with a cobalt content of 6%-to-12% resulting in high hardness and abrasion-resistance. However, in many instances, a custom tool design really is the answer to these applications.
3. What are the advantages of custom tooling?
When standard tools aren’t suited to meet the challenges of machining aerospace components, using custom preform tools can be the answer. Purposely designed to meet specifications of the part or application, these tools can provide superior performance, accuracy, and precision. Additionally, custom tools can save you time and money by reducing set-up costs and lead times.
4. What role does the blank manufacturer play in custom tooling?

The toolmaker or OEM dictates the design of the tool and, although we aren’t tool designers, we can impact the tool performance through our input and manufacturing process. Prior to making a custom blank, we can provide guidance in grade selection as well as input on the design. Being able to modify the tool – for example, coolant hole positions, angles, or other features – while the tool’s in its green state, prior to sintering, helps reduce cost and improve quality.
5. How do you control custom tool costs, quality, and lead times?
Working with vertically integrated suppliers such as H.B. Carbide – where we have full control of all manufacturing activities from powder processing to finished ground blanks – guarantees consistency, quality, and control of the entire process. It can be a misconception that custom blanks are more expensive than grinding from a standard blank. If you look at the big picture, investing in a custom tool that achieves shorter cycle times can result in very fast ROI. Plus, as a domestic company with global capability, we can provide an excellent customer experience by delivering any grade of carbide quickly with complete traceability and reliability – piece-to-piece, batch-to-batch, every time.
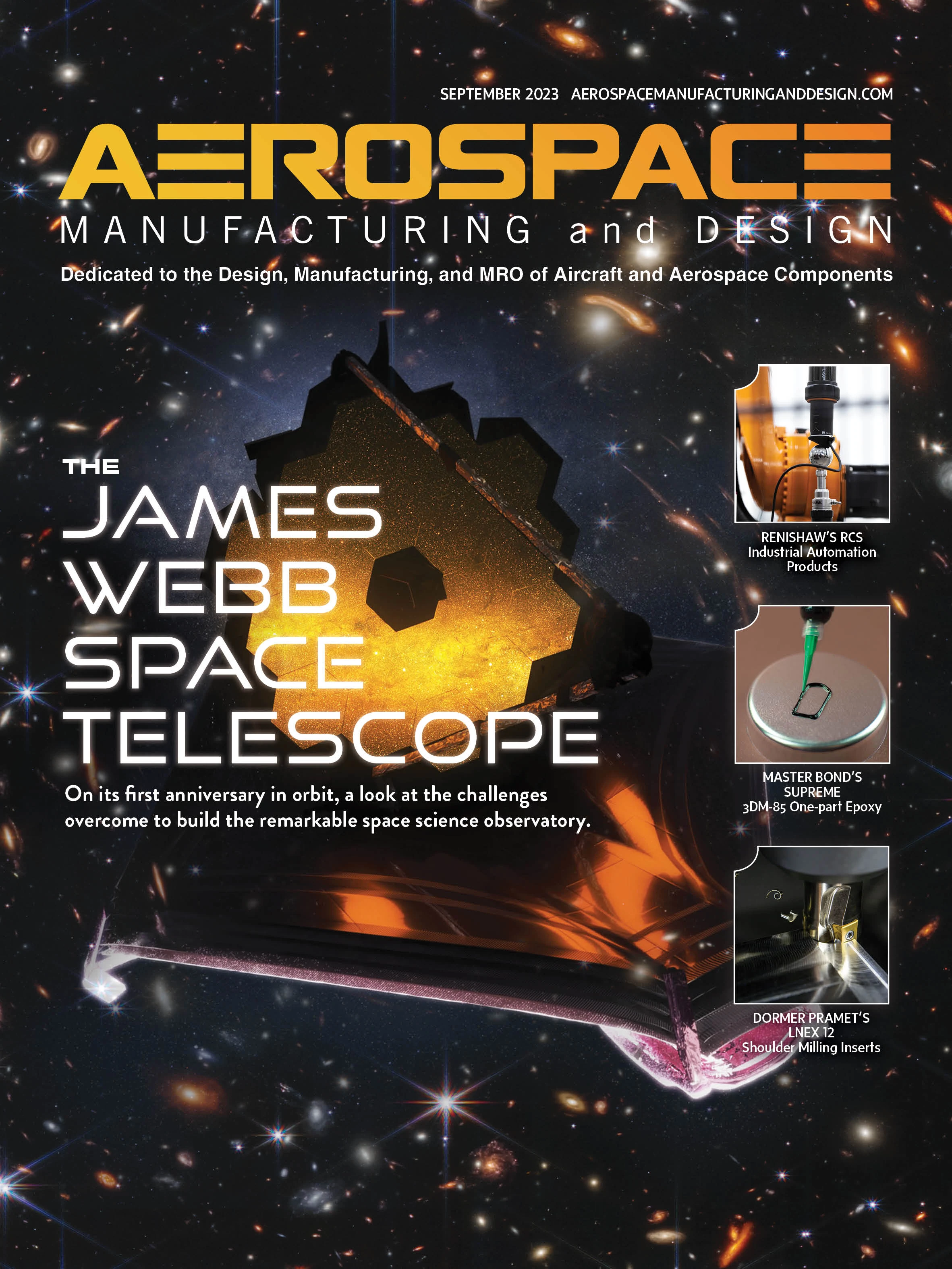
Explore the September 2023 Issue
Check out more from this issue and find your next story to read.
Latest from Aerospace Manufacturing and Design
- Titanium drop bottom furnace installation underway
- Solid carbide taps for demanding materials
- The Partner Companies acquires Precision Eforming
- Hall Effect angle sensors
- July is for learning – so drop in for this month’s second Manufacturing Lunch + Learn
- Essential strategies to protect your data
- NASA selects instruments for Artemis lunar terrain vehicle
- Twin-cutter boring head