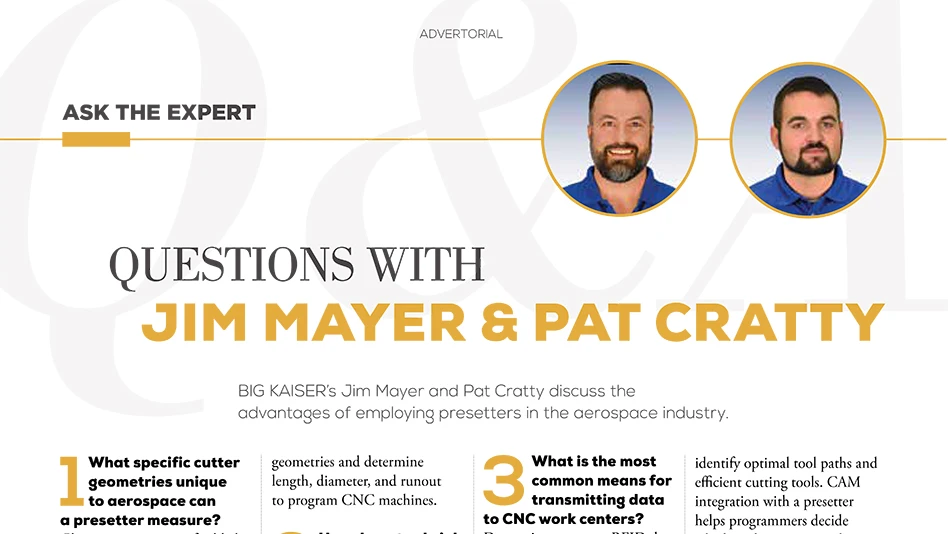
GIE Media
1. What specific cutter geometries unique to aerospace can a presetter measure?

Christmas tree cutters for blade milling accurately cut material and provide required surface finish. Historically, these form tools are measured in the CNC machine with probes, meaning the spindle isn’t running. Other legacy measuring methods reduce the ability to measure runout and don’t define any suspect cutting edges. Using a presetter’s scanning function, an operator can measure unique geometries and determine length, diameter, and runout to program CNC machines.
2. How do auto shrink presetters benefit shops in the aerospace industry?
Having a presetter/auto shrink combo to set the tool length within 0.0002" tolerance offers many benefits to aerospace shops. Anyone doing tight tolerance 5-axis machining knows clearance and collision avoidance are essential. Precisely controlling the stick-out length of shrink-fit tools significantly reduces the likelihood of crashes and improves surface finishes.
3. What is the most common means for transmitting data to CNC work centers?
Data written onto an RFID data chip at the presetting station can be read by the machine tool, providing quick, accurate data transfer. RFID solutions also ensure that the tool holder is loaded into the correct pocket of the tool magazine. A recent advancement for transferring data from a presetter to a machine tool is SPI, a hands-off post-processor interface from Speroni. There are multiple ways to deploy SPI, including linking directly from the presetting station to a machine tool using a handheld wireless scanner. This scanner can post offsets to various machine tools and is configurable to meet workflow requirements.

4. How do most aerospace companies get tool data into the presetter station for tool assembly?
Most use CAM integration to get tool data to the presetter, eliminating the need for paper setup and preventing human error and information loss if the paperwork is misplaced. CAM software allows programmers to identify optimal tool paths and efficient cutting tools. CAM integration with a presetter helps programmers decide which tools to use to make a specific part and which tool components are available by accessing the tool and adapter management feature in the presetter’s software.
5. My machines have a touch probe. Why do I need an offline presetter?
Touch probes and lasers in a CNC machine are a great way to spot-check tools, but machine tools are not made to measure tooling. Offline presetters measure tools efficiently and accurately, keeping the spindle running. Touch probes and lasers are dedicated to a single machine. An offline presetter can set tooling that goes into multiple machine tools. Touch probes also have difficulty measuring tools with unique geometries, such as step drills, and can’t identify the first thread on a tap. Offline presetters identify tool wear with a camera, ensuring accuracy where a tool probe and laser can’t.
For more information: https://www.bigkaiser.com
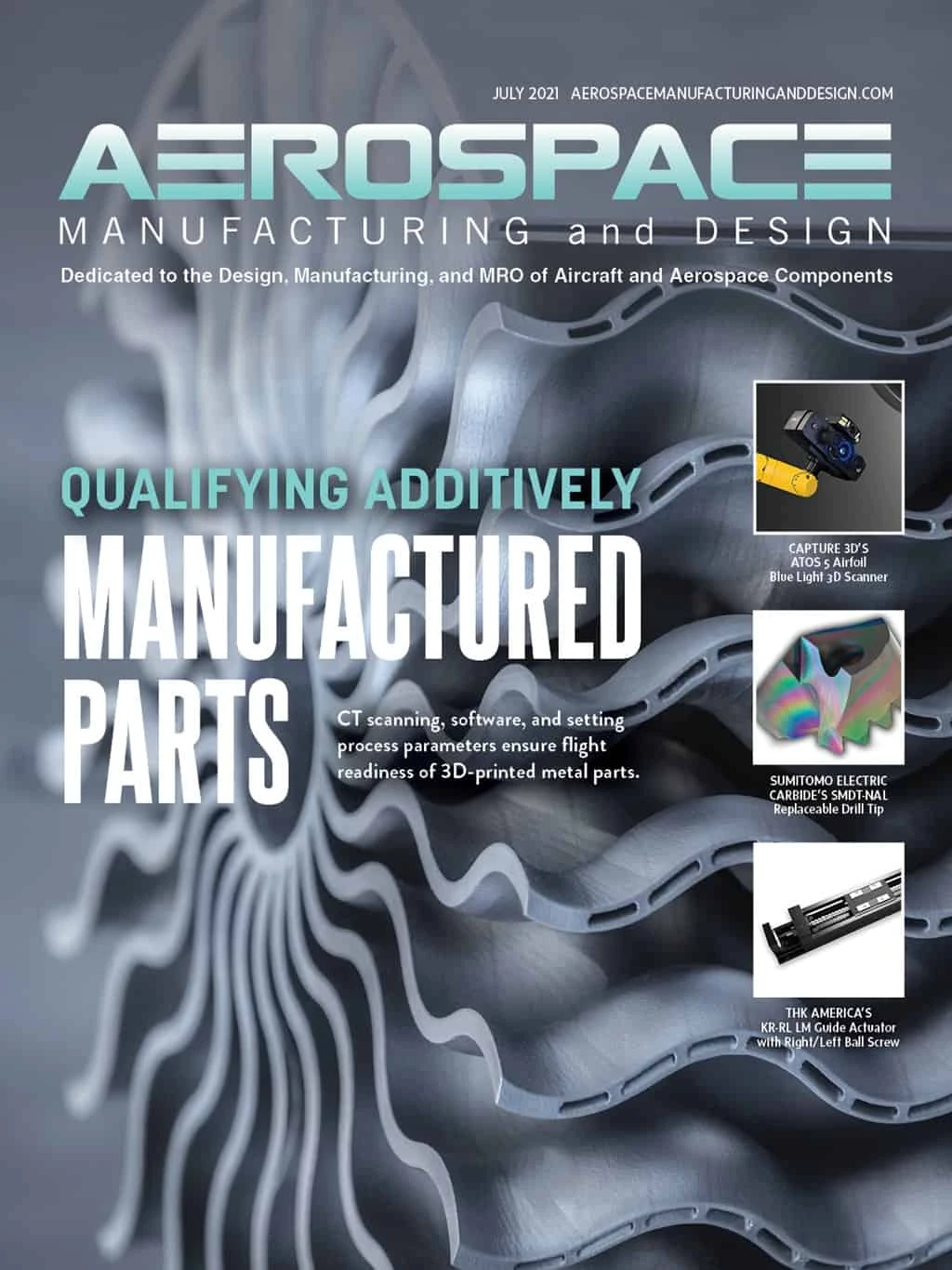
Explore the July 2021 Issue
Check out more from this issue and find your next story to read.
Latest from Aerospace Manufacturing and Design
- UT researchers receive Air Force grant for wind tunnel
- Monticont's linear voice coil servo motor
- FAA certifies Pratt & Whitney GTF engine to power the Airbus A321XLR
- Wevo's silicone gap filler
- Daher Learning Center inaugurated
- HEMCO Corporation's UniFlow CE AireStream fume hoods
- IMTS 2024 Booth Tour - Niigata
- PNAA announces ADVANCE 2025