
GIE Media

1) Why is stainless steel used in production parts?
It offers an ideal balance of strength with thermal and corrosion resistance. It indicates that whatever product is made from stainless is going to last. All these benefits explain why many industries, such as aerospace, use this as a primary material.
2) What makes stainless steel different from other steels?
It’s critical to understand the material you are machining. This means knowing the material’s chemical composition and physical properties. Knowing the alloying elements and any processes used to shape it play a large factor in the material’s machinability. Stainless is a version of steel, but with decreased iron and carbon and an increase of various alloying elements that make up that vacancy. These alloying elements improve its strength, heat/corrosion resistance, workability, hardenability, weldability, etc. The downside is, while these add good qualities to the material, it often adds difficulties to the machining process.
3) What are some of the main alloying elements, and how do they impact the material?
4) What are some of the main alloying elements, and how do they impact the material?
Chromium is the primary alloying element in stainless steel, having a minimum of 10%, and is one of the main contributors to making the material difficult to machine. It’s what makes the steel stainless by creating a layer that oxidizes when exposed to air to help prevent corrosion.
Nickel, the next largest alloying element in stainless steel, increases its strength and toughness, which decreases its machinability. Silicon and tungsten also provide additional hardness. Stainless steel can be difficult to harden, so copper, boron, and molybdenum can be added to help. Lead and sulfur can also be added to increase machinability.
5) What are some application tips, and is a specific style of machining best suited for stainless steel?
When machining stainless, it’s critical to make sure the coolant is clean and in good condition. Coolant is always required due to stainless steel’s poor thermal conductivity, which can vary from grade to grade depending on the composition. There isn’t a specific style of machining best suited for stainless. Rate adjustments are needed when cutting this material, but there isn’t a specific tool path.
6) What geometry should you consider when machining stainless steel?
First, you want a moderately high rake angle, balanced between strength and shearing capability. A higher helix (between 35° and 50°) adds to that shearing capability. A high relief is needed to avoid rubbing and creating excess heat. The core needs to be balanced to be strong without sacrificing chip space. Keeping the cutting edge in good condition should be prioritized by running appropriate rates and having good coolant. Once the cutting edge begins to break down, the tool will wear exponentially.
For more info: https://www.kyocera-sgstool.com
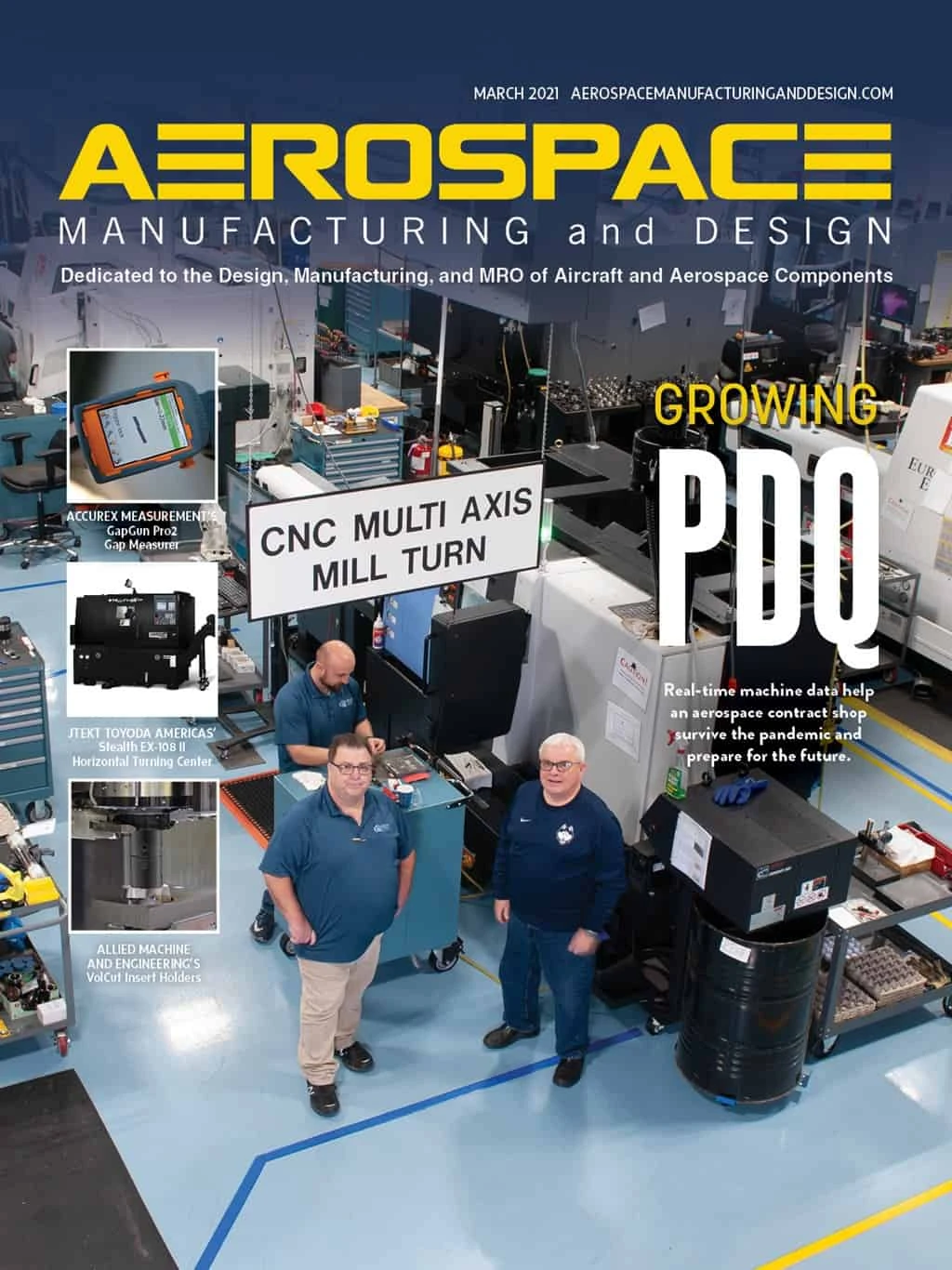
Explore the March 2021 Issue
Check out more from this issue and find your next story to read.
Latest from Aerospace Manufacturing and Design
- AAMI project call submission deadline extended to May 12
- Jergens launches cast iron tooling column additions
- Airbus to acquire assets relating to its aircraft production from Spirit AeroSystems
- FANUC America's Cobot and Go web tool
- Chicago Innovation Days 2025: Shaping the future of manufacturing
- High-density DC/DC converters for mission-critical applications
- #59 - Manufacturing Matters: Additive manufacturing trends, innovations
- ACE at 150: A legacy of innovation and industry leadership